The longer a surveillance aircraft can stay aloft and on station, the less time it wastes in transit. But if the aircraft is too lightweight, it could flex and crash in the winds. The U.S. Navy is looking at a solar-powered design whose engineers have taken up the challenge. Keith Button spoke to the CEO of Skydweller Aero.
The Skydweller solar-electric plane has a wingspan longer than a 747’s but weighs just 2,500 kilograms. When this remotely flown craft lands at Stennis International Airport in Mississippi, two technicians riding electric scooters must grab short poles under the wings and steady the plane on its two center wheels as it slows. This prevents either end of the massive span from scraping the runway.
This wingspan and low weight are the key factors that have permitted the design to stay aloft for up to 22.5 hours so far, with 90 days being the ultimate aim. But the long span also makes Skydweller susceptible to wind gusts that could flex its wings and tear apart the carbon frame covered in solar cells on the upper surface.
“That’s what’s killed every other solar-powered aircraft to date,” says Robert Miller, head of Skydweller Aero, the Oklahoma City company developing the plane. “You’ve got to understand aeroelasticity,” he says, referring to the science of predicting the flexing of an aircraft’s structure under aerodynamic and inertial forces.
Other contestants in the race to build a “perpetual flight” airplane that flies for months at a time have crashed because of the issue. AeroVironment’s unoccupied Helios prototype broke apart and crashed into the Pacific Ocean in 2003 after encountering turbulence, and an unoccupied Zephyr prototype built by Airbus crashed in 2022 due to storm turbulence.
Now, in a new round of test fights from Stennis that began in February, engineers hope to prove that their solutions can keep Skydweller aloft for days at a time consistently. They want to show their sponsors, the U.S. Navy and U.S. Southern Command, that the plane could be a cheaper, longer-flying alternative to jet-fuel-powered drones for tracking drug-runners, smugglers and other nefarious characters at sea. Miller declined to provide the contract amount for this year’s flights, but the 2024 flights were funded under a $5 million Navy contract.
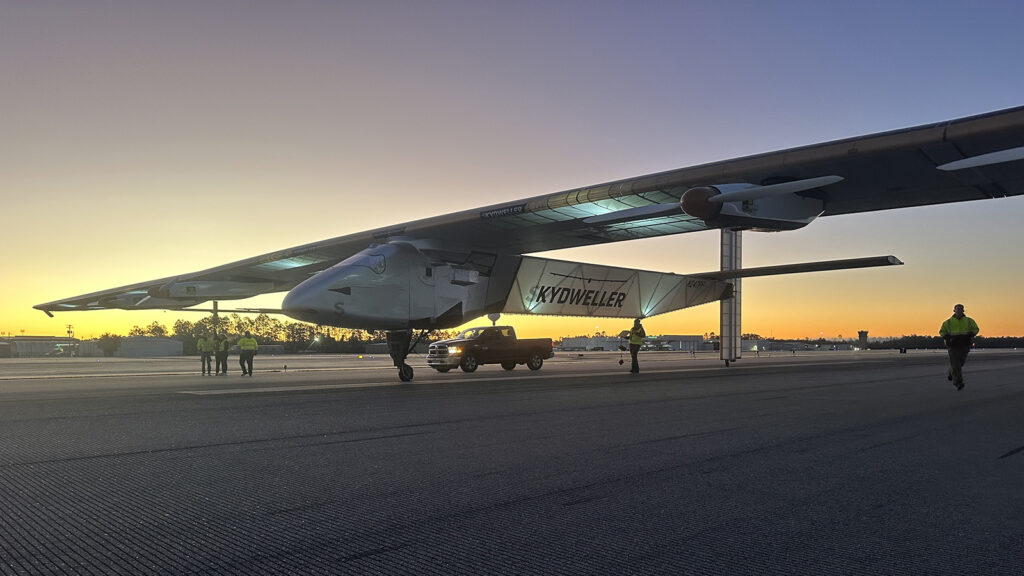
The idea is to take another step toward the 90-day goal by demonstrating that the design can reliably operate its sensors and communication links and stay aloft for about seven days — roughly four times longer than can be done by MQ-9 Reapers, the remotely piloted drones that were commonly flown by U.S. forces over Afghanistan and Iraq. Miller envisons that someday, each Skydweller would carry 360 kgs of batteries, communications equipment, cameras and other sensors needed to link to satellite or radio signals. Like Reapers, they could be operated from anywhere with a keyboard and mouse, Miller says — but at a much lower cost. “If I’ve got internet, I can talk to it.”
Last year, the plane was flown from Stennis in August and September for a series of tests that included the 22.5-hour flight over the Gulf of Mexico — or America, as President Trump has renamed it.
Miller saw surveillance potential in Skydweller’s predecessor, the onboard-piloted Solar Impulse 2, and teamed up with venture capital backers to acquire it for an undisclosed price in 2019. Three years before, Solar Impulse 2 had become the first solar-powered plane to fly around the world, piloted on alternate legs of the journey by Solar Impulse co-founders Bertrand Piccard and André Borschberg. For Miller, the plane showed promise at the time as a lower-cost, longer-loitering alternative to conventional drones for sensor missions, such as those that required a “virtual hover” flight speed and a large payload capacity for carrying forest-canopy-penetrating radar.
Part of making Skydweller resilient in gusting winds involves flight control software, which Miller and his team built as they adapted the piloted Solar Impulse 2 to become autonomous. Skydweller’s airframe is nearly unchanged from Solar Impulse 2. By designing the software to fly the plane through turbulence, the engineers could keep the carbon structure as light as possible without causing the wings to break apart when shaken by wind gusts.
They started by building a computer model of the aircraft, from which they developed an aerodynamic model and a structural model. The structural model showed how much the plane would twist or bend when it encountered loads, such as wind gusts. They also modeled how the aerodynamics changed when the plane’s structure was deformed, such as when the wing tips tilted up at a certain angle.
Next, they needed to find out how the plane would respond to vibration caused by winds, so they performed ground vibration tests. They attached accelerometers to the wing, tail and fuselage to measure the response when the plane was vibrated by a shaker. They also recorded accelerometer readings when the plane’s wings and control surfaces were tapped by a small hammer.
With these readings about the plane’s responses to vibration, they updated their structural models. The readings also helped determine where to place accelerometers on the plane’s wings for in-flight tests. Then they directed it into turbulence to see how it responded, and to verify that what their models predicted was accurate in flight.
“You go out and look for stuff to shake you up a little bit,” Miller says.
At the same time that they were building their computer models of the plane and tuning them with measurements from actual flights, the engineers were also developing and tweaking the flight control software. Miller declined to go into specifics, but in general, the software moves the control surfaces on its wings and tail in real time to unload lift created by wind gusts. This prevents damage from extreme twisting or vibration by gusts, like the severe wing bend that occurred on AeroVironment’s Helios before it broke apart and crashed. The software’s flight adjustments also helps control Skydweller better, such as when it encounters crosswinds during a landing.
There are other unique techniques for flying a plane with the wingspan of a 747, Miller says: The plane needs to bank and turn slowly, for example, because of the difference in speed between the outer and inner wingtips. The plane’s cruising speed is 43 kilometers per hour.
“As you get larger, and we’re much larger, aeroelasticity doesn’t scale,” he says. “It gets much harder.”
Skydweller flies as high as 45,000 feet as a means of energy storage, so it can descend slowly overnight and use up less of the battery power that drives its four propellers. Because the plane flies in the 5,000- to 30,000-foot “solar-powered aircraft death zone” of the atmosphere where weather occurs, avoiding turbulence has been another key issue to contend with, Miller says. The engineers needed to build an automated weather prediction and avoidance software package.
They developed cloud-based software that receives live feeds of weather data and predicts where thunderstorms and the resulting winds will occur so that the plane can avoid them. The software turns bad weather and dark clouds into obstacles for the plane’s onboard flight software to avoid, much like a 3D obstacle course.
“We encapsulate that bad weather and make it into a solid obstacle,” Miller says.
Algorithms chart a flight path through the obstacles while also maximizing surveillance collection capabilities for a given mission and collecting enough sunlight for the plane’s batteries for flying at a high enough altitude to make it through the night. Clouds that obscure the sun must also be avoided so that the solar cells that plaster the top surfaces of its tail, fuselage and wings can keep the batteries charged.
“You want to make sure in the morning you’re not under a dark cloud,” Miller says. “You may not want to descend below a certain point at night, because in the morning you want to be at a certain altitude to avoid the clouds.”
As the plane becomes capable of flying longer and longer flights, another key issue will be redundancies: how to keep flying when something fails on the plane, Miller says. “Making an aircraft fly, by itself, is not that hard. It’s making it fly when not one, not two, but three things go wrong, and you want to bring it home and land it,” he says.
That’s where Skydweller’s large payload comes in. It can carry more backup communications, avionics and actuators than smaller-payload solar aircraft, Miller says. “There’s no single failure that can bring down the aircraft.”
“If you want to fly for 30 or 60 days, things are going to go wrong. It’s a probability thing,” he adds. For a plane to operate in real-world conditions and be more than “a science experiment,” it has to carry redundant equipment, he says.
For example, Skydweller’s engineers worked with actuator suppliers to develop backup motors to move control surfaces in the event the original motors failed. “That’s probably the toughest thing to get highly reliable.”
They knew they would need redundancy, but the question was how much. They built a systems integration laboratory in Oklahoma City consisting of a rack of servers with duplicates of the plane’s avionics and flight control computers, along with a test rack for the actuator motors that move the wing and tail control surfaces. At the lab, they moved the actuators as they would be moved in flight, under specific aerodynamic loads, and simulated in-flight failures for the actuators, electronics and backup actuators and electronics as those failures might be predicted by probability models. They tested how the plane’s backups would respond to, for example, an electrical component failing and rerouting power through another circuit. The simulations also helped them plan what less essential tasks could be abandoned in the event of a failure to keep the plane flying.
“Maybe you’ve got to shed some stuff that’s not important anymore because you don’t want to overload a power bus,” Miller says. “You spend a lot of time worrying about ‘Well, if this thing fails, how do I compensate and if that thing fails, how do I compensate?’”
They determined that quadruple redundancy — three backups for every potential failure point — would make the plane 99% reliable through a 30-day flight. Skydweller now has triple redundancies, and Miller is in the process of upgrading it to quadruple redundancies. Redundant flight computers “vote” when the logic in one fails, he says, and the majority determines which one is wrong.
“The most difficult thing is when you have two flight computers; it’s like a man with two watches who doesn’t know what time it is because he’s never sure which one is right,” he says.
Part of making Skydweller capable of flying longer has involved accumulating many small improvements in its solar cells, batteries, propellers, motors and weight reduction, Miller says. To decide whether the cost of a given improvement will be worth it, the engineers simulate how the update to, say, solar cells on the wings will improve the plane’s ability to stay aloft longer. One metric is the latitude at which the plane can operate during the worst day of the year for a solar-powered plane. That’s Dec. 22 in the Northern Hemisphere, the winter solstice and shortest day of the year. If a particular improvement would significantly widen the latitude band it could operate in year-round, then it might buy its way onto the plane.
“You slay this demon of perpetual flight by multiple cuts. It’s not one thing that kills it. You’ve got to attack it from 15 different ways,” Miller says. “Each one of those builds up a little bit more margin for you.”