Stay Up to Date
Submit your email address to receive the latest industry and Aerospace America news.
Venkat Viswanathan
Whether it’s reducing carbon emissions or limiting costly jet fuel consumption, there’s a lot to love about the idea of powering aircraft exclusively or in part with batteries. But the holy grail of purely electric passenger travel has remained frustratingly out of reach for decades, largely because delivering the required energy with today’s battery technology would make such aircraft impossibly heavy. Venkat Viswanathan, a professor at Carnegie Mellon University, is one of the researchers attempting to design a new class of batteries that would be lighter and would deliver more power. I called Viswanathan at his home office in Pennsylvania to discuss the challenges and external trends influencing electric flight.
IN HIS WORDS
Wanted: industry backing
If you look at the scale of investment in electric aircraft, it’s minuscule. A lot of these arguments are very similar to the arguments that people were making in 2003 when Tesla was founded: Electric vehicles can never be long range, can never charge fast and so on. It takes extraordinary willpower for some set of entrepreneurially minded people to be able to move the needle. We’re nowhere near the spending levels needed for driving this innovation and driving the technology forward. Part of it is also a challenge of where this development should reside. The traditional people who think about batteries don’t think about aviation, and the people who think about aviation typically don’t think about batteries. What’s needed is similar to the Tesla Effect, which is you need some company or something with a very strong, sustained effort to begin the electrification of aircraft to sort of bootstrap the traditional, more established people into this dimension. Otherwise, it’s very unlikely that we’ll see the kind of disruption that we saw in the vehicle space in the aviation space.
Moore’s law vs. Wright’s law
There’s actually been quite a lot of improvements in battery technology. But we frequently sort of compare it to Moore’s law and then ask the question, “Why haven’t batteries progressed?” Now, there’s actually a very interesting recasting of Moore’s law in the form of what’s called Wright’s law. The idea is that if you start making more of something, you learn how to make it better. So you will both learn how to do new things in a way, but also there’s a critical mass of people innovating and so on. It turns out that most energy technologies grow at roughly the same pace with the scale of production. For batteries, now that we’re seeing massive exponential scales of production, unit costs will start to go down. Now, at some point, you hit some limits of what’s possible with the chemistry of materials. Batteries will eventually approach that limit. We’re not there yet. I would say in the Moore’s law analogy, we’re probably in the 1980s or 1985, maybe. And there are still sort of 20 more years, or something like that; 10 more years, 20 more years of growth where we know the trajectory to getting better and better and better.
Reusability
The central technical problem comes to the question of single-use fuels compared to batteries that are used multiple times. Fuel you just burn once and then you emit the CO2, and then you move on with life. It’s easy to make energy sources that can be single use, so those can be very high-energy density, meaning lots of energy is stored per volume, and a higher density number is better. The reuse is what makes the energy density of batteries much lower than regular fuels. So depending on what state-of-the-art numbers you take, you get an energy source that’s roughly 10 times heavier than jet fuel, for instance. So now you can then ask the question, “Well, if that was the case, how are electric cars able to solve this problem?” What engineers have done is essentially make these cars heavier, so any electric vehicle is much heavier than the comparable internal combustion engine vehicle because the lower energy density of batteries means you need more of them. For aircraft, the problem comes from the fact that you need to generate lift. That’s when the weight hits you. The extra weight essentially forces you to ask for so much more power and so much more energy, which will need more batteries. And then you basically can’t close the design. So it’s a runaway train: You need more and then you add more, and then you need more, even more, and so on.
Power conundrum
Batteries are closed systems, which means that nothing comes in or comes out. When you have a closed system, you usually have this fundamental energy-power tradeoff. The easiest way in which you can visualize this is if you have an energy source, what happens is if you want very high power, then essentially you want to run very high currents through it. And because power is voltage times the current, to increase the power you need to increase the current. Now, when you increase the current, the amount of available energy loses a part that goes into heat. So as you try and increase the power, which is increasing the current, then you lose energy because of the fact that your resistive part of the energy loss now becomes much higher. You can then ask the question, “Could I do something smarter? Could I now make it such that I put more of the energy-containing components — which in a battery is the anode and the cathode — in the battery?” When you’re discharging the battery, you want to move ions from the anode to the cathode. Now, if you have more material on the cathode, in order to get all of the energy out you need to move the ion to all parts of the cathode, and you want to do that very fast because you want to get very high power. So one popular way in which you can make better batteries is to put more of the material; you can think of them as sheets stacked on top of each other, and you can make a bigger sheet. Then what happens is when the ions are moving, it’s easy for them to move, and then they can access the front part [of the battery]. But then it’s very hard for them to access the end part. So once you make thicker and thicker electrodes, you get less and less power.
Batteries compared to combustion
The energy content inside a tank of gasoline is way more than the energy that is stored in a battery pack, but the electric drivetrain is more efficient, as batteries are more efficient at converting chemical energy into useful work than burning fuels. So you need less overall energy to be able to move an electric vehicle than what you would need with the internal combustion engine counterparts. In that same way, an electric aircraft will need less energy, so as a result will need less energy density than the equivalent jet fuel-powered aircraft. But of course, that assumes that the weight of the battery pack doesn’t play a huge role. Jet engines need economies of scale because the bigger they are, the more efficient they are, and then you have two of them for redundancy, for safety. Essentially, you oversize it so much because it should be able to fly with just one, whereas electric motors are essentially still invariant: They’re equally efficient when they’re small as when they are very large. Which means that you can do these kinds of distributed propulsion concepts like the NASA X-57 plane, where instead of having just two engines, you have these 14 motors across the wing, and that then brings some aerodynamic efficiency and so on. There may be other ways in which you can get improvements.
Why lithium
The term lithium-ion is used for a broad range of technologies. Basically anything that uses lithium as the main carrying ion would technically fall under lithium-ion. Many of the things that people call “beyond lithium-ion” also still use lithium-ion. So solid state and all these things, it’s still lithium-ion as the working ion. In that sense, in the broader definition of lithium-ion, I think it’s nearly impossible for it to be any other ion because lithium is the lightest, and it’s the most electro positive, which means you’ll get the highest voltage out of your cell for the least amount of weight. To do that, you need to maximize the voltage and you need to minimize the weight. Lithium is the best for that at this point. Now having said that, the conventional way in which the term “lithium-ion” is used is that it refers to the kind of lithium-ion that we use today, which consists of graphite and some oxide cathode material. And then anything beyond that typically is called “beyond lithium-ion.” So battery chemistries that are changing the anode from graphite to silicon or lithium metal, those are seen as beyond lithium-ion, but they still use lithium-ion as the working ion from one side to another.
Exotic alternatives
Those would be lithium-ion based, but there are still battery chemistries even in lithium-ion that haven’t been explored, which I think would significantly move the needle. The are several very interesting ideas that are known to be much, much higher in energy density than current lithium-ion. If we look at single-use batteries, there are battery chemistries that would give something like 800-plus watt-hour per kilogram energy density. To compare, today’s best automotive cells provide around 250 watt-hours per kilogram. So that’s a significant step up, but we haven’t been able to make these single-use batteries rechargeable, so the economics just won’t work out. You need the battery to last several thousand cycles.
Rechargeability
The rechargeability question really comes hand in hand with the use case model, which is basically, “Would you fast charge the battery or would you slow charge the battery and swap the battery in an aircraft?” It seems to be that both are still on the table. So a plane lands, you charge the battery, and then it takes off again. That means the battery would have to be recharged in 30 minutes or so. Or you take it out and then you swap the battery and then slow charge the battery. The lifespan is hugely dependent on whether you fast charge or whether you slow charge. If you slow charge, then you have easily several thousands of cycles that are possible. Now, if you fast charge, then that comes down to a few hundred cycles. That’s the challenge that basically ties back to the use case, and of course the economics of the use case, which means that if you swap then you need more than one battery pack because the other battery is not being utilized for some time. That will also have a role to play.
Sorry, no electric 747
We have many, many solutions that we know for a fact can easily electrify flying taxi concepts for whatever distance it is you think you want: 100 miles, 200 miles, etc. Whether we have it today is, of course, up for debate, but we’ll have it. There’s no technological barrier to making it work; it’s simply just now finding the kinks and figuring them out. Now, if you think of something like a Boeing Dreamliner or the equivalent Airbus A380 aircraft, it gets very tricky. Then you’ll have to ask the question of how many passengers and how long. There is a limit beyond which it is essentially not feasible with any known technology today, of any known battery chemistry today — which means battery defined in the fashion of how we think about battery today. There are some hard limits. What that number is is a little bit tricky to exactly estimate. I couldn’t crisply tell you the boundary, but I think there will be an envelope of things that would be possible, and then beyond which it will not be possible. It’s safe to say that a wide-body aircraft that’s carrying something like 300 passengers would be essentially impossible with any known battery technology today.
Steady progression
It’s going to be a staged development: urban air mobility, and then short haul, maybe seaplanes, other kinds of small commuter aircraft; and then from there to maybe some more regional planes, and then eventually maybe something like a coast-to-coast type of thing. There’s a long way to go in terms of certifying aircraft. The systems have to get very, very high levels of reliability. Both the short haul and the urban air mobility are sort of ideal playgrounds to set up that certification process and thinking about these battery systems as propulsive batteries as opposed to how they’re seen today, which is that they are just for auxiliary power. For a vertical takeoff and landing aircraft capable of carrying a few passengers, the requirements and size of the battery pack would not be significantly different from that of a battery pack inside a typical electric vehicle, for example a Tesla Model 3, which means that the leap is not so large. We know how to manage these battery packs safely. Then from there, you can go to better battery system safety certification. You also need consumer faith and consumer adoption and so on. People should feel safe flying these things. So if these things come and become ubiquitous, then there will be a step change.
Lithium fire risk
If you think about it, it’s crazy that we go and pump flammable gasoline into our cars, and we feel totally safe. It’s very unlikely that, during use, a lithium-ion battery would have any sort of safety issues. The risk is mostly during charging; so if you charge your battery pack, that’s when you’re more likely to face these issues. But it’s the fear of the unknown, and that’s a fear that any new technology must face. So there’s still a while to go for this to get to the level where people are feeling comfortable and excited.

About cat hofacker
Cat helps guide our coverage and keeps production of the print magazine on schedule. She became associate editor in 2021 after two years as our staff reporter. Cat joined us in 2019 after covering the 2018 congressional midterm elections as an intern for USA Today.
Related Posts
Stay Up to Date
Submit your email address to receive the latest industry and Aerospace America news.
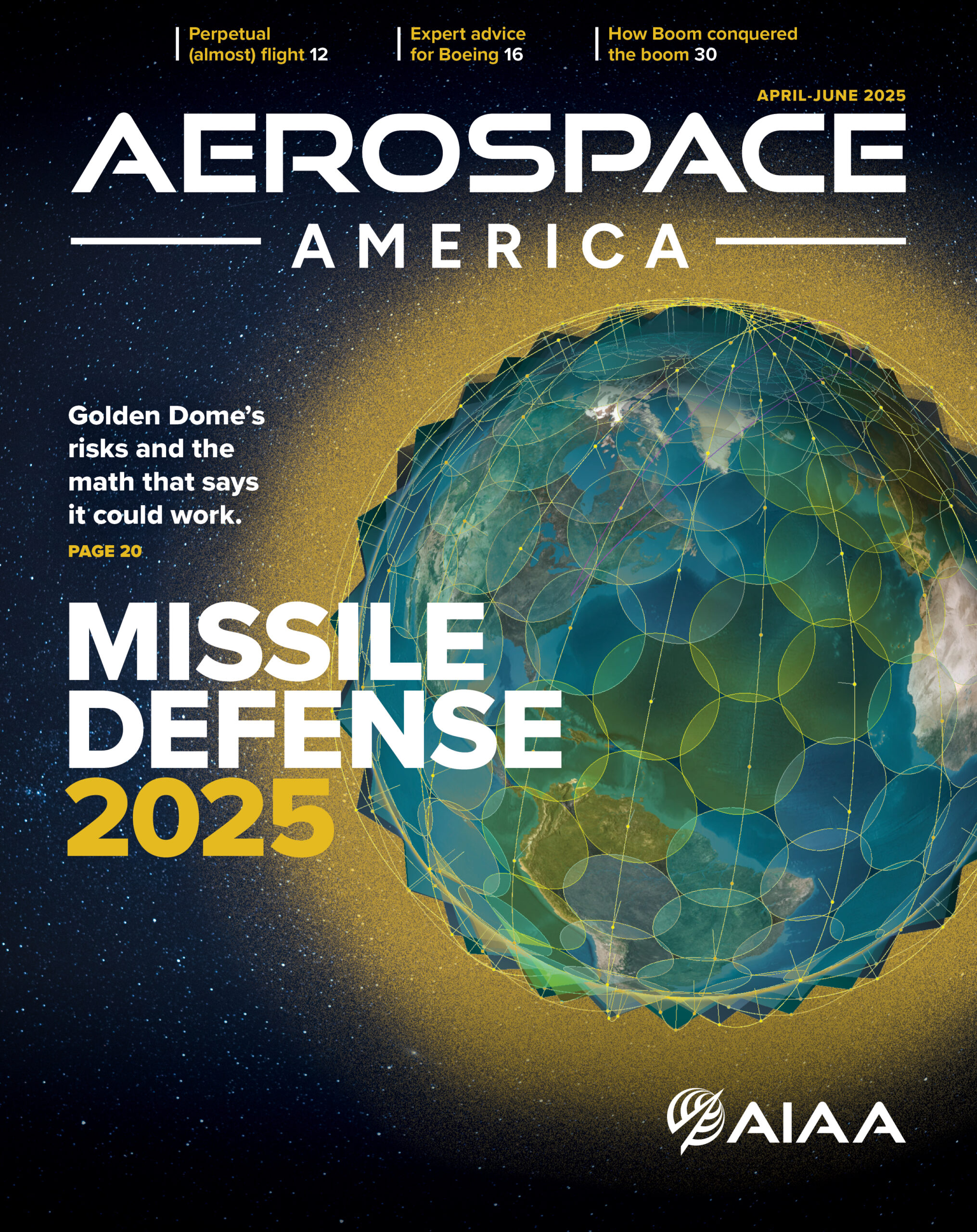
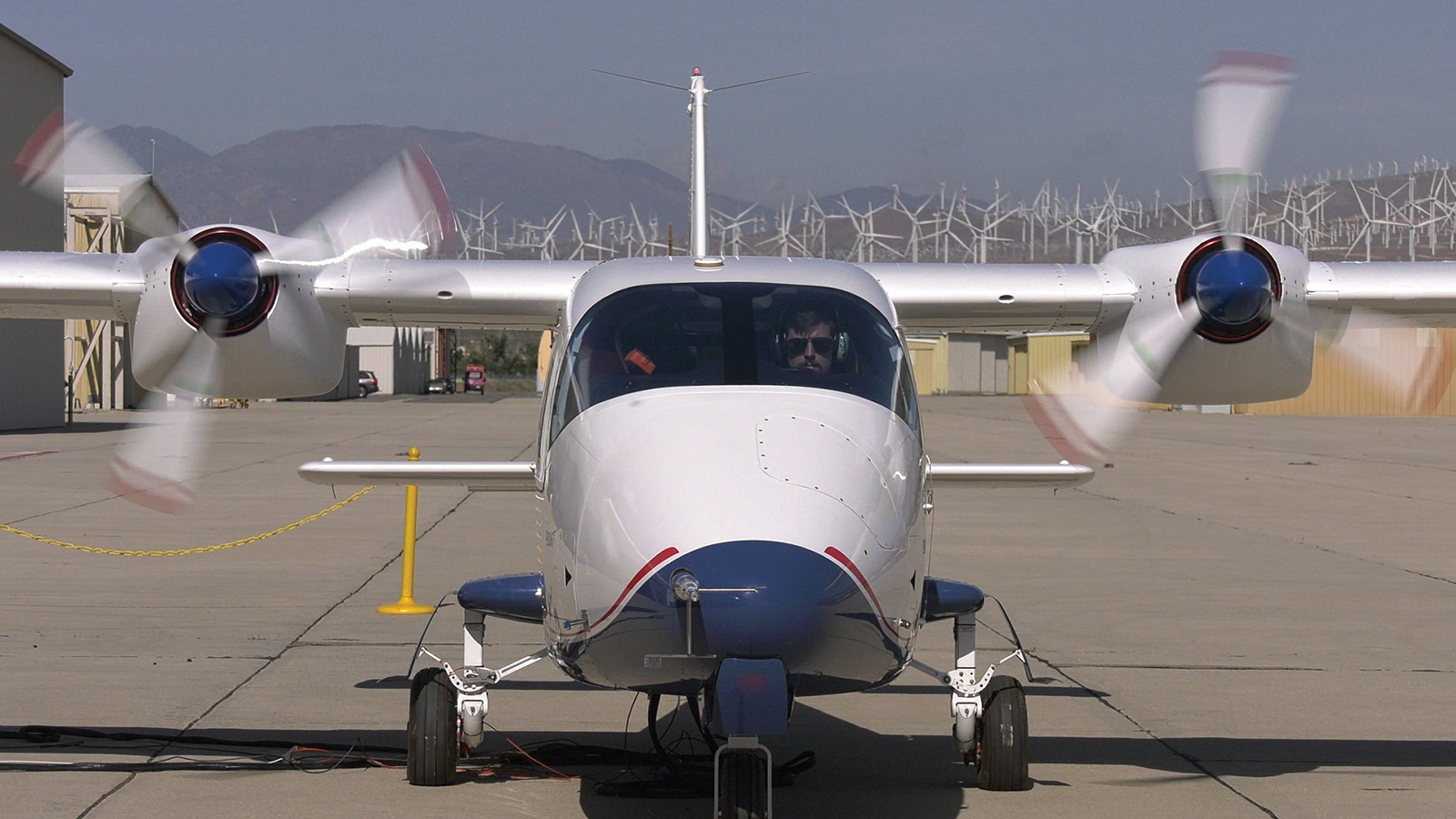