Stay Up to Date
Submit your email address to receive the latest industry and Aerospace America news.
What’s the solution for achieving net-zero air travel by 2050? Hydrogen? Electrification? Rushing sustainable aviation fuel into today’s jets? At least part of the answer could take flight in 2028. Cat Hofacker looks at the history and promise of Boeing’s Transonic Truss-Braced Wing demonstrator.
When aviation consultant Rubén Del Rosario heard about NASA’s multimillion-dollar award to Boeing to build the Transonic Truss-Braced Wing demonstrator, he likened it to the feeling of sending a child off to college.
It’s an apt reference, given that 17 years ago, while at NASA, Del Rosario oversaw the project under which Boeing drew up an early version of the design, easily recognizable by its elongated, thin wings supported by rigid beams. Boeing has been refining the concept ever since through its own internal funding and a series of NASA study contracts meant to help develop technology for future generations of airliners that would expend less fossil fuel.
“We saw the baby be born, and we have been through elementary school doing the fundamental wind tunnel tests,” says Del Rosario, now a vice president at Crown Consulting in Virginia. “So all that testing has been going on to the point that now they feel comfortable that the next step is designing that wing into an airplane to flight test it.”
Indeed, NASA is betting that those years of preliminary design and analysis have positioned Boeing to finalize the design and assemble the demonstrator in time for a one-year flight test campaign targeted to begin in 2028. Under the terms of the Space Act Agreement under which the Sustainable Flight Demonstrator award was made, Boeing and its yet-to-be-announced industry partners must supplement NASA’s $425 million with $725 million of their own funds.
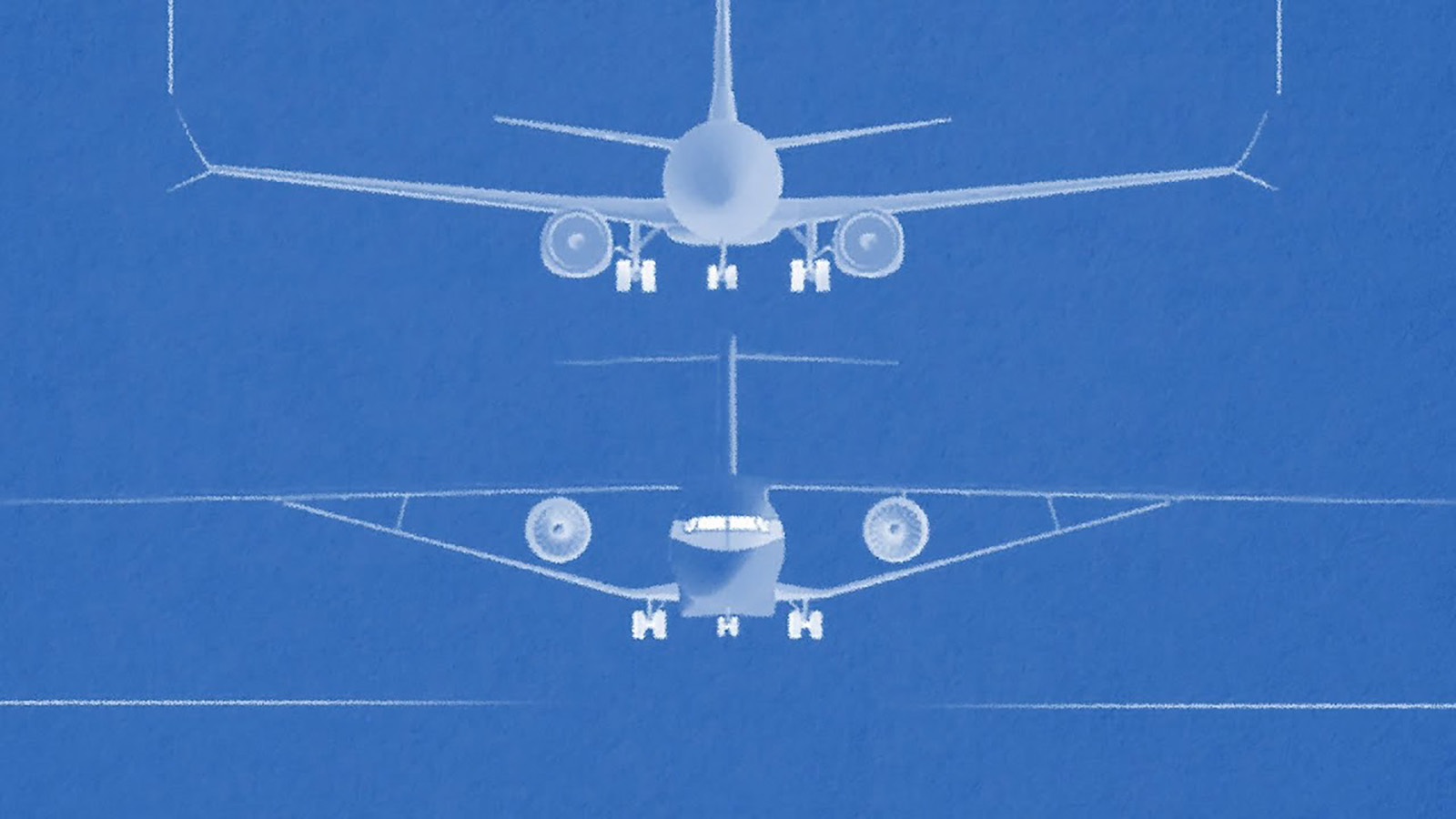
If it seems like an ambitious target, that’s because time is of the essence. NASA wants to demonstrate a 30% fuel burn reduction with the TTBW demonstrator compared to today’s airliners, therefore giving Boeing and other manufacturers the confidence to include a commercial version in their next generation of single-aisle jets.
“This is a way of influencing” the industry’s goal of achieving net-zero carbon emissions by 2050, “especially when coupled with things like sustainable aviation fuels,” says Eric Kaduce, Boeing’s program director for the demonstrator. “Hydrogen has real advantages, but by 2050, its ability to make a marked impact to the global emissions is relatively small just because of the lead times involved — and not just the vehicle, but the global infrastructure required to support that.”
But with these next-generation aircraft scheduled to begin passenger service in the 2030s, “that means we’ve got to get all this done in this decade,” says Brent Cobleigh, manager of NASA’s Sustainable Flight Demonstrator project. “Otherwise, we might have to wait 10 or 15 years,” when the next iteration of airliners is being designed.
A big idea
Concepts for TTBW airliners date back to the 1950s, when Swiss aerodynamicist Werner Pfenninger proposed an ultralong, thin wing braced by rigid support beams to maximize aerodynamic lift. In the following decades, researchers from NASA, the aviation industry and universities have studied the concept. Boeing’s version originated in 2006, when technical fellow Marty Bradley was searching for a topic that the company’s Advanced Concepts group could begin researching that would represent a significant advancement for the aviation industry.
“I came across the impact of aviation on climate, and I ended up finding two people at Boeing that were doing biofuel work,” he says, referring to fuels made from nonpetroleum sources that are now commonly referred to as sustainable aviation fuels. “That got me thinking, ‘What else can we do for sustainability?’”
So he gathered a group of engineers from Boeing’s Research and Technology division in a conference room at the company’s office in Huntington Beach, California, and “we came up with a bunch of things that we might pursue.” The list included aircraft concepts that made use of innovative propulsion methods, including hybrid-electric.
When NASA Aeronautics issued a call for Subsonic Fixed Wing proposals in 2008, the group submitted their ideas under the name SUGAR, short for Subsonic Ultra Green Aircraft Research. The challenge then was similar to the one issued under today’s Sustainable Flight Demonstrator program: Give us your ideas for next-generation aircraft that will burn less fossil fuel. After being awarded a $1.9 million study contract, Boeing proposed five preliminary aircraft concepts and recommended two for further study — the hybrid-electric SUGAR Volt and the SUGAR High, a 124-seat airliner with thin wings slightly longer than Italy’s Leaning Tower of Pisa is tall, supported by a single strut on either side.
That long aircraft caught everyone’s attention. “It looked promising,” recalls NASA’s Rich Wahls, who at the time was chief scientist of the Subsonic Fixed Wing Project, and is now mission integration manager overseeing a portfolio of programs that includes the Sustainable Flight Demonstrator. So NASA awarded Boeing a Phase II contract to refine the SUGAR High concept and “identify the key challenges,” he says.
And there were plenty, because for every advantage associated with the design, there was also a big question: The thin, elongated wings reduce drag by reducing the degree of pressure that would otherwise build up at the wingtips as air travels under and across the wings. But if something weren’t done, this design element would also cause the wings to flutter and vibrate when the airliner travels at transonic cruising speeds, meaning close to the speed of sound. The struts or trusses (Boeing uses the terms interchangeably) bolted to both sides of the fuselage and underneath the wings would prevent the fluttering, but designers also had to consider the drag that would be added by interrupting the smooth flow of air underneath the wings. And although the thinner wings free up additional space for large, fuel-efficient engines, if the engines are too heavy, they will negate the weight savings of the wings.
“Everything ends up being tradeoffs,” says Bradley, who is now an aviation consultant.
Test and test again
Digital modeling and computational fluid dynamics simulations of the SUGAR High concept only provided so much information about these challenges, so in 2012 Boeing engineers built a 15% model out of fiberglass and took it to the Transonic Dynamics Wind Tunnel at NASA’s Langley Research Center in Virginia. They began by flying the instrumented model sans supporting struts to get baseline data on the aeroelasticity, or flutter, of the wings.
“As [the tunnel] built up speed, the wings just started vibrating like crazy,” recalls Boeing’s Kaduce. “So they said, ‘Turn it off, you’re going to snap it!’”
Then, the engineers bolted on the struts and ran the test again: “It was just rock solid.” And subsequent tests showed “even better” results, Kaduce says, due to the addition of jury struts, smaller supporting beams positioned vertically between the underside of the wing and the outer half of the main struts.
Tests at Langley and other wind tunnels at NASA’s Ames Research Center in California continued through 2016, at which point Boeing began making some seemingly small but significant changes to the aircraft. The largest one was increasing the design’s cruising speed.
In early tests, the aircraft flew at Mach 0.745, slightly slower than commercial airliners, the thinking being that a higher cruising speed would increase drag on the aircraft and require it to expend more fuel. But Boeing engineers thought they had a solution: By angling the wings back farther, a total of 20 degrees, designers were able to slow the rate at which air flowed over the wings while the aircraft was traveling close to the speed of sound, therefore preventing the formation of shockwaves that would increase drag.
This in turn required tweaking the trusses because “there was some concern of getting shocks setting up in that corner flow region, right between the top of the outboard portion of the strut and the bottom of the wing,” says Greg Gatlin, the aerospace engineer at Langley who oversaw the wind tunnel tests.
So the trusses were made thinner at the top where they connected with the wings, and thicker at the bottom where they met the fuselage.
“That turned out to be a nice benefit where the strut was having less influence on the wing aerodynamics,” says Gatlin.
Boeing unveiled the updated Mach 0.8 design in 2019 and has been conducting additional wind tunnel tests ever since.
Early research
In 2008, Boeing answered a NASA call for proposals about techniques for reducing fuel burn on future generations of aircraft. That preliminary research, dubbed SUGAR for Subsonic Ultra Green Aircraft Research, yielded the early design for the Transonic Truss-Braced Wing demonstrator that the company will build under NASA’s Sustainable Flight Demonstrator program.
Phase I: 2008-2010
Under NASA’s Subsonic Fixed Wing Project, five preliminary aircraft concepts were evaluated, including one for a strut-braced wing design dubbed SUGAR High, and a hybrid-electric version called SUGAR Volt.
Phase II: 2012-2014
Different fuels and engine configurations were evaluated for the aircraft proposed in Phase I, and Boeing recommended initial planning for a truss-braced wing demonstrator. Subscale models were flown in the Transonic Dynamics Tunnel at NASA’s Langley Research Center to investigate wing flutter.
Phase III: 2014-2016
An initial high-speed design for a Mach 0.7 truss-braced wing airliner was completed. The first transonic wind tunnel test was conducted to study aerodynamic performance in the 11-foot Transonic Wind Tunnel at NASA’s Ames Research Center.
Phase IV: 2016-2020
The design was updated for a Mach 0.8 cruising speed based on results of wind tunnel tests. The first high-lift wind tunnel tests were conducted in the 14’x22’ Subsonic Wind Tunnel at NASA’s Langley Research Center.
Phase V: 2020-2022
Low-speed wind tunnel tests with subscale models and a high-speed transonic wind tunnel to measure buffeting were conducted.
Getting to first flight
With this preliminary design in hand, the NASA and Boeing Sustainable Flight Demonstrator teams have now begun a series of activities to prepare for the first flight, targeted for 2028. The first milestone comes in July, when a conceptual design review is due to take place.
“That will basically lay down the baseline configuration and everything that’s going to be in it,” says Cobleigh, the NASA project manager, “including how we’re going to instrument it to collect the data we need to validate the technology.”
After a critical design review, currently scheduled for early 2026, construction of the demonstrator will begin. Boeing plans to modify a retired MD-90 aircraft, one of two that are in storage at Southern California Logistics Airport, also known as Victorville.
“We’re not really building an airplane. We’re building a research tool,” Kaduce says. “So starting from something like an MD-90 makes a lot of sense.”
Necessary modifications include ripping off the aircraft wings, removing the engines and then shortening the fuselage before installing the new 52-meter wings and trusses, both of which will be constructed from carbon fiber. Among the new components to be installed will be a pair of turbofan engines, from a company yet to be announced.
If all goes as planned, the aircraft will take off from Edwards Air Force Base in California in 2028, likely with a Boeing pilot and a NASA pilot aboard, heavily instrumented to measure “the fuel flow, the drag, trying to calculate the drag of the airplane and all of that to validate the overall performance,” Cobleigh says.
As for the true measure of success, he says that will be calculated by the impact beyond a new Boeing commercial aircraft: “If we come up with a 30% more efficient airplane, the rest of the market has to match that. So in some sense, we could be a catalyst for making sure that the entire fleet across the world becomes more efficient over time. And that’s what we need to do,” says Cobleigh.
Adds Bradley, “It’s a matter of execution now.” NASA and Boeing have “everything in place to do it. They have the technical data they need to do it. Now it becomes [a question of] how well can the program be executed.”

About cat hofacker
Cat helps guide our coverage and keeps production of the print magazine on schedule. She became associate editor in 2021 after two years as our staff reporter. Cat joined us in 2019 after covering the 2018 congressional midterm elections as an intern for USA Today.
Related Posts
Stay Up to Date
Submit your email address to receive the latest industry and Aerospace America news.
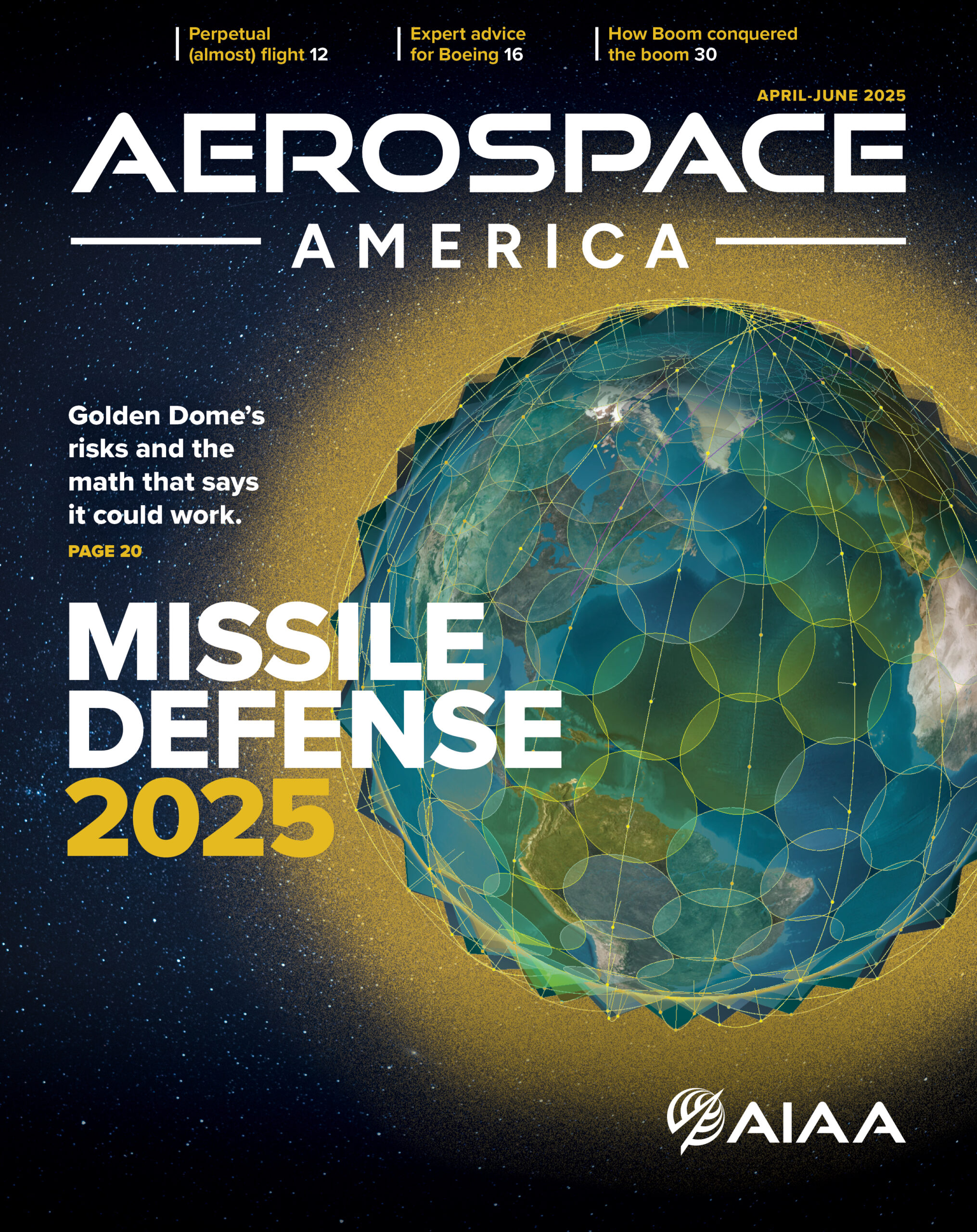