Stay Up to Date
Submit your email address to receive the latest industry and Aerospace America news.
Carbon composites have a tendency to weaken and delaminate when subjected to repeated cycles of heating and cooling as is common in aerospace applications.
N12 Technologies Inc., a 35-person company formed in 2012 as a spinoff of an MIT project, this year hopes to enter high-volume production with a material called Nano-
Stitch, which would be added during the composite fabrication process to combat delamination.
Today, engineers must either add more carbon fiber layers to compensate for the delamination risk, which adds undesired weight, or find a structural workaround.
“NanoStitch specifically addresses and eliminates the delamination failure mode,” says materials scientist Ryan Williams, director of science and technology for the company and its first employee. It can achieve the same strength with less material or higher strength with the same amount of material, he says. N12 bills the material as especially suitable for today’s consumer electric-VTOL (vertical takeoff and landing) concepts, where weight is a performance hurdle.
Mass production of NanoStitch has been a challenge, but N12 thinks it has solved that. Technicians at the company’s Somerville, Massachusetts, factory place a sheet of proprietary metal substrate into a large furnace called a reactor. The gray material in the scanning electron microscope image (top of page) is the substrate. Gases are introduced, and trillions of cylindrical, carbon nanotube molecules (the grass looking material) form vertically via this chemical-vapor-deposition process. So far, N12 has scaled up the width of the sheets to 300 millimeters and Williams says one machine has the potential to produce 1,500 mm wide sheets.
From there, an additional roller would be added to the composite production sequence and a NanoStitch sheet would be applied onto a standard sheet of carbon composite pre-impregnated with epoxy. “We just sort of sneak in at the end,” Williams says. Rolls of this composite/NanoStitch material would be shipped to component fabricators who would follow their standard process of cutting composite sheets and stacking them to form a composite structure. Heat and pressure would then be applied to harden the polymer into the final part.
How do the nanotubes add strength? As shown in the other image (second image), the tubes are sandwiched vertically between layers of carbon fibers running in two directions.
“Now you really have a material that’s reinforced in three directions,” Williams says. The whitish material is the epoxy that binds everything together.

About Ben Iannotta
As editor-in-chief from 2013 to March 2025, Ben kept the magazine and its news coverage on the cutting edge of journalism. He began working for the magazine in the 1990s as a freelance contributor. He was editor of C4ISR Journal and has written for Air & Space Smithsonian, New Scientist, Popular Mechanics, Reuters and Space News.
Related Posts
Stay Up to Date
Submit your email address to receive the latest industry and Aerospace America news.
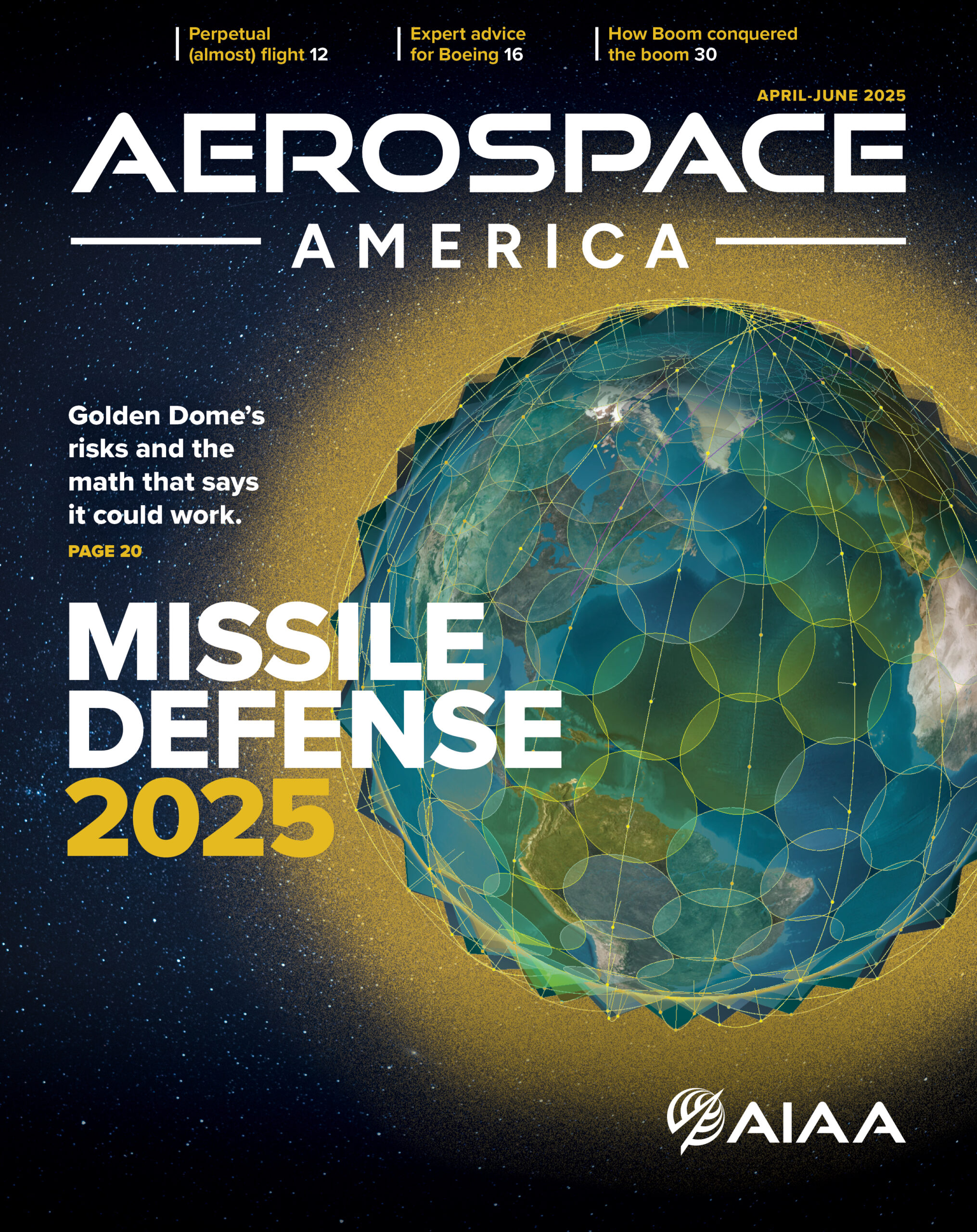
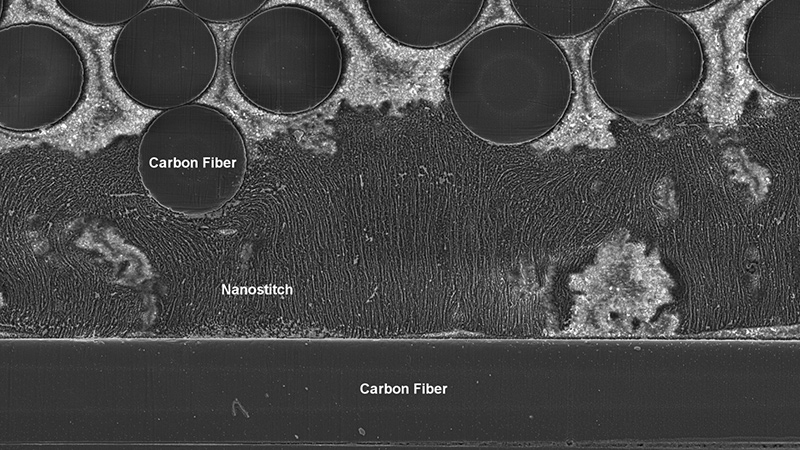