Stay Up to Date
Submit your email address to receive the latest industry and Aerospace America news.
Someday, a dozen palm-sized, origami-inspired robots called PUFFERs, short for Pop-Up Flat Folding Explorer Rovers, could be released from a single, shoebox-size instrument box on a larger planetary rover. Once free from their parent, the PUFFERs would roll in and out of Martian craters or perhaps across Jupiter’s icy moon Europa.
It sounds futuristic, but Jaakko Karras, the PUFFER project manager in the Robotics Group of the NASA-funded Jet Propulsion Lab, says he’s optimistic that within five years PUFFERs will be chosen for a future Mars mission.
Getting to that level of confidence did not come easily. JPL engineers were testing prototypes in 2015 when they hit a snag. Each rover needed fine wires of copper, called traces (the shiny patch in the center of the pictured rover), to carry sensory data and power through the rover. Designers had embedded the traces in polyimide, a strong polymer that covered the flexible circuit boards which formed the rover’s chassis and doubled as its brain. The tests revealed that the copper traces had a habit of cracking when folded and unfolded repeatedly, for instance where the wheels meet the chassis. That was a big problem, because each rover needed to slant its wheels inward to squeeze under obstacles or climb up slippery terrain.
“We had two conflicting challenges, we needed the copper traces to survive enough cycles to be useful and we wanted to keep our hinges fairly thin and narrow like a crease on a sheet of paper,” says Karras.
That’s when Dale McKeeby, vice president for Pioneer Circuits, a Santa Ana, California, manufacturer of printed circuit boards for aviation and space, met the PUFFER engineering team. He offered to print alternative circuit board mock-ups for PUFFER free, a service Pioneer has performed for JPL missions for decades.
The engineers realized that instead of creating hinges with bendable circuit boards, they could lay stacks of circuit boards end to end and join them with Dupont’s Nomex fabric (the beige burlap-looking material in the image at top). This heat-resistant material is found in space suits and airbags for landing on Mars. This time, the woven material would form the hinges. Next, they embedded the copper traces in narrow polyimide ribbons spanning each hinge like a bridge. This resulted in gentler bending of the copper traces.
Testing shows that these bridges can stand repeated folding and unfolding under mission scenarios, Karras says.
Karras envisions dropping PUFFERs from helicopters onto polar ice sheets on Earth or catapulting them away from rovers on Mars. JPL engineers are writing software to make PUFFERs semiautonomous so they can perform jobs like entering a cave, capturing images and relaying data through a daisy-chain of other PUFFERs to the parent rover.

About Debra Werner
A longtime contributor to Aerospace America, Debra is also a correspondent for Space News on the West Coast of the United States.
Related Posts
Stay Up to Date
Submit your email address to receive the latest industry and Aerospace America news.
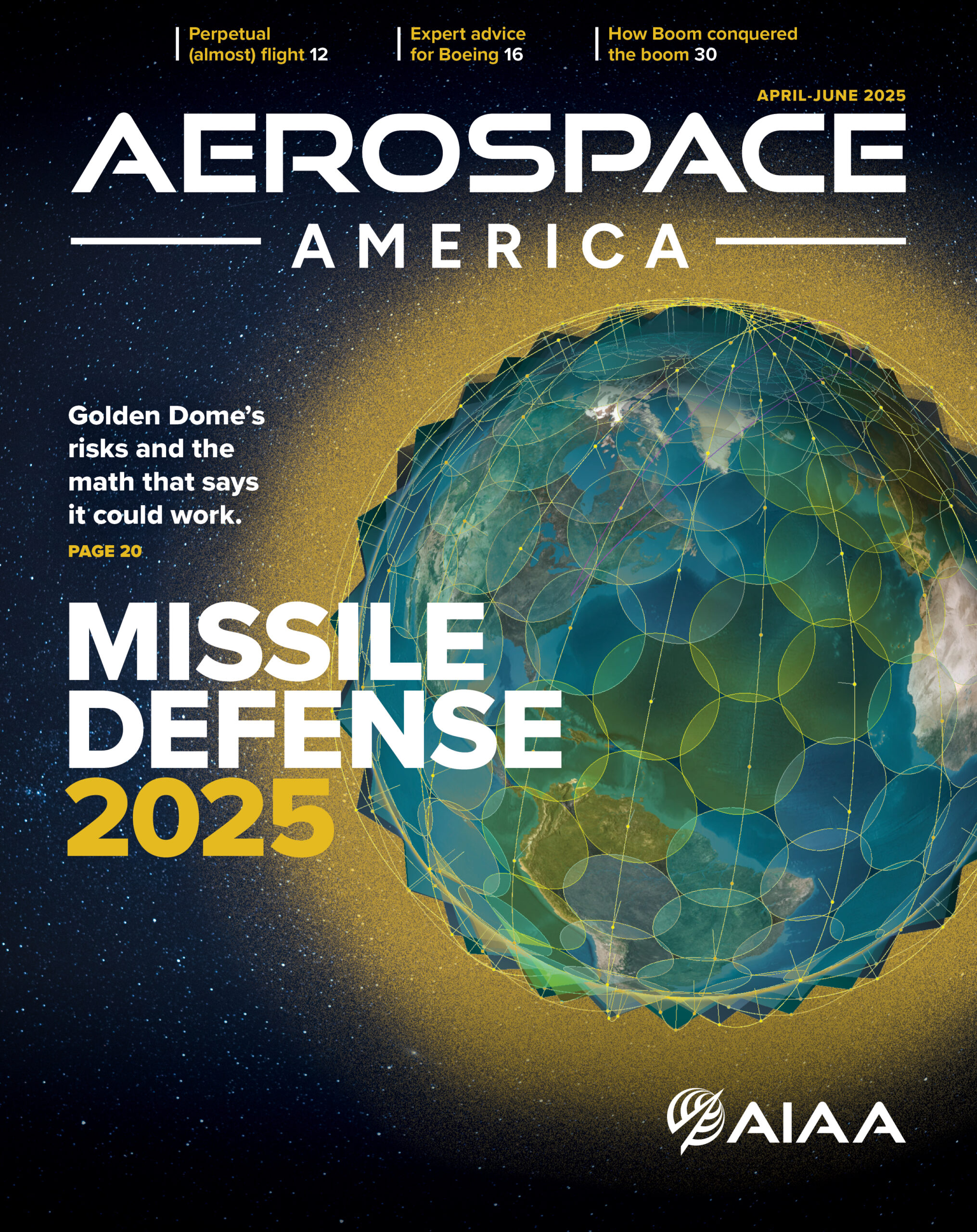