Stay Up to Date
Submit your email address to receive the latest industry and Aerospace America news.
Creating a piloted glider that can soar into the stratosphere on waves of air rising over the Andes required some creative safety innovations. Keith Button tells the story of Perlan 2.
Flights of the Perlan 2 glider in August and September were not for naught, even though pilots failed to beat the glider altitude record they set last year when Perlan 2 climbed to 76,124 feet over Argentina.
Design improvements over the original Perlan aircraft worked as planned, and the Nevada-based Perlan Project, which is funded mainly by Airbus, will try again next year to reach its ultimate goal of 90,000 feet, the pilots and engineers say.
The conclusion of this year’s flights marked the first time in Perlan 2’s four-year history that the team hasn’t returned from Argentina with a long to-do list, says Morgan Sandercock, chief engineer for the project. “We don’t have a big sheet of paper filled with: ‘Fix this; repair that; upgrade that.’ We’ve got it flying pretty much perfectly how we want it to fly now,” he says.
Getting to this point required overcoming some life-and-death engineering challenges.
Bad vibrations
The team conducts its flights in late winter in the Southern Hemisphere to take advantage of Antarctica’s powerful polar vortex, which pushes wind over the Andes. When some of these winds rush down the backsides of the mountains, they rebound forcefully and, under the right conditions, can rise as high as 130,000 feet and persist for days. These stratospheric waves are what the Perlan 2 pilots ride into the stratosphere once they are released by their tow plane at an altitude of about 45,000 feet.
Steering a carbon-fiber glider with a 26-meter wingspan through the stratosphere at the climb rate of an airliner can be hairy. The two pilots in their pressured cockpit and heated flight suits must avoid severe wing flutter, which are vibrations that can be catastrophic.
“We know that flutter will get worse as we climb higher,” says Sandercock, one of the co-pilots who rotates on the Perlan 2 flights.
The thinning atmosphere provides less of a damping effect to smooth vibrations that can become flutter. Also, the risk of flutter increases with rising airspeed, and the glider must accelerate as altitude increases to maintain lift in the thinning air. As Sandercock notes, every aircraft has a red line on its airspeed indicator, “and if you exceed that red line, then bad things happen, like the wings fall off.”
Obviously the team can’t let that happen.
Below the stratosphere, staying under the indicated airspeed limit is part of the strategy for avoiding flutter. But in the stratosphere, the indicated airspeed doesn’t tell the whole story. That’s because pitot-tube sensors measure airspeed by sensing the pressure of air flowing by. Since the air in the stratosphere is thinner, this means the indicated airspeed from the pitot sensor remains at a constant figure while the glider’s true airspeed in fact increases to maintain lift at higher and higher altitudes. If the glider were to reach a recording-setting 90,000 feet, for example, its true airspeed might have to soar to 370 kph for adequate lift, Sandercock says.
They needed to be confident that Perlan 2 would not succumb to flutter in those conditions.
The team members realized after ground vibration tests on Perlan 2 in 2015 that they would need to test for vulnerability to dangerous flutter in real time during each flight. The tests showed that unsafe flutter conditions could result if the plane flew too fast, outside its flight envelope, and a confluence of conditions occurred. Those conditions could include certain bolts loosening plus mechanical connections coming apart plus damage to the glider’s skin. The extreme cold at high altitudes could also create flutter from unexpected sources — cold grease in a hinge creating more friction, for example.
So Sandercock built a flutter test system that fits in the wingtips. It consists of motors that vibrate six weights of about 170 grams each (that’s about the weight of a cellphone) to see if vibrations of certain frequencies begin to produce signs of flutter. Also, four accelerometers measure vibration, twisting and bending in the wing. Perlan 2’s pilots activate the flutter test system during every flight. Measurements of the frequency responses and damping are routed to the team’s flight test engineers at El Calafate airport, Perlan 2’s Argentina base. When the glider climbs to an altitude where it has never before flown, the measurements are also routed to engineers with ATA Engineering in San Diego who confirm that flutter conditions are not present before giving the go-ahead for the glider pilots to continue climbing.
The pilots do this about every 5,000 feet during a record attempt.
The Perlan 2 team also tests for Dutch roll, which is an oscillating rolling and yawing movement that could create unnecessary drag and slow the glider’s climb. These tests also are done every 5,000 feet as an untested altitude is reached. The team initially believed it might have to install an active damping device to control Dutch roll, but the pilots so far have determined they can control the condition without damping.
The team hoped to soar as high as 90,000 feet during the 2019 flights. But this year, a sudden stratospheric warming event, or SSW, disrupted the polar vortex by mixing in warm air and diminishing the vortex wind speeds. The last strong SSW in the Southern Hemisphere occurred in 2002, and this year’s was the strongest ever, according to the project team. During this year’s highest flight, to 65,000 feet, the stratospheric wave generated lift of 30 to 60 meters per minute, compared to 240 to 300 meters per minute during last year’s record flight, says Jim Payne, chief pilot for the Perlan 2.
If all goes well, they’ll try again next year. Sandercock says there is a practical limit to how high Perlan 2 or any glider can fly. Cracking 100,000 feet would require flying at Mach 0.7 or Mach 0.8, and “giant amounts of thrust” would be required to push the aircraft through the transonic drag of those speeds, he says. “We don’t believe it will ever be possible for any glider to fly above 100,000 feet.”
Combating cold
Another potential high-altitude danger the team had to prepare for was extreme cold. The temperatures in the atmosphere above 50,000 feet could dip to minus 78 degrees Celsius, threatening to crack materials or cause mechanical parts to jam.
Business jets and commercial airliners cruise in temperatures almost that cold, but designers of these aircraft have an advantage that glider designers don’t have: combustion engines. “They just run a little duct out there and put some hot air in and there you go; you’ve solved the problem,” Sandercock says.
The only possible sources of warming power aboard Perlan 2 are its batteries.
Engineers needed to find out how much warming would be needed, so they tested glider components on the ground by lowering their temperature to minus 68 Celsius with frozen carbon dioxide, better known as dry ice. They discovered that the oxygen regulators on each pilot’s breathing apparatus would need to be heated to minus 40 degrees.
They also discovered that the performance of Perlan 2’s lithium batteries dropped off sharply below minus 10 degrees Celsius. They decided to attach heaters to the batteries and divert a few percent of each battery’s energy to them.
Next year
In addition to shooting for altitude records, Perlan 2 collects meteorological data and conducts experiments requested by scientists and students.
The glider flights provide controlled access to specific spots in the stratosphere that isn’t possible with weather balloons and sounding rockets.
The Perlan team has not announced its plans for next season, but Airbus says it will continue to sponsor the program until Perlan 2 reaches 90,000 feet, which would set the altitude record for all winged-aircraft, not just gliders.

About Keith Button
Keith has written for C4ISR Journal and Hedge Fund Alert, where he broke news of the 2007 Bear Stearns hedge fund blowup that kicked off the global credit crisis. He is based in New York.
Related Posts
Stay Up to Date
Submit your email address to receive the latest industry and Aerospace America news.
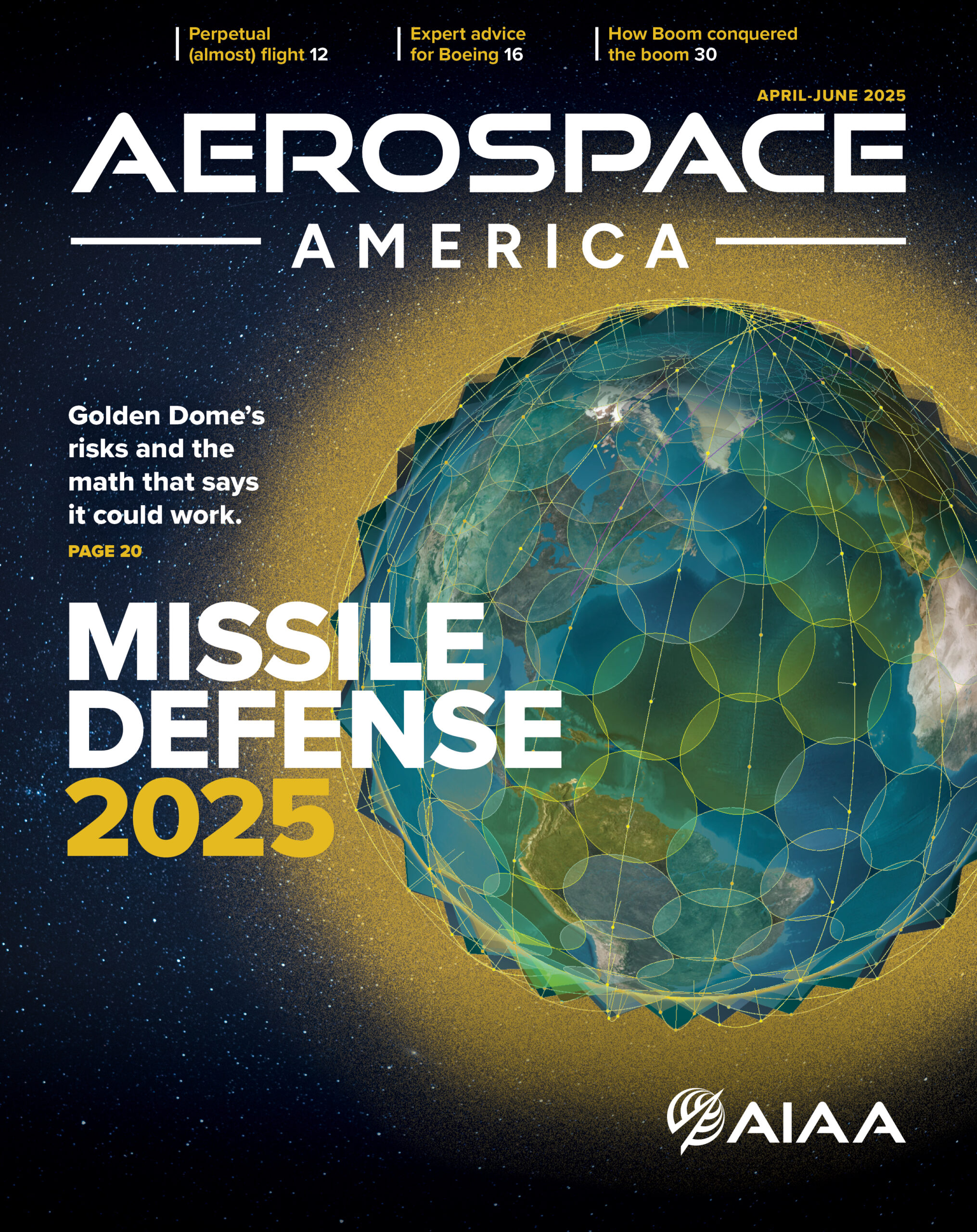
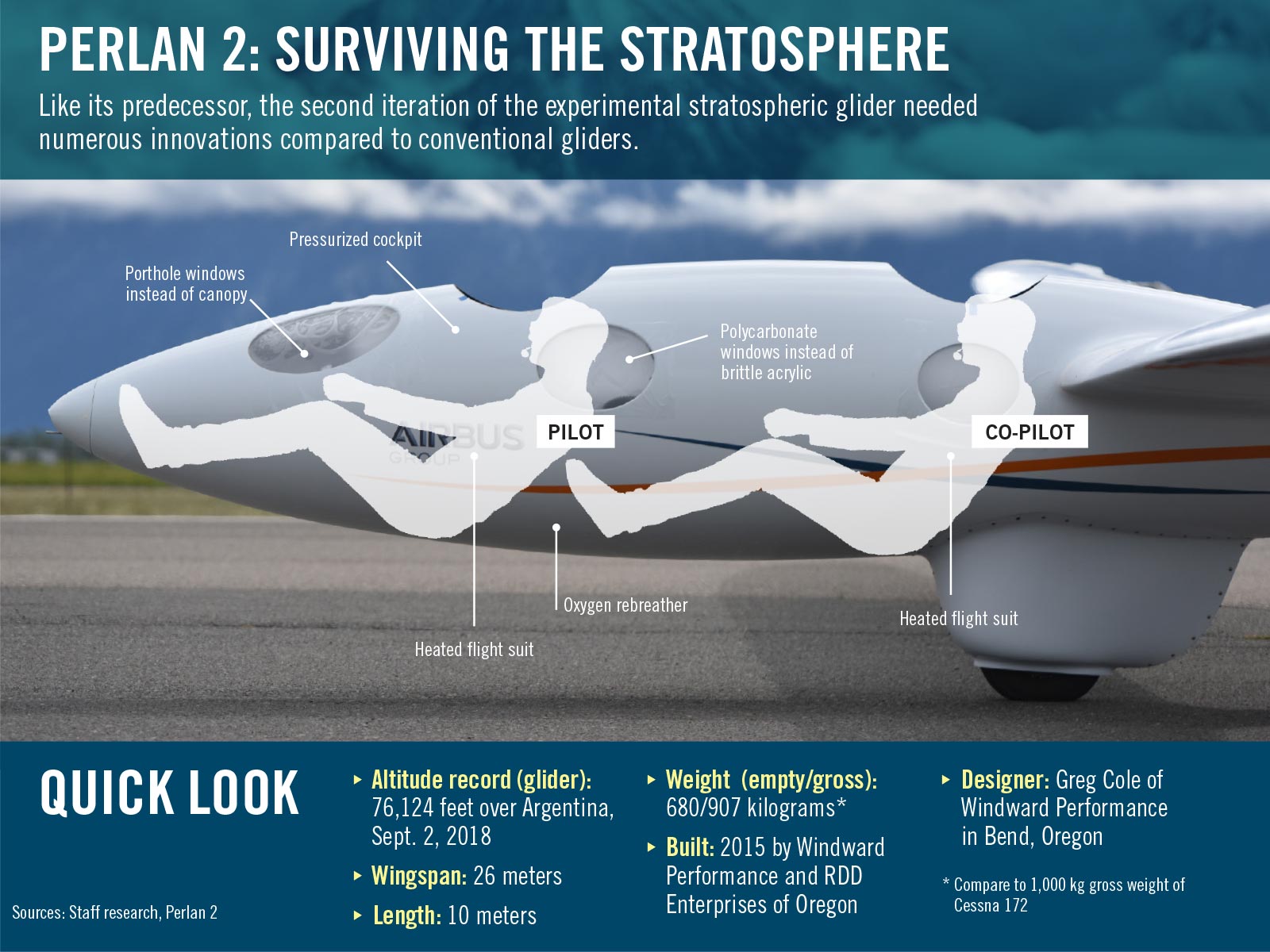
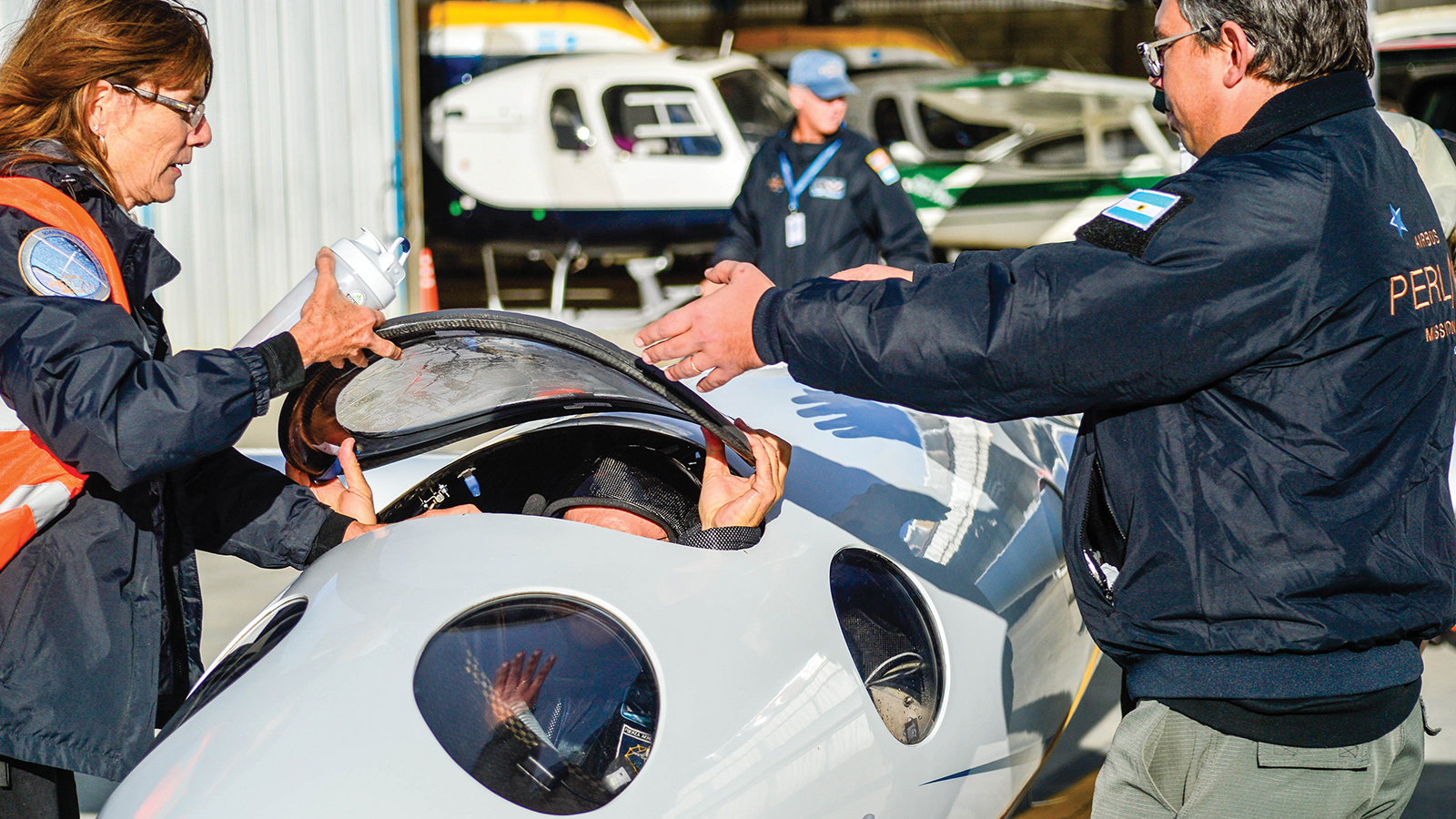