Stay Up to Date
Submit your email address to receive the latest industry and Aerospace America news.
Jerome Bonini
The European Union’s Clean Sky program is funding Paris-based Safran to create an airplane engine that would be lighter than conventional jet engines, burn less fuel and release fewer carbon emissions. Safran’s Jerome Bonini oversees research, testing and development of the Open Rotor concept: an engine without a casing that includes two exposed sets of counter-rotating blades behind the gas turbine. The safety of the design was a top concern for Bonini and his team even before the fatal fan blade accident in April on a Southwest Airlines plane that involved an engine built by CFM International, the joint venture of Safran Aircraft Engines and GE Aviation. Bonini thinks the Open Rotor’s composite fan blades, which are like those on today’s CFM LEAP (Leading Edge Aviation Propulsion) engines, could prove to be more durable than titanium blades like the one that broke in the April accident. I spoke with Bonini on the phone and followed up by email to learn the latest about the Open Rotor project.
IN HIS WORDS
Reducing fuel burn
The open rotor saves 30 percent fuel burn compared to CFM56 turbofan engines. The main objective of Clean Sky programs is to reduce the environmental impact of aviation. During the next four years we will continue to work on Open Rotor with this funding. It is partially funded by the European community. All the Clean Sky projects aim to achieve by 2050 to reduce [European Union carbon dioxide emissions] by 75 percent compared to the beginning of this century.
Post-test inspection
The engine was very good on the test bed [in 2017]. We will disassemble each part to check that the behavior of each part is what we expect. If there is some start of degradation, we will correct for the next version.
Bird strike test
We have composite blades — the way the propeller blade cracks is different from a metallic blade. These blades are more robust than metallic blades. We can imagine a different way to monitor them and to replace blades before failure. The main event we have to demonstrate is the bird strike event. We intend to perform it in the next two years in Villaroche where we have a dedicated test bed for ingestion test of fine blades.
Timetable
Regarding the flight test, that should be 2024-2025. We expect the beginning of the development in 2030 and an entry into service in 2035.
Possible interest from airlines
It will depend on what the market will need in 15 years and on the airframer decision to change or not the architecture of the future aircraft. You have to do a breakthrough; 10 to 15 years is not too much time to convince them that the Open Rotor is the right option. We have new technologies which can help them to reduce fuel burn for the next short- and medium-range aircraft. And if they want to have the same gain in terms of fuel burn they made with the last generation, they have to think differently.
More thrust, less drag without engine casing weight
If the diameter of the fan is very large, you can reduce significantly the fuel consumption of the engine. Bypass ratio is a major lever to increase the engine’s efficiency. With the open rotor concept, you can increase the diameter of the fan and bypass ratio without penalties of drag and weight of casings.
Lighter than titanium
The 3D woven innovation enables us to make stronger and lighter parts and plays a key role in improving the performance of the new LEAP commercial airplane engine. We make the fan blades and case for the LEAP engine family using a 3D-woven composite and the resin transfer molding, RTM, process. Composite materials are a sea change in the aerospace industry. Their combination of strength and lightness makes a significant contribution to improving engine efficiency. These 3D-woven RTM composite blades are a 500-kilograms-per-airplane weight savings over conventional blades. The next step will be to expand use of these materials to aircraft engine parts subject to greater stress, such as compressors.
Explaining counter-rotation
[The blades] are counter-rotating to reduce the speed of each set of blades. By having two rotating stages, you can put a static one to redirect the air after rotation. They make sure the air flow is going straight.
Aerodynamic shapes for wings, fuselage to match open rotor engine
These engines can be adapted to be installed under the wings, but it would be best to have them farther back on the aircraft. We have to work very close with a framer to have the best integration. If you increase the size of the aircraft a lot and keep the engines under the wings, you have a problem with your landing systems. You have the problem of weight also, of the aircraft itself, and if you want to reduce this impact, you have to think about the integration of large bypass ratio engines differently. Airbus has also one of these concepts where the engine is embedded at the rear of the fuselage. You have also a NASA boundary layer ingestion concept.
Public perception
This concept is different. You have to make people confident in this concept and that’s the reason why we talk a lot about this concept today. Even with 10, 15 years, it’s a good challenge for us to prepare people to have an engine with no casing at the rear of the aircraft and a large engine. The aircraft would be larger, so the engine is larger. That’s not so different.
About Tom Risen
As our staff reporter from 2017-2018, Tom covered breaking news and wrote features. He has reported for U.S. News & World Report, Slate and Atlantic Media.
Related Posts
Stay Up to Date
Submit your email address to receive the latest industry and Aerospace America news.
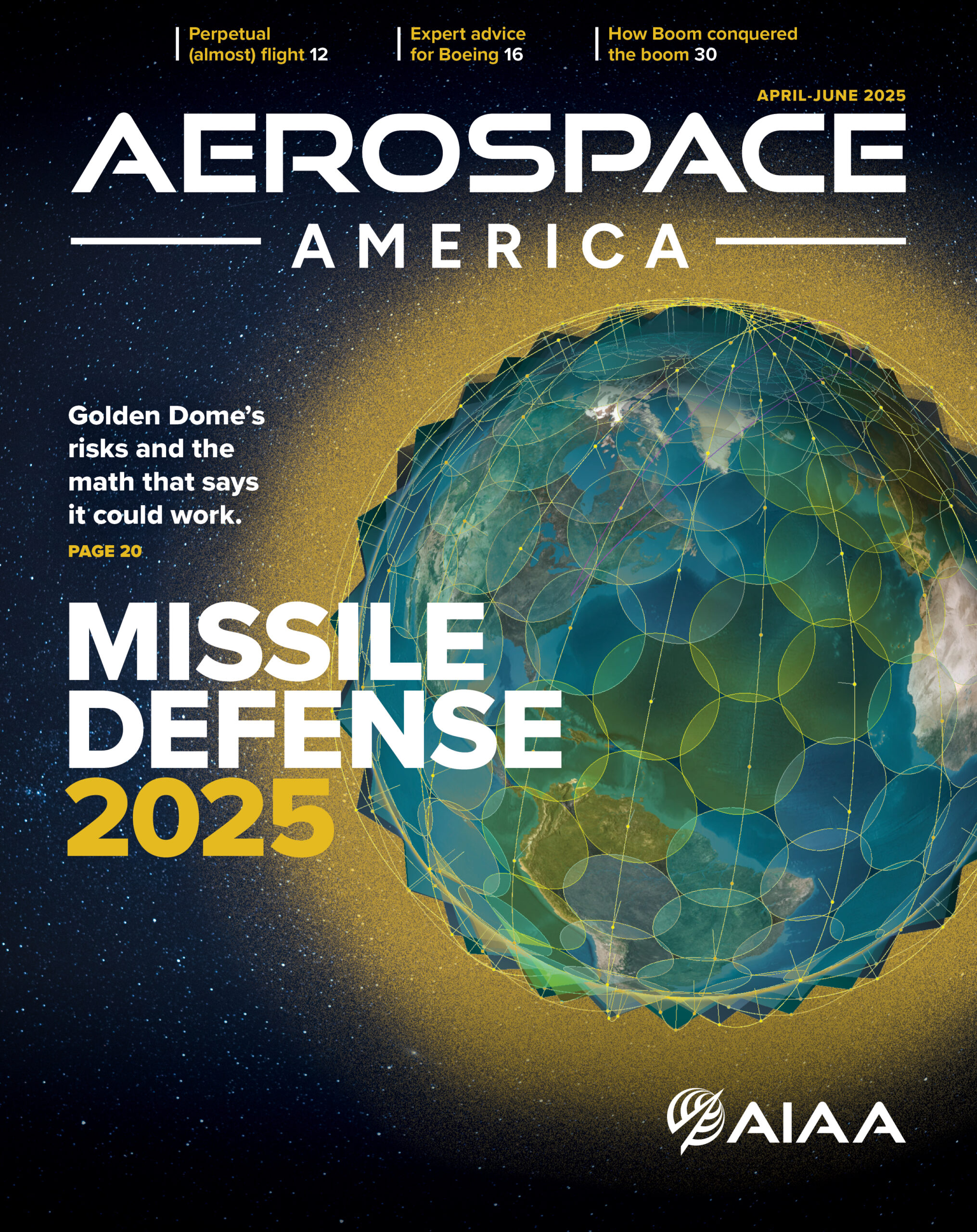