Stay Up to Date
Submit your email address to receive the latest industry and Aerospace America news.
Designing a jet-fast plane that can stop on a dime in midair, hover and speed off
Eight times over the last year, a bizarre-looking aircraft with tilted wings, tilted canards and 24 ducted fans has lifted off the tarmac of a naval facility in Maryland. The unmanned plane weighs just 147 kilograms, but it’s designed to prove the feasibility of building an unmanned plane that would be substantially larger and do something no plane of that size has ever done: Hover like a helicopter and fly nearly as fast as a business jet. The closest thing to this planned aircraft, called LightningStrike, would be the U.S. V-22 Osprey tiltrotor, but that aircraft’s speed tops out at about half that of a Gulfstream G650 business jet.
“This is the most difficult airplane I have worked on in my long professional life,” says systems engineer Carl Schaefer, the LightningStrike program manager at Aurora Flight Sciences, the Manassas, Virginia, aviation and aeronautics research company that specializes in unmanned vehicles. “Nothing like it has ever flown. This is truly a DARPA-hard problem.”
DARPA awarded Aurora an $89.4 million contract in March 2016 to build a full-scale version of LightningStrike as a demonstrator. The plane has to carry a useful load equal to at least 40 percent of its gross weight, achieve sustained air speeds of 300 to 400 knots, hover with an efficiency of at least 75 percent, which is measured by dividing the aircraft’s weight by the amount of power it needs to remain aloft, and demonstrate a lift-to-drag ratio of at least 10, compared with about 18 for a 747.
Schaefer and his team are flying the subscale model, which runs on lithium polymer batteries, to test the design’s aerodynamics and fine-tune its avionics and flight control algorithms. The team faces some daunting challenges for the combustion-powered full-scale demonstrator that they plan to start building shortly. The plane must be aerodynamically suited and lightweight enough for its complex role, while packing enough power for vertical liftoff and hover.
The LightningStrike team, which includes Rolls-Royce LibertyWorks and Honeywell International, will build the carbon fiber epoxy composite demonstrator around a single Rolls-Royce AE 1107C turboshaft engine housed in the fuselage. The AE 1107C is the same engine as in the V-22 transports built by Bell Helicopter and Boeing Rotorcraft Systems.
Instead of the AE 1107C engine turning a propeller or rotor, on the LightningStrike it drives a gearbox with three Honeywell 1-megawatt generators that distribute electric power to 24 enclosed fans carried in the plane’s tilt-wings and tilt-canards. The three fans in each canard are 27 inches (69 centimeters) and nine fans in each wing measure 31 inches (79 centimeters). Because the fans’ propulsive power helps generate lift, engineers were able to size the plane’s wings and canards for efficient cruising rather than enlarging them to produce the additional aerodynamic lift for takeoff and landing, a move that saves weight and fuel.
“Once you decouple the [combustion-based] power generation from the propulsive force, you can start integrating those fans anywhere you want on the air vehicle,” says Kaare Erickson, chief of advanced propulsion concepts for Rolls-Royce LibertyWorks, the company’s advanced research unit in Indianapolis. The Rolls-Royce engine generates electricity that’s delivered by wires to motors that weigh a fraction of what combustion engines would weigh. “It enables all kinds of interesting concepts not just for vertical takeoff and landing but for conventional flight as well,” Erickson says.
This isn’t the first time engineers have tried separating an aircraft’s power source from its propellers or ducted fans. In the past, however, that approach made aircraft too heavy for vertical takeoff and landing because engineers had to install additional communications, power conversion and control mechanisms to link the power source with the fans or propellers. Aurora and its teammates eliminated all that equipment as well as the thermal management issues associated with each device by developing LightningStrike’s Electric Distributed Propulsion, which relies on three flight control computers to ensure that the appropriate amount of power goes to each of the plane’s ducted fans throughout flight.
The Electric Distributed Propulsion creates challenges of its own, though. Rolls-Royce had to figure out how to power electrical generators with an engine that normally provides shaft horsepower to a rotor that has so much inertia it doesn’t accelerate or decelerate quickly. “That is a real challenge: managing the turbine engine and the power generation and making sure it all stays cool and the engine is operating at peak efficiency,” Erickson says.
Another challenge will be coordinating operation of the 24 fans. Aurora and Rolls-Royce invented hardware and software to monitor the fans’ performance to ensure that they start turning in a synchronous fashion and remain synchronized. “We can lose a fan or two and still land safely if we ingest a bird,” Schaefer says. “But we have to make sure that when a fan drops offline, we don’t lose all the fans.”
Aurora and Rolls-Royce pulled LightningStrike technology from existing programs wherever possible. The demonstrator’s avionics are similar to those of Aurora’s Orion medium-altitude long endurance unmanned airplane, while its ground control station software stems from the company’s Centaur optionally piloted airplane. Aurora engineers also relied on expertise they gained working on a DARPA contract a decade ago to build GoldenEye 80, which looks like a flying ducted fan.
Still, a lot of LightningStrike’s hardware and software is brand new, particularly the equipment that distributes electric power throughout the aircraft. To ensure that all the old and new pieces work together, Schaefer and his team planned an incremental risk-reduction strategy.
Since DARPA hired Aurora to build LightningStrike, the agency has allowed the team to release only one video publicly. That video, taken shortly after the contract was awarded, shows Aurora’s 20 percent scale model of LightningStrike lifting off, hovering and landing. Since then, the company has flown the battery-powered 147-kilogram LightningStrike model seven more times at the U.S. Naval Air Station Patuxent River’s Webster Outlying Field in Maryland.
In addition to building the scale model, Aurora set up extensive ground testing equipment. One apparatus emulates the hardware and software that direct power from the Honeywell generators to each fan. Others emulate LightningStrike’s landing gear, pumps, valves, and wing-tilt and canard-tilt actuators. Engineers rely on still another apparatus to see that the AE 1107C works with Honeywell’s generators and LightningStrike’s Electric Distributed Propulsion. “Once we are satisfied that something works, we pull items out of the test rig and it goes right onto the airplane,” Schaefer says.
Aurora engineers plan to design, assemble and build the full-size LightningStrike over the next 14 months. “We will have to have an aircraft on its gear ready for engine lightoff in the spring of 2018,” Schaefer says. Then, engineers plan to conduct a six- to seven-month series of ground tests at Aurora’s Manassas facility and at the Naval Air Station Patuxent River or at Webster Outlying Field before flying at Patuxent River. The company may conduct additional LightningStrike flights at the U.S. Army’s Yuma Proving Ground in Arizona.
Schaefer says he’s hopeful one of the military services will buy some version of LightningStrike. “We want to refine the airplane a bit more to design it around some operational requirements,” he adds. DARPA often pushes technology forward and then hands it off to the Army, Navy, Air Force or Marine Corps to fulfill a military role.
One unique feature of LightningStrike is its excess power. When hovering, the airplane uses 2.7 to 2.8 of its 3 megawatts of available power. When it’s cruising, LightningStrike draws only about 1 megawatt, which leaves nearly 2 megawatts of excess power that could be used for sensors, jammers, lasers or weapon systems.
Whether or not anyone buys a version of LightningStrike, Schaefer and Erickson are confident the airplane’s aerodynamic principles and propulsion technology will find their way into future military vertical takeoff and landing aircraft or commercial aircraft. “The aircraft was developed purely as a technology demonstrator to explore the art of the possible,” Schaefer says. “We see the greatest opportunity for transition in the hybrid propulsion system because it could be adapted very easily for vertical takeoff and landing aircraft or commercial aircraft.” ★
“This is the most difficult airplane I have worked on in my long professional life. Nothing like it has ever flown. This is truly a DARPA-hard problem.”
Systems engineer Carl Schaefer, LightningStrike program manager at Aurora Flight Sciences

About Debra Werner
A longtime contributor to Aerospace America, Debra is also a correspondent for Space News on the West Coast of the United States.
Related Posts
Stay Up to Date
Submit your email address to receive the latest industry and Aerospace America news.
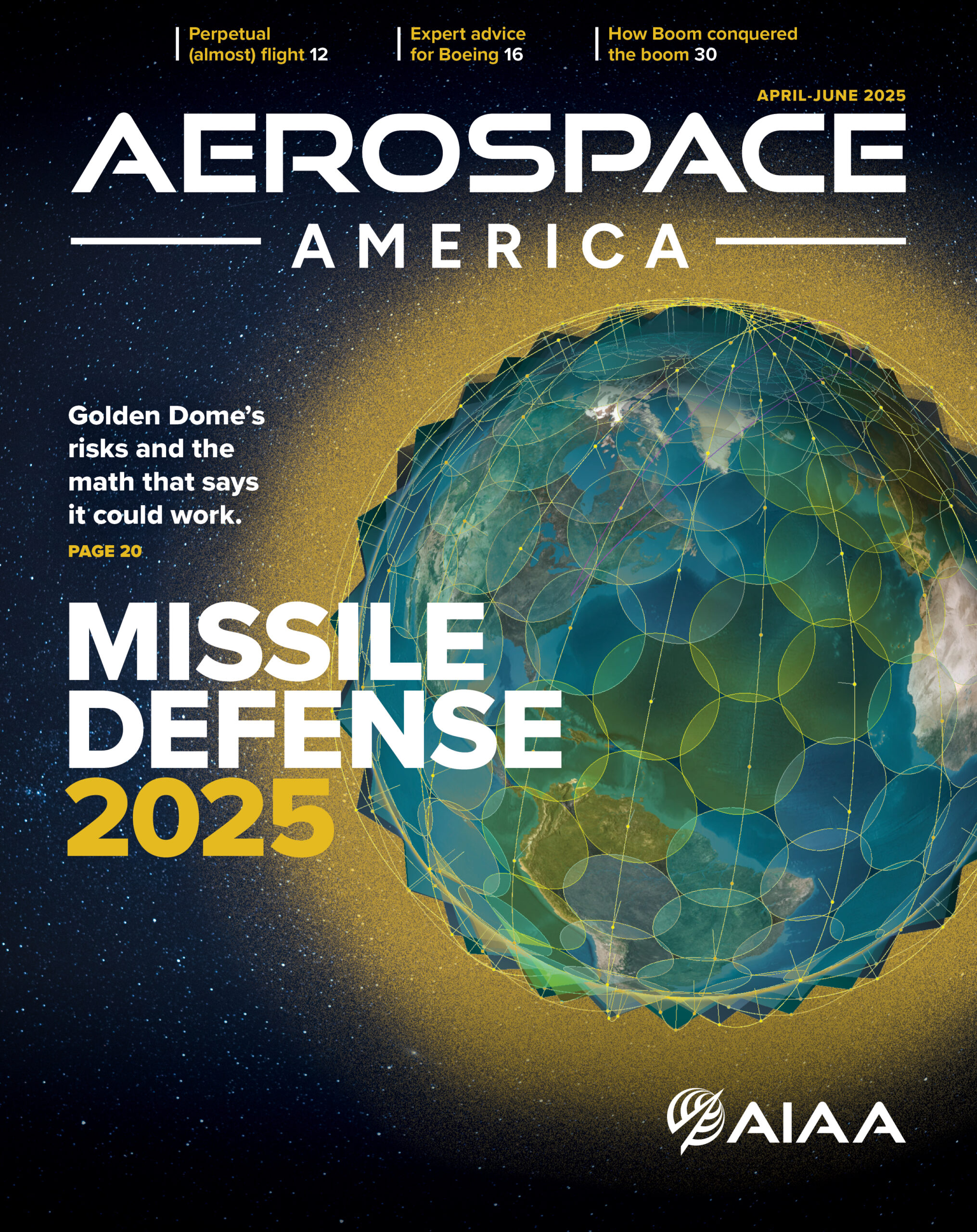
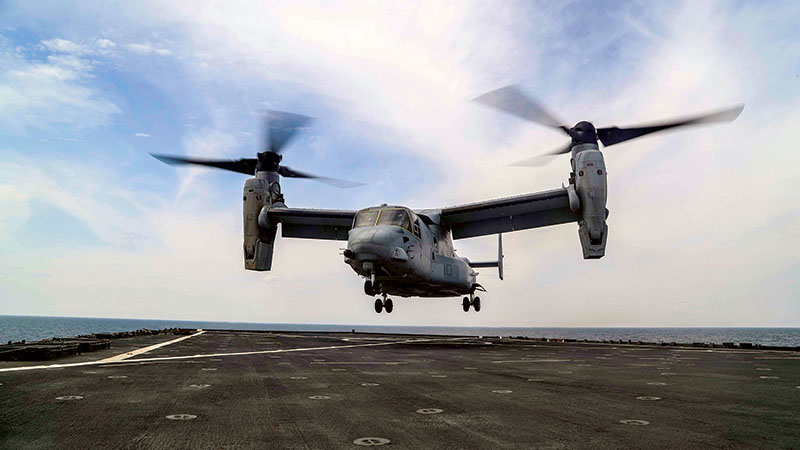
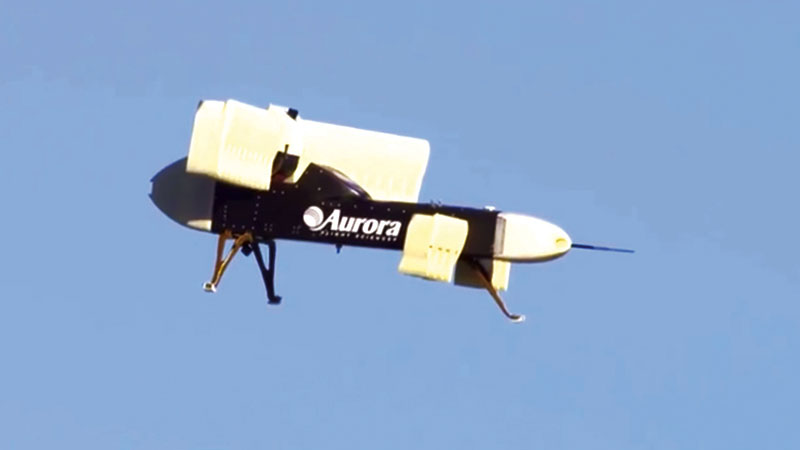