Stay Up to Date
Submit your email address to receive the latest industry and Aerospace America news.
NASA’s Orion spacecraft is intended to fly astronauts into lunar orbit on regular visits to a planned deep-space platform called the gateway. Veteran astronaut Tom Jones recently visited the Orion assembly line at Kennedy Space Center to assess the craft’s progress and path into translunar space.
I’ve seen my share of space hardware, and flew into orbit aboard some of it, but inspecting a spacecraft bound for the moon is something special. In mid-May, I received a close-up tour of Orion, a four-person ship capable of extended flight to and around the moon. The spacecraft is undergoing final assembly in Florida at the Kennedy Space Center Armstrong Operations and Checkout Building. Managers from NASA and Lockheed Martin, the spacecraft’s builder, walked me around the assembly floor to give me a sense of how this moon ship is coming together, and what challenges remain before Orion’s launch.
Orion is sized to support a crew independently on a 21-day lunar mission. The spacecraft can also dock at the planned Lunar Orbital Platform-Gateway for up to a year, drawing power and consumables from that outpost. An early version of Orion completed two unmanned orbits around Earth in 2014 and splashed down off California in Exploration Flight Test 1. The next Orion will undertake an uncrewed lunar voyage in early 2020 called Exploration Mission-1. EM-1 will be a critical checkout of Orion’s guidance, propulsion, communications and thermal control systems in advance of the first crewed Orion mission, EM-2 in 2022.
Mark Kirasich, NASA’s Orion program manager, tells me his team is finishing “the paper-intensive parts of the program — where you’re changing requirements and you’re moving designs on the PowerPoint charts — and we are really starting into production mode.”
His Orion team is simultaneously pursuing five major campaigns to make EM-1 a reality. The first is to finish assembly and testing of the EM-1 spacecraft. The second is to complete the welding of the EM-2 crew module (scheduled to happen in July) and ship it from the Michoud Assembly Facility in Louisiana to Kennedy (scheduled for August). The third task is to continue to procure and machine the thick aluminum sheets for the hull of the EM-3 crew module, marking the shift from developmental spacecraft to series production. The fourth is to fly the high-altitude Ascent Abort 2 test at Kennedy in April 2019. The fifth task is to prove Orion’s readiness for flight with the full-scale avionics and structural qualification versions in Denver and the propulsion system at NASA’s White Sands, New Mexico, facility. “There is more hardware and software in manufacturing, integration and test than we’ve ever had before,” Kirasich says.
Preparing for deep space
Kirasich describes EM-1 as “where we are trying to demonstrate and validate all critical systems to take people to low Earth orbit, to the moon and back again, and then re-enter the Earth’s atmosphere on a high-energy lunar return.”
The uncrewed Orion will be injected on a lunar trajectory by the Space Launch System’s Interim Cryogenic Propulsion Stage (ICPS, based on the Delta Cryogenic Second Stage flown on the Delta 3 and 4 boosters). Orion will perform a close lunar flyby and then, with a burn of its orbital maneuvering system engine, swing into a distant retrograde orbit around the moon. Orion will stay in this stable lunar orbit, roughly 70,000 kilometers above the moon, and farther from Earth than any human-rated spacecraft has ever traveled — until its extended deep-space systems checkout is complete.
To achieve the requirement of a daylight launch and Earth landing, Orion will remain in the distant retrograde orbit for either one or two 14-day revolutions, then perform an Earth-return maneuver to splash down in the Pacific. Adding the round-trip transit time to the moon, EM-1 will last between 26 and 42 days.
Some assembly (still) required
What I saw nearing completion at Kennedy were two major components of Orion’s crew module: the pressure vessel (or cabin) and the heat shield. I also saw the U.S.-built crew module adapter: the structural, power and fluids bridge between the crew module and the European Space Agency service module. Together, the launch abort system and the crew and service modules comprise the complete Orion spacecraft, to be stacked atop a Space Launch System booster on its inaugural launch.
The ESA service module is not yet at Kennedy. The service module, based partly on ESA’s Automated Transfer Vehicle cargo spacecraft, is being assembled by Airbus in Bremen, Germany. ESA is furnishing the service modules for the EM-1 and -2 flights, and Kirasich says discussions have started on procuring the modules for EM-3 and -4. The EM-1 service module was scheduled to be flown to Kennedy in early September.
Scott Wilson, who manages production of Orion for NASA at Kennedy, says the service module is “a whole new piece of hardware that we didn’t have with EFT-1 [Orion’s first test flight in 2014]. … This period of working together with [the Europeans] has been a learning curve that I think we got through pretty well.”
At Kennedy, engineers will bolt the crew module adapter to the top of the service module, weld fluid fittings, and mate electrical harnesses. After power-on functional tests and an initial run through the thermal/vacuum chamber, the service module will be mated with the crew module in early 2019.
The EM-1 spacecraft will then be flown to Ohio for high-stakes environmental qualification tests in the massive Plum Brook Station thermal/vacuum and acoustic chambers. During 60 days at vacuum, Orion will be baked and frozen to test its thermal control systems. Chilling the 30-meter-diameter, 37-meter-tall chamber to deep space conditions will consume eight tank trucks of liquid nitrogen daily.
One Plum Brook test will vent the cabin interior to vacuum to see whether spacecraft systems can withstand a cabin leak and keep the suited astronaut crew alive during a three-day return to Earth. To enable vacuum operation, Orion’s avionics and life support systems are conduction-cooled via water-chilled cold plates. (The space shuttle cabin systems were cooled by forced air circulation and cold plates.)
Plum Brook was chosen because “it’s a one-stop shop” for environmental testing,” says Wilson. The facility will test Orion’s ability to withstand launch and abort vibration and sound levels, just as intended during the Constellation return-to-the-moon program canceled in 2010. “In Constellation, we invested in upgrading the chamber and put in a very large shaker table that is capable of shaking the Altair lunar lander,” he says. “For Orion, our biggest acoustic input is from the launch abort system. It’s about 172 decibels, which is really unheard of. It’s about eight times more powerful than anything in the world in terms of size and acoustic volume.” The Plum Brook acoustic generators will subject Orion’s structures and cabin insulation to the intense sounds and vibrations characteristic of the launch abort motor firing just a few meters above the crew module.
Once Orion returns to Kennedy, Lockheed Martin will make necessary modifications, complete final qualification tests, and turn the spacecraft over to Kennedy ground operations by October 2019. After handover comes fueling and integration with the launch abort system, followed by stacking atop the SLS rocket for launch.
First crewed mission
EM-2’s pressure vessel, the airtight aluminum shell housing the crew, was scheduled to arrive at Kennedy by September. Technicians will then outfit this pressurized core with structural ribs, electrical harnesses, propellant tanks, and fluid lines to fashion the crew module.
If EM-1 goes well, NASA hopes to fly the EM-2 version of Orion with astronauts aboard in 2022. The moon is also EM-2’s destination, but the flight plan will be conservative. Because EM-1 will have flown without a full life support system, the EM-2 mission will first test that vital system in Earth’s vicinity.
After an SLS launch, Orion’s crew will test their systems for two revolutions in low Earth orbit. With all well, the ICPS will reignite to place Orion in a very high, 24-hour Earth orbit with a 71,500-km apogee and 230-km perigee.
Once separated from the upper stage, Orion will perform another day or two of life support and propulsion checkouts before committing to the moon. Given a “Go” by Mission Control, Orion’s service module main engine (a refurbished shuttle orbital maneuvering system engine) will propel the spacecraft onto a free-return lunar flyby trajectory.
On EM-2, the crew will not drop into lunar orbit, but take only an extended swing around the lunar far side. This free-return path protects against a propulsion failure, although the service module’s auxiliary thrusters are designed to back up the main engine. Notably, the flyby will take Orion some 8,890 kilometers beyond the moon, farther from Earth than any humans have ever traveled.
To prevent the service module’s re-entry debris from striking land, Orion will aim for a landing in the Pacific Ocean off California. Mission duration from launch to splashdown will total 10-14 days.
Orion and the gateway
Starting with EM-3, Orion production will be paced at one per year, with crews delivering and installing successive components of the Lunar Orbital Platform-Gateway in a “near-rectilinear halo orbit” about the moon. If you could see a spacecraft in this orbit from the vantage point of Earth, it would appear to circle the moon’s poles in a plane perpendicular to the Earth-moon line. For the gateway, the halo offers orbit stability, low fuel requirements for orbit maintenance, and excellent communications and visibility to both Earth and moon. The design orbit has a seven-day period, with a 71,000-km apolune over the lunar south pole and a 3,350-km perilune that offers good remote sensing and later, an advantageous departure point for the lunar surface. One drawback: Orion can abort to Earth from this halo orbit only once a week; in case of a serious emergency, the gateway will serve as a safe haven.
The first gateway component, a power and propulsion element, will be launched commercially into this halo orbit by a Delta 4 or Falcon Heavy. Orion’s EM-3 mission will bring along the second element, a habitation module, and dock with the power and propulsion element, inaugurating the gateway.
EM-3 and subsequent Orion missions will launch on SLS boosters equipped with exploration upper stages, more powerful than the interim cryogenic propulsion stage on EM-1 and -2. The added thrust will deliver the velocity change needed to carry 10-metric-ton gateway elements like the habitat module (crew quarters), airlock, partner modules and cargo containers. Docking missions require Orion to withstand larger structural loads, and to maneuver precisely, so EM-3 and later spacecraft will need software upgrades and physical reorientation of the aft thrusters.
Challenges — and excitement — ahead
Kirasich says that one difficult challenge for EM-1 is to qualify remaining parts before they are installed on Orion. Late qualification failures mean that corresponding parts on the spacecraft must be pulled and modified back at the manufacturer, a time-consuming process just completed for inertial measurement units and some phased array communication antennas. Kirasich is seeing steady progress, but the qualification process is still only 60 percent complete.
One problem overcome was the qualification of the beachball-shaped airbags that tip the conical crew module upright, onto its broad heat shield, after splashdown. On EFT-1, three out of five didn’t fully deploy. To retire the risk of leaving the crew dangling from their seat straps, more than a dozen design, manufacturing and installation changes were made to ensure proper airbag function.
NASA’s Wilson is aware of the significance of the approaching EM-1 flight. “As a little kid I watched the Apollo launches, and I was so excited about that stuff. Now, being in the same building [where Apollo was tested] and building things that go beyond where Apollo could go — being part of that is amazing. The closer we get to launch, the more excited I get.”
Building and flying these moon ships now seems to be a national commitment, at long last. The Orion I saw coming together represents U.S. leadership in space — at the moon, the asteroids and Mars — for a generation. Details of our path may change, but Orion demonstrates to me our determination to chart new frontiers in space — and soon.
About Tom Risen
As our staff reporter from 2017-2018, Tom covered breaking news and wrote features. He has reported for U.S. News & World Report, Slate and Atlantic Media.
Related Posts
Stay Up to Date
Submit your email address to receive the latest industry and Aerospace America news.
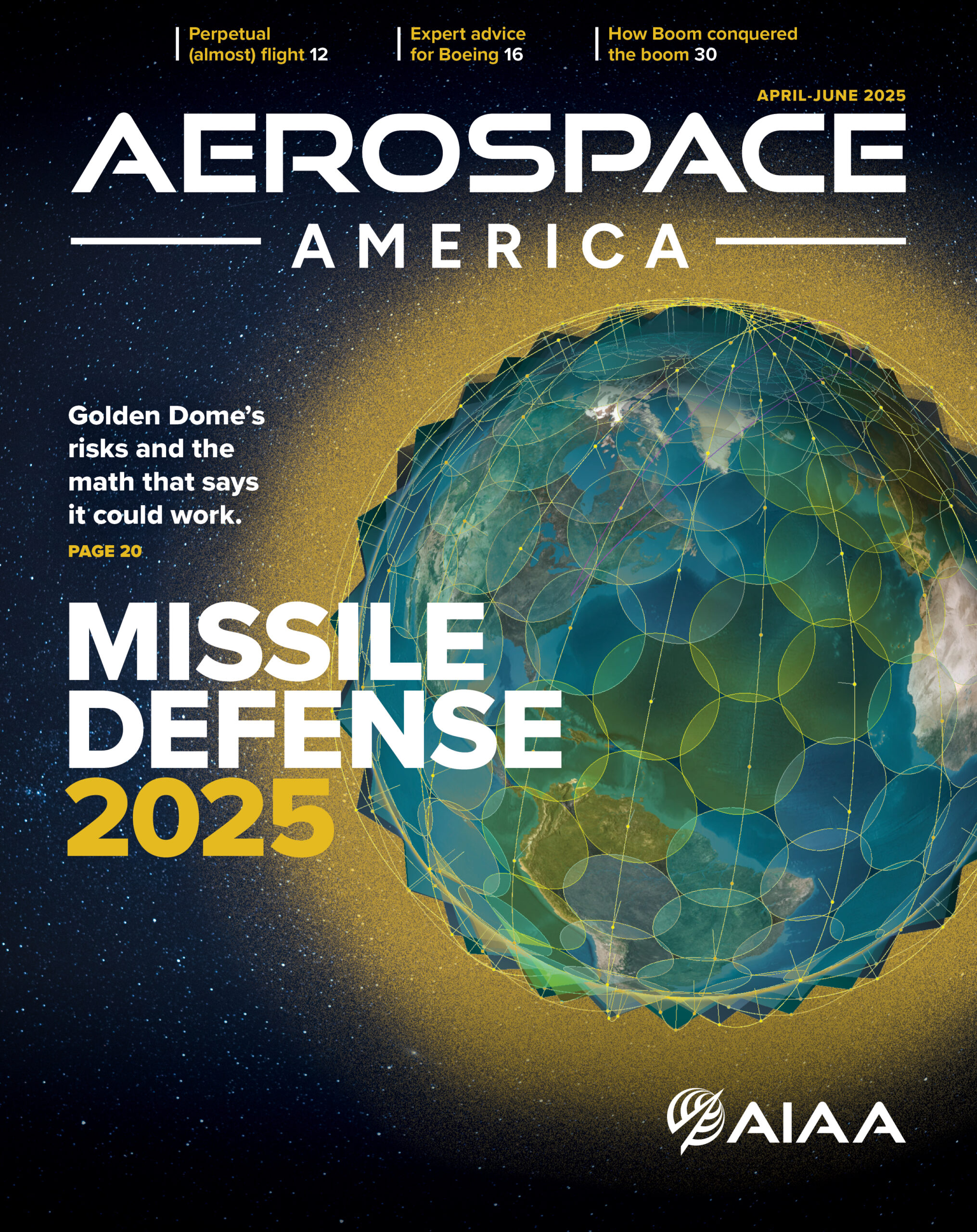
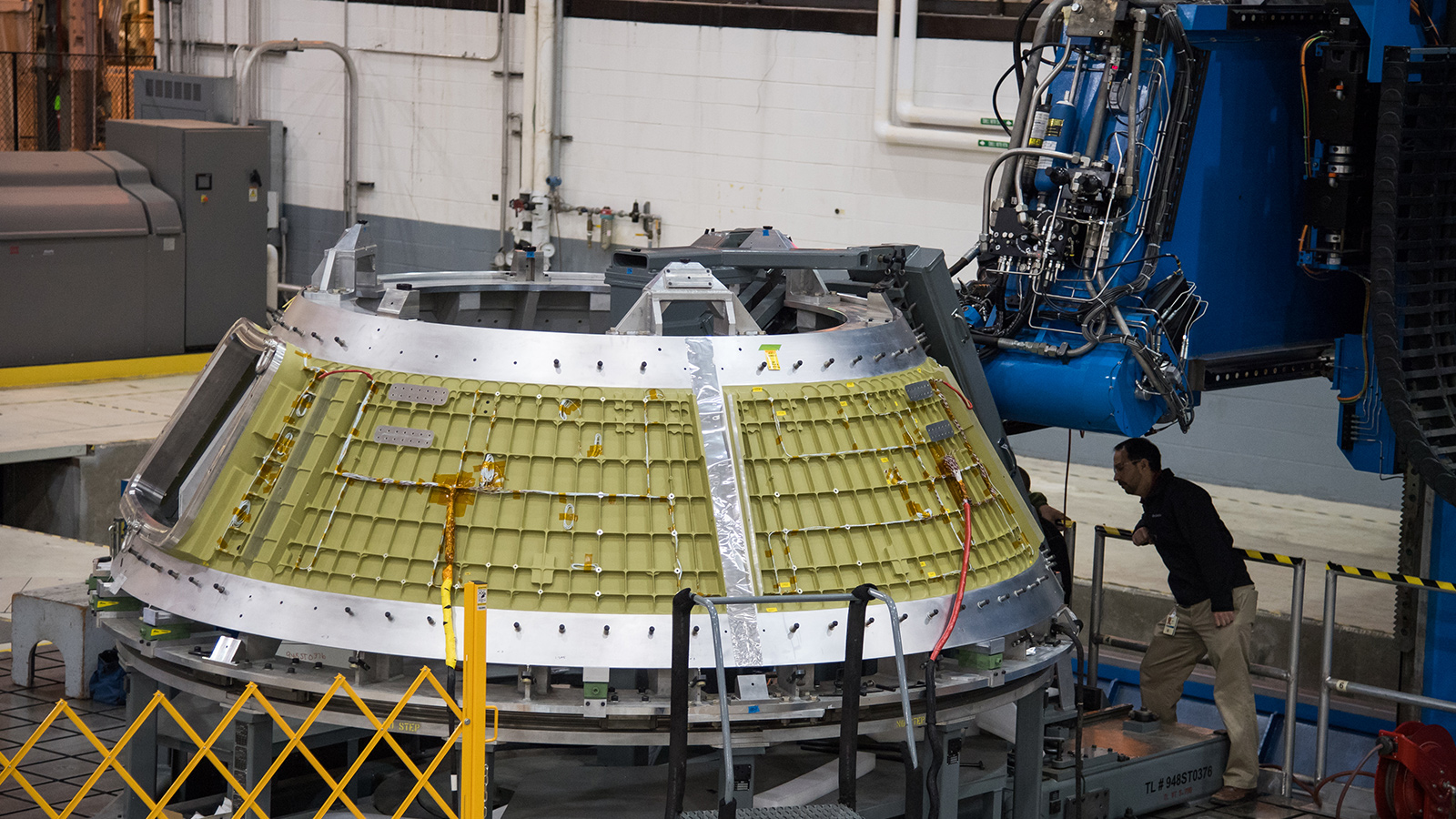
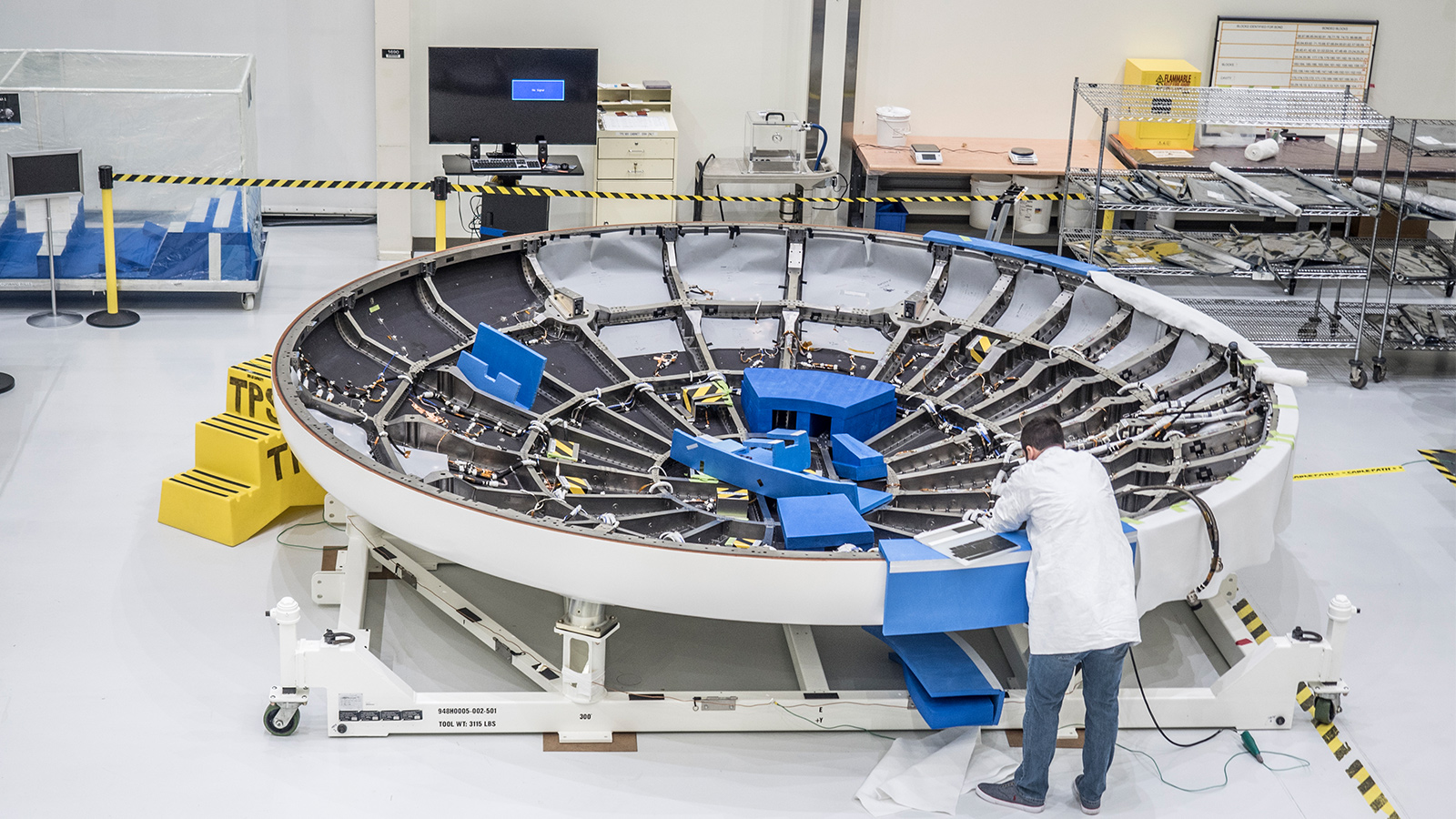
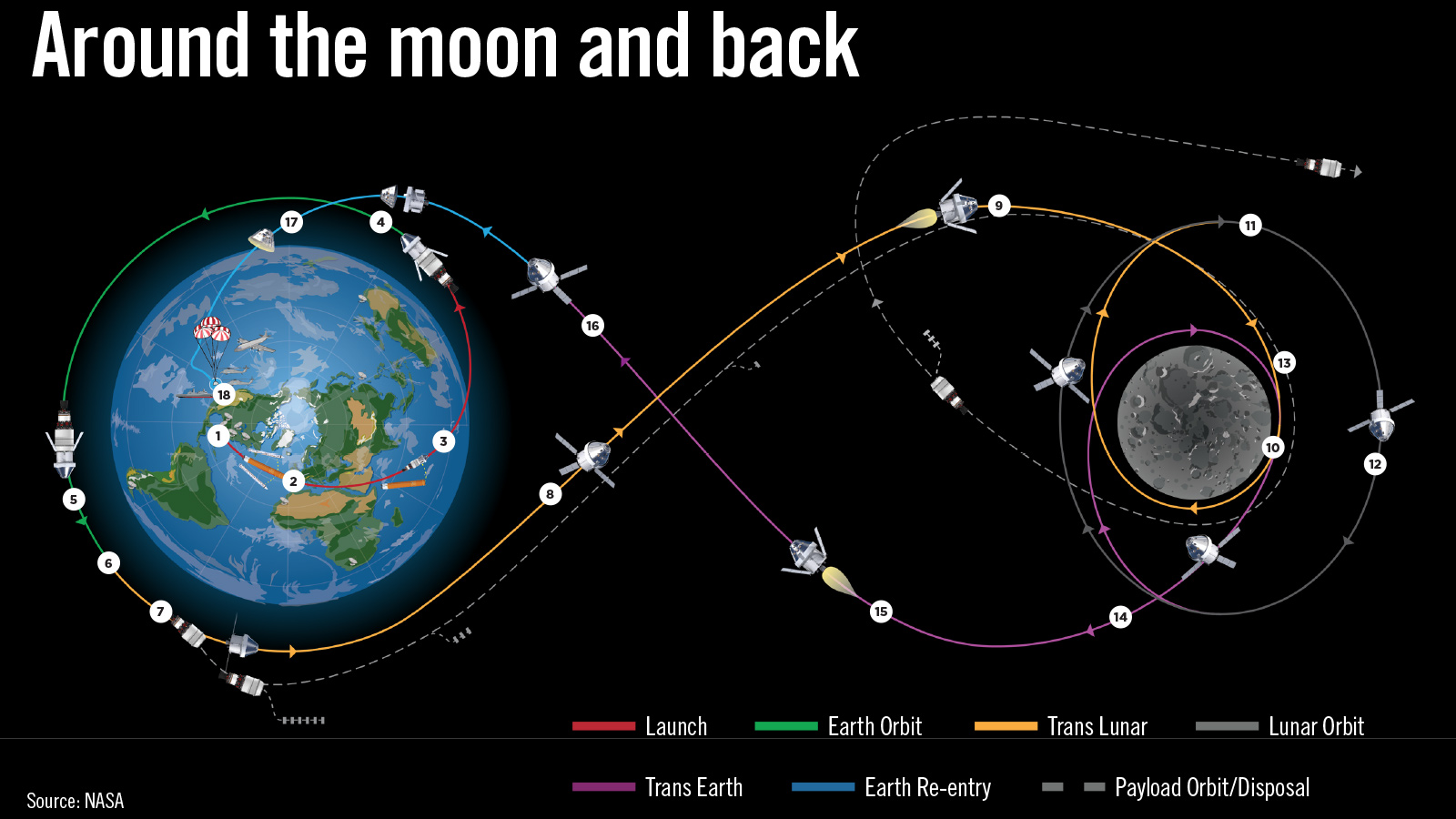
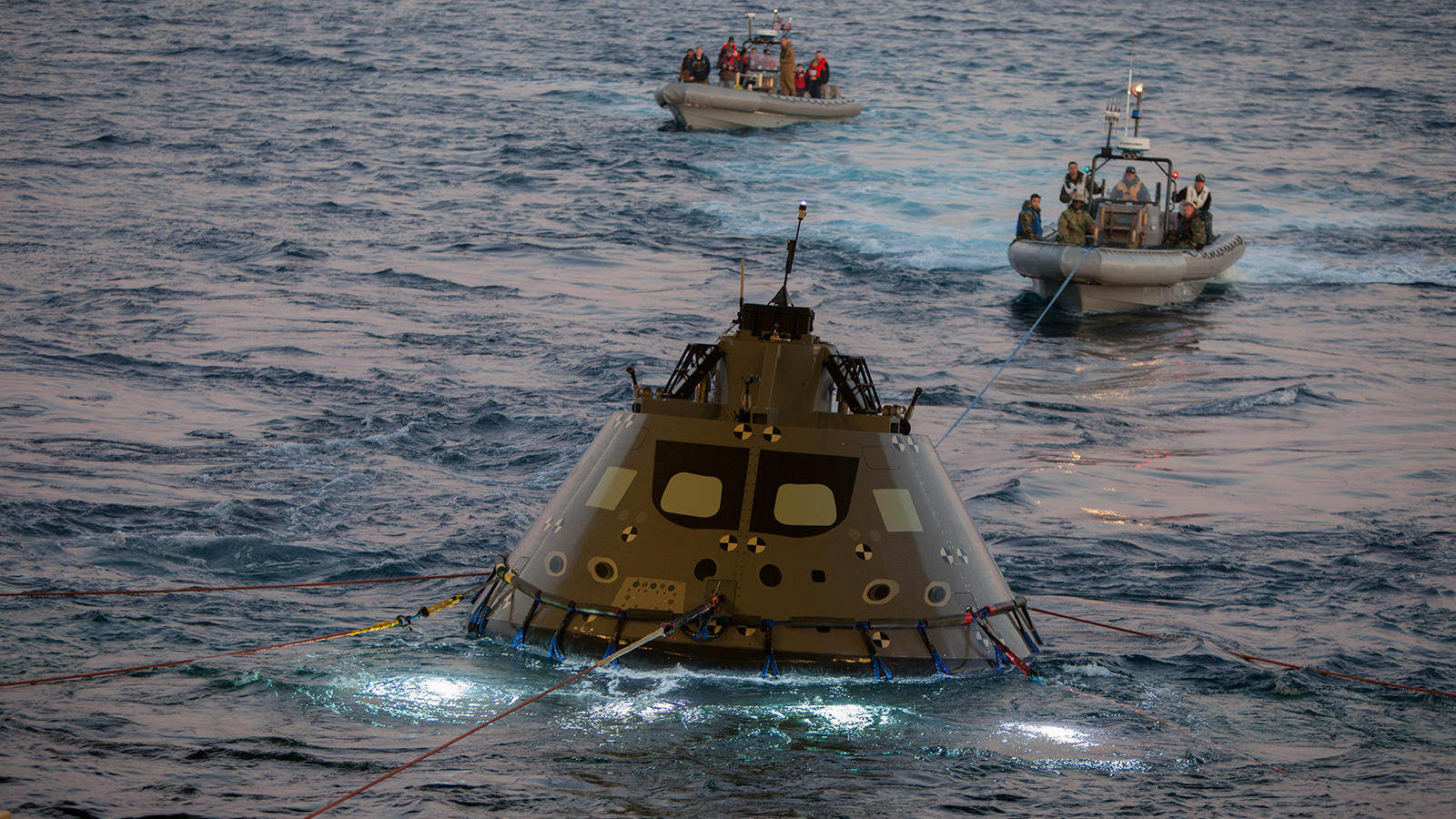