Stay Up to Date
Submit your email address to receive the latest industry and Aerospace America news.
Mark Cousin
Mark Cousin’s staff must create the technologies that will propel Airbus into the future of flight. If all goes as planned, digitally manufactured autonomous aircraft will shuttle passengers quietly and cleanly through a well-organized airspace. This must be true whether passengers are riding in small urban air mobility craft or in airliners. Cousin is head of A3, pronounced “A cubed,” the DARPA-inspired innovation center that Airbus established in 2015 in California’s Silicon Valley. I interviewed Cousin in June at the AIAA Aviation Forum in Dallas.
IN HIS WORDS
Parallel development
What we’re trying to do in A3 is put to one side the traditional approach of developing technology until it’s mature and then building the demonstrator. We turn that on its head and say, “OK, let’s set an aggressive goal to build the demonstrator of something that we think is possible but develop the technology while we’re developing the project.” We do make our projects really time limited, so typically two to three years as a maximum to actually build and develop a sort of minimum viable product of something groundbreaking, something disruptive. We don’t expect all of our projects to be successful.
Learning from success and failure
I would say we would expect at least 50% of our projects to actually transition into something useful, something meaningful for one of the business units of our company. We try to make sure now that all of the projects we run have some serious sponsorship within the business, so we’re not just doing stuff that’s cool; we’re doing stuff that’s cool but has some potential impact and support within the business. And I think in the first four years we’ve achieved about that. You know we’ve had some projects which have been very successful and have spawned in fact a new division within Airbus called Urban Air Mobility. And we’ve had some other projects which have not been successful in the traditional sense, but I think one of the things we’ve also learned is that you very often learn as much from failure as you do from success.
Urban air management
We have a big project, which is part of this urban air mobility push for urban traffic management, which will be absolutely critical once we have hundreds or even thousands of vehicles flying in the skies. We’ll need a completely new means of controlling the low altitude airspace above cities. For example, typically in São Paulo today, we can have only six helicopters operational in the air at the same time. So the future requires not six, maybe 600 or even 6,000 vehicles airborne.
Flying clean on battery power
We have a very, very clear view from the cities that we’ve engaged with that these vehicles will have to be completely emissions free, otherwise they won’t be welcome in modern cities where pollution is a major issue. With what I see today on the development of battery technology, I’m pretty optimistic, in fact, very optimistic, that the level of performance that we require to make these vehicles viable will be achieved within the next two or three years. The only real question is whether it will limit how big you can make the vehicle, how many passengers it can carry, or how far it can fly. But the technology is already very close to where we need it to be. And there is a huge amount of research going into battery development.
Automation vs. autonomy
The business case for urban air mobility doesn’t work if those vehicles are not autonomous at some point in the future. If they have to be piloted, then the business case doesn’t close. Also in our civil aircraft business, we know we have to move toward more autonomous aircraft. I draw a big distinction here between automation and autonomy. What we’ve done to date in aerospace is automate a lot of tasks. Autonomy is something very different. Autonomy means that the vehicle is making decisions and learning from its own mistakes. So we recognize that if we want the commercial aerospace business to continue growing as it is today — and it’s predicted to double in size — we will not be able to do that if we continue with two or even four pilots in the cockpit.
Replicating a human pilot
If you want to land an aircraft at an airport that’s not equipped with sophisticated instrument landing systems, that’s something that’s done very well by a human pilot today. We’re in the process of developing the ability to do that with an automated system, but that’s quite difficult because you’re doing that with a high-definition camera. It has to identify the runway, has to identify the touchdown point, has to fly the approach as a human pilot would. We’re really on the edge of both sensing capability and computing capability to reproduce what a human pilot can do. On the other side, one of the huge potential benefits of machine learning is that if you think about incidents or even accidents that occur today with an aircraft, the only person who learns is the pilot in that particular flight. If you have an autonomous vehicle where the software is learning, then every single aircraft in the fleet will learn from every single event or occurrence. We need to be able to have a system which is able to start taking decisions when things don’t go as planned, and project Wayfinder is really charting uncharted territory.
The coming pilot shortage
Our objective is to move toward commercial aircraft with a single pilot onboard. That’s largely driven by the fact that if we extrapolate the growth of aviation today, then we will need to train 600,000 pilots in the next 20 years. Put that into context: We’ve only trained 200,000 pilots since the start of commercial aviation. So we know if we don’t do something, the growth of the industry is going to be constrained by the availability of pilots. Now if you want to go to an aircraft with a single pilot onboard, you basically need to design an autonomous vehicle where the vehicle is going to take all of the decisions on what it should do, even in failure cases, and the crew member onboard is really there as performing the role that the pilot nonflying in the cockpit today would be performing. So there’d still be a human being onboard to intervene in extreme situations, but the vehicle or the architecture of the vehicle really has to be designed around an autonomous vehicle, which is a major departure from what we design today where we have a lot of automation but no real autonomy.
Certification complication for machine learning Today we certify flight control software, which is fixed; it doesn’t change. If we now want to certify something which is going to evolve with time, it’s a different challenge. So certifiable autonomy is something which is really a major challenge and something which we’re putting a lot of effort into.
Going digital
The digitalization of the manufacturing process of the aircraft is obviously critical. We’re now building aircraft at production rates that we never, ever envisaged. We’ll deliver nearly 900 aircraft this year. And we’re building single aisle, our A320 family of aircraft, we’re building more than two aircraft a day. And those aircraft were designed in an era when we were building one or two a week. So the digitalization of not only the design, but also the production process of those aircraft is something that’s critical. But also then the evolution of how those aircraft develop and behave once they’re in service, and that’s where the digital twin really comes in. If you have a digital twin, you’re able to model and follow the evolution of the aircraft and what you expect the, for example, the maintenance required on the aircraft to be in service after it’s been delivered. So you’re using your digital model of the aircraft to predict what you will need to do with the aircraft in service to make its operation the most efficient that it can be.
The image at the top is Vahana, a vertical takeoff and landing aircraft by A3.

About Ben Iannotta
As editor-in-chief from 2013 to March 2025, Ben kept the magazine and its news coverage on the cutting edge of journalism. He began working for the magazine in the 1990s as a freelance contributor. He was editor of C4ISR Journal and has written for Air & Space Smithsonian, New Scientist, Popular Mechanics, Reuters and Space News.
Stay Up to Date
Submit your email address to receive the latest industry and Aerospace America news.
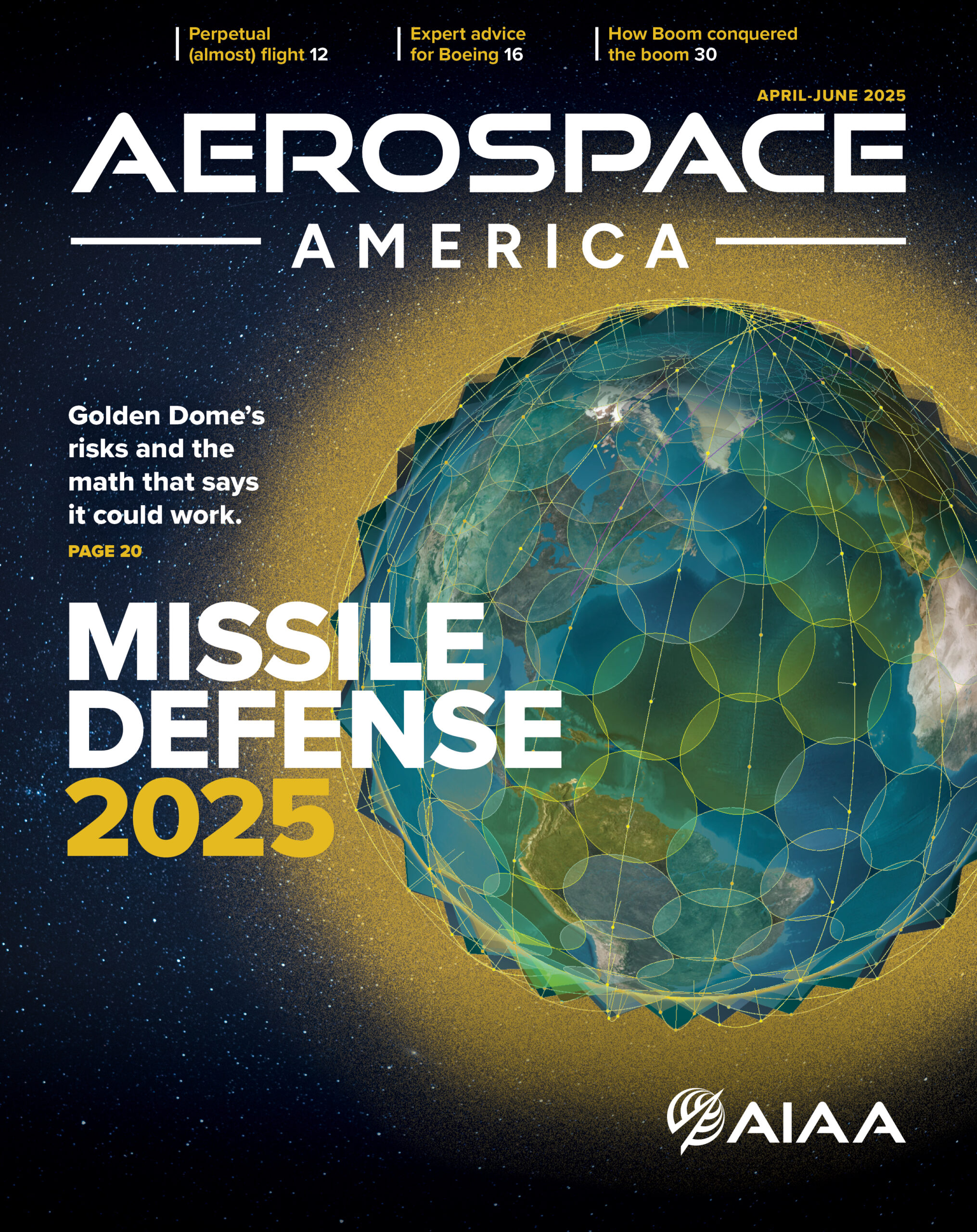
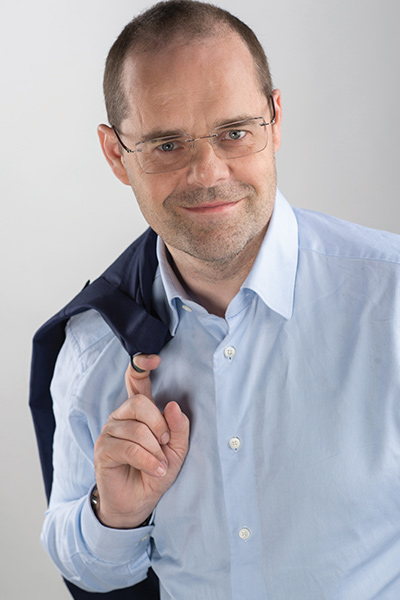