Stay Up to Date
Submit your email address to receive the latest industry and Aerospace America news.
Companies face an array of crucial technical decisions as they pioneer additive manufacturing techniques for parts on commercial aircraft that must carry hundreds of passengers safely to their destinations.
Two kinds of additively manufactured parts on today’s Boeing 787s offer a study in contrasts between techniques for additive manufacturing, also called 3D printing, and the kinds of companies that do this work.
Consider first the fuel nozzles in the GEnx engines that power more than half of 787s. They were made in Auburn, Alabama, by the additive manufacturing unit of the century-old, $120 billion-a year industrial giant GE through a process centered on fusing metal powder with lasers. Next, consider the 33-centimeter-long titanium fittings that anchor the floor of the aft kitchen galley to the 787 airframe and bear structural stresses. These were made in Oslo, Norway, and Plattsburgh, New York, by the Norwegian company Norsk Titanium, an 11-year-old firm of about 140 employees. Norsk applied an entirely different technique tailored for larger structures.
For Norsk, several early decisions determined its path to production.
In theory, Norsk could have started by making parts for business sectors other than aerospace, since those sectors are less regulated. From its startup in 2007, though, Norsk elected to make aerospace parts. “We wanted to take on the hard one first,” explains Chief Technology Officer Carl Johnson, a mechanical engineer who joined Norsk in 2016 from Northrop Grumman. If Norsk could meet the standards of this most demanding sector, it could offer its additive manufacturing to any market, something it has begun doing.
Some firms sell specialized machines for additive manufacturing, but Norsk decided early on “to make parts, not sell machines,” Johnson says. In fact, in its early days, Norsk had about as many metallurgists as machine designers. The metallurgists were essential for Norsk to meet the rigorous requirements, including strength and uniformity, of the aerospace sector.
Norsk decided to focus on titanium partly because of the metal’s increasing importance in aviation and partly because it is very expensive at nearly $7 per gram. One big advantage of additive manufacturing is that it cuts the buy-to-fly ratio, that is, the volume of material that must be purchased relative to the volume in the finished part. When parts are machined, excess material must be scrapped or expensively recycled. Additive manufacturing leaves much less leftover material to be recycled. By working with titanium, Norsk would be saving plenty of a high-value metal compared to machining.
Norsk elected to build large titanium structural parts, hence the galley fittings. The question was which basic additive technique the company should adapt to meet its needs. Most aerospace firms have concentrated on powder bed fusion, also known as direct metal laser sintering. In this technique, lasers or electron beams melt and fuse powdered metals. This is how GE printed its fuel nozzles.
But powder bed is really suited for small, intricate parts, such as GE’s nozzles, says Norsk Chief Commercial Officer Chet Fuller, who joined the company in 2015. It is a slow process in which a few dozen grams of metal are laid down per hour. Norsk would be producing parts weighing 2 kilograms or more. “Powder takes too long for that,” says Fuller. Norsk wanted a technique to produce parts on an industrial scale of kilograms per hour.
To do that, Norsk developed its own version of direct metal deposition, a technique in which metal powders or wires in the case of Norsk are deposited into shape via a plasma, with dimensions and material integrity managed by a control system. Norsk calls its patented technique Rapid Plasma Deposition, or RPD, and it built its own machines to do it.
As with all additive techniques, the process starts with a computer assisted design drawing of the part to be printed. This data is entered into a control system programmed to generate deposition coordinates for the part.
These coordinates are fed into the production machine, the latest of which is Norsk’s Merke 4.
Norsk’s titanium wire starts out at room temperature and is fed into inert argon gas atmosphere in the Merke 4’s build chamber. An electrode in a torch forms a plasma arc that is forced through a nozzle and exits at high speed and a very high temperature. This arc in turn raises the wire’s temperature by thousands of degrees, momentarily melting it into a liquid that is laid down according to the computer drawing. Once laid and separated from the arc, the liquid cools and solidifies in milliseconds. Then the process repeats to lay down the next layer. When the part is fully formed into its basic shape, it is machined into its final shape.
Norsk chose a wire feedstock rather than titanium powder because wire has a higher deposition rate and is thus faster to lay down than powder. And metal powders, which must be atomized from bar stock, can be extremely expensive. Very expensive powder could reduce or eliminate the advantage in buy-to-fly ratio. Titanium wire costs more per kilogram than bar stock, but “not dramatically so,” Fuller notes.
The engineers looked at various standard diameters of titanium wire that are produced in large and therefore affordable volumes. They found the most efficient diameter was 1.6 millimeters. Suppliers of this standard titanium wire must only meet Norsk’s specifications for the wire’s twist and cleanliness.
Direct metal deposition processes usually must operate in a vacuum. Norsk chose plasma with positive pressure and no vacuum because it makes loading and unloading parts more efficient. There was no need to create vacuum conditions for each new part, which takes time and slows production.
Norsk has adjusted the design of its Merke machines through four generations.
“We went from very large machines to smaller ones, we even looked at robotic arms,” Johnson says. “What we eventually came up with was a machine that reduced variability and enhances control.”
Norsk had its first machine, the relatively simple Merke 1, up and running in 2008. By 2010, the second-generation Merke 2 was in operation. This machine applied dual-torches to produce the plasma arcs and to make test parts for qualification and delivery to customers. This was the prototype that cleared the way for development of the RPD process.
By 2012, Norsk had moved on to the Merke 3. Like Merke 2, its six-axis robots manipulated the torch head and substrate, the surface on which printing is done. Norsk improved the processing monitoring system and made proprietary upgrades for manufacturing larger and more complex parts. This is the version that made sample titanium materials for FAA material testing.
The current machine, Merke 4, was ready by 2015. In this version, computerized numerical controls rather than robots manipulate the torch head and substrate. Norsk designed Merke 4 for serial production with further upgrades in its monitoring and closed-loop control systems. Merke 4 can build parts up to 900 millimeters by 600 mm by 300 mm, depositing titanium rapidly at five to 10 kg per hour, the company says.
Norsk says its monitoring and control systems are highly proprietary and crucial to its success. The Merke 4 now monitors 600 parameters per second as a part is printed. The sampling rate for each parameter is chosen according to how often tests have shown the parameter can change. Parameters for electricity, both voltage and current, are sampled at very high rates. Sampling covers the current between the work piece and the plasma and the current between the wire and the gas that is melting the wire. Sensors sample other parameters at different rates, according to how often they might change.
Monitoring of some parameters feeds back to the production machine, controlling its operation. That is the closed-loop part of monitoring. Other parameters are just monitored to prove that a part has been produced under required conditions.
A major goal of control and monitoring is to ensure that the microstructure of each part is homogeneous and meets specifications.
“We are unique in the way we control our process and the way we document our process,” Johnson stresses. “We are meticulous in our record-keeping and very consistent in our quality.”
For installation in aircraft, regulators must certify the additive process itself, the materials produced by the process and the specific parts produced. The first two certifications are the toughest, and took years to achieve. Once that was done, it took about 10 months to certify the 787 fittings in 2017.
Norsk produced and tested roughly two tons of materials and parts to obtain certification of its 787 parts. That meant 2,000 individual specimens at a cost of $700,000, in addition to the cost of manufacturing the test material itself. “Testing wasn’t difficult, just time-consuming and expensive,” Johnson says.
Apart from satisfying customers and regulators, meticulous monitoring also provides a big economic advantage. Unlike some additive processes, which are certified machine by machine because each machine may differ slightly in its operation, all three Merke 4s in Norway and now nine in upstate New York have been certified by FAA. Norsk can thus achieve its aim of producing parts at industrial scale.
For about a year now, Norsk has been producing four parts, and three part numbers, for 10 Boeing 787s per month. The near-net shape parts produced by Norsk are machined to final parts by a supply-chain partner.
This machining generates some scrap titanium, but not nearly as much as cutting parts from blocks. Fuller estimates that a typical 2 kg structural titanium part on an aircraft would have to be cut from a 30 kg block, generating 28 kg of scrap. The same part, printed by Norsk and machined to final shape, would require only 6 kg of titanium wire. That’s money in the bank for Boeing and Norsk.
“We went from very large machines to smaller ones, we even looked at robotic arms. What we eventually came up with was a machine that reduced variability and enhances control.”
Norsk Chief Technology Officer Carl Johnson

About cat hofacker
As acting editor-in-chief, Cat guides our coverage, keeps production of the print magazine on schedule and edits all articles. She became associate editor in 2021 after two years as our staff reporter. Cat joined us in 2019 after covering the 2018 congressional midterm elections as an intern for USA Today.
Related Posts
Stay Up to Date
Submit your email address to receive the latest industry and Aerospace America news.
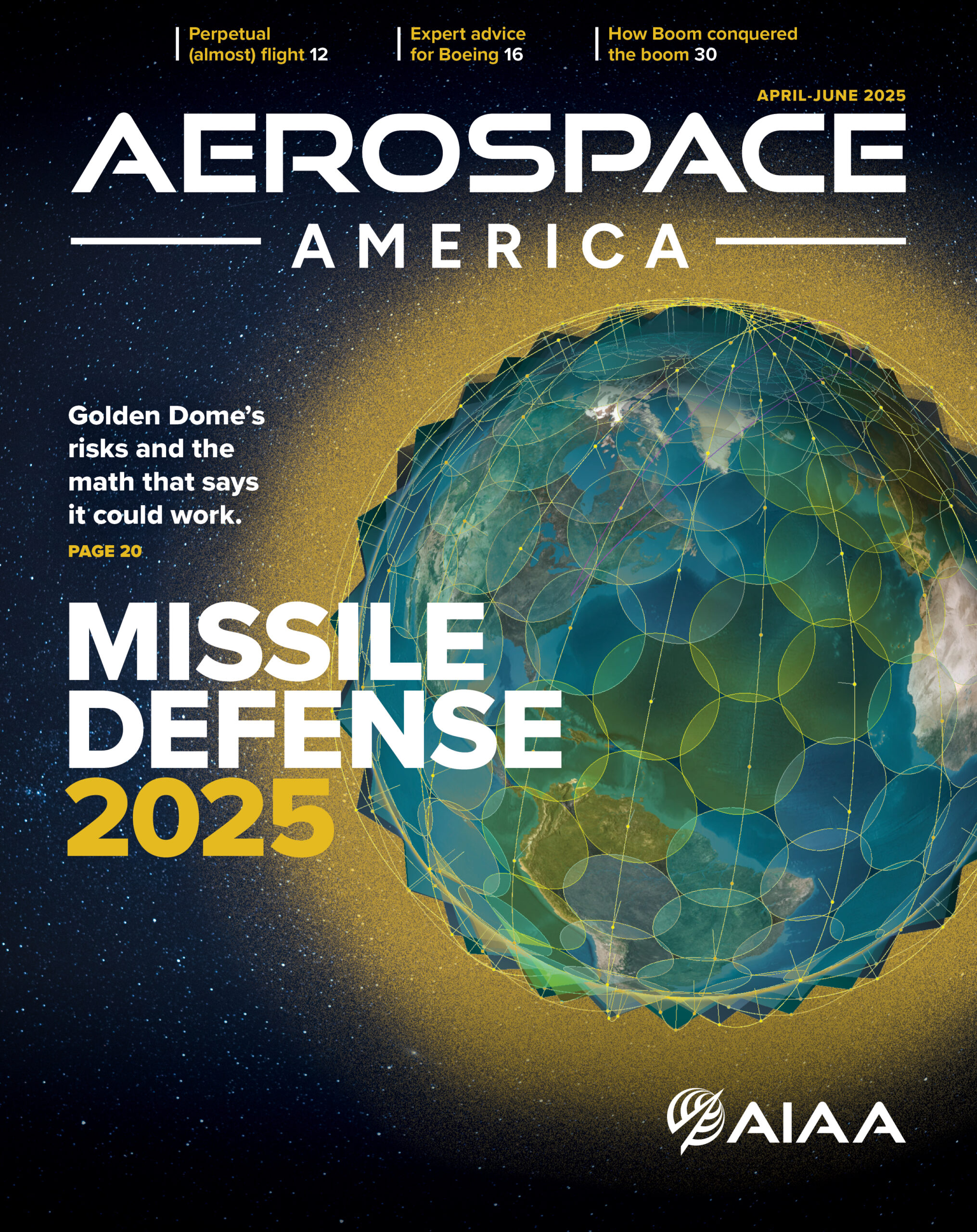
