Stay Up to Date
Submit your email address to receive the latest industry and Aerospace America news.
Today, returning payloads to Earth or delivering them to Mars means facing the tyranny of the rocket shroud. Payloads must be protected by rigid heat shields, and this reality limits their mass, since heavier payloads need wider shields, but the shield must fit in the shroud. What if a shield could be inflated in space? A November test by NASA pointed the way, but the mission left a key challenge to be addressed. Keith Button tells the story.
In a gravel lot outside of Bozeman, Montana, a handful of space wonks peered from a safe distance at a long, empty plastic bag attached to a metal pipe jutting horizontally from a stack of sandbags. Among them was John Bognar, who later explained the experiment to me over the phone. Bognar is a chemist and owner of Anasphere, a three-person space technology company in nearby Logan. He counted “three, two, one” and hit a red button on a black box. Behind the sandbags, a loud “pop” emanated from a metal drum, followed by a “whoosh.” The pop was the sound of an electric charge igniting small discs of thermite, a pyrotechnic substance commonly employed by welders. This ignition produced heat that triggered a chemical reaction in which hydrogen molecules were dislodged from granules of a metal hydride in the drum to form hydrogen gas. The whoosh was the sound of gas slowly inflating the plastic bag, a successful result that was met with a subdued reaction from the NASA managers in the group.
“We always have very serious audiences,” Bognar notes. “They’re really trying to take in a lot.”
This 2021 experiment demonstrated a simple gas generator: a device that turns a solid into a gas. The technology is a key missing ingredient in an initiative by NASA and industry players to liberate themselves from the need to squeeze a rigid, dome-shaped heat shield into a rocket shroud every time they want to deliver a payload to the surface of Mars or back to Earth. What if a fabric heat shield could be packaged in the shroud and inflated in space? NASA took a step toward that vision in November with LOFTID, the Low-Earth Orbit Flight Test of an Inflatable Decelerator. NASA’s early analysis of this test suggests that the 6-meter-diameter shield indeed kept the temperatures on its aft side at acceptable levels as it plowed back into the atmosphere at 8.1 kilometers per second (nearly Mach 24) over the Pacific Ocean, following its release from a United Launch Alliance Atlas V rocket.
LOFTID was a breakthrough in the field of HIADs, short for hypersonic inflatable aerodynamic decelerators, but the inflation technique, though potentially useful for returning equipment to Earth, was not what NASA wants for deep space. This handmade fabric shield was inflated by high-pressure nitrogen gas released from “a glorified scuba tank” on the Atlas V upper stage, says Neal Cheatwood, NASA’s senior technologist for planetary entry, descent and landing, and one of those on hand for Anasphere’s demonstration.
The mass and volume of this inflation system were too high for a Mars mission. The tank, the gas and the series of regulators that lowered the pressure before inflation weighed about 135 kilograms. As for the nitrogen, that would be “a lot of volume of gas that you’d have to store for a very long time,” says Cheatwood. “To go to Mars, even if we did a fast trajectory, you’re talking about storing it for three months.” Hence the desire to turn a solid into a gas, despite the hurdles.
“One of the biggest engineering challenges to using gas generators for space applications is that, quite frankly, no one is doing that yet,” says Hillary Blakeley, who was NASA’s inflation system lead for LOFTID.
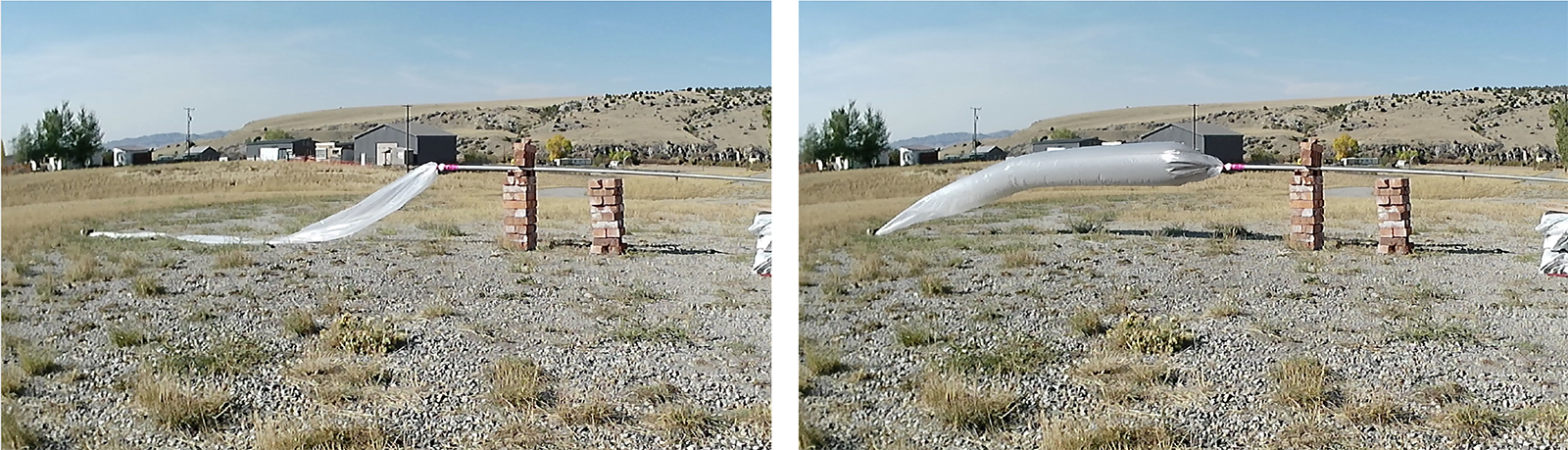
So far, only modest funding has been spent toward a better inflation system. Most recently, NASA’s Small Business Innovative Research program awarded a combined $1.05 million to Anasphere and two other companies: Outpost Technologies of Santa Monica, California, which plans to return satellites to Earth for reuse, and Storm Castle Technical Products, a Montana company that is developing lightweight housings for Anasphere’s hydrogen gas generator cores. Because hydrogen might not be needed for Earth applications, the other companies are looking at lower-cost generators that would rely on carbon monoxide, carbon dioxide or nitrogen, Cheatwood says.
On to Mars
The payload demands for a human mission to Mars would be enormous. Today, the largest rocket fairings are about 5 meters in diameter, so Cheatwood estimates a rigid aeroshell could be, at most, 4.7 meters wide. If a crew landed on Mars protected by such an aeroshell, “I don’t know what they would do when they got there, or how long they would last,” Cheatwood says. There would be little room or mass allocation for supplies. In fact, a crew of four would require 80 metric tons of equipment — the landing craft, food, water, oxygen, habitat, other gear and launch vehicle to leave Mars. This would need to be delivered in multiple batches of 20 to 25 metric tons each, one of those missions carrying the crew as well.
Delivering a payload of that mass isn’t possible with a 4.7-meter heat shield because it’s too small to create enough drag to slow down the craft quickly enough as it enters the atmosphere, which in turn means the payload would be subject to higher temperatures. To guide a single 20-ton payload through the Martian atmosphere, a 16- to 20-meter heat shield is required. (SpaceX is proposing to deliver humans and their equipment to Mars with a single Starship upper stage that would land vertically on the surface with retrorockets and then take off when the time came to depart, but that idea relies on refueling with carbon dioxide and water from the Martian environment.)
To inflate a HIAD for a Mars mission, the most promising concept involves powdered metal hydrides like those in the Anasphere experiment. Unlike the explosive chemical reaction that inflates a car’s airbags with nitrogen in a split second, the space version would need to fill up much more slowly so that the inflatable structure can get by with thin, light walls. Hydrogen gas derived this way provides the largest volume of gas per kilogram of solid, Cheatwood explains.
The structure of the heat shield needs to be lightweight enough that it can be folded compactly into a rocket fairing but also be arranged in such a way that when inflated, it withstands the heat and pressures of reentry. So for LOFTID, NASA covered the downward-facing side of the HIAD with a ceramic-fiber-cloth-and-insulation blanket capable of withstanding 1,600 degrees Celsius. This blanket covered concentric rings of textiles, each ring with an inflatable fluoropolymer liner (think the inner tube in a bicycle tire) encased by a layer of braided nylon or Kevlar — the tire, in this analogy. Once inflated, the rings acted as a blunt cone-shaped brake, slowing LOFTID as it plowed through the atmosphere.
For inflation, NASA needs the gas temperature to be lower than 200 degrees Celsius so it won’t melt the liner, and the gas must be nearly free of contaminants that could damage the liner, such as metal particles or chemicals that react with the material, or water vapor that could cause the inflatable shield to lose too much pressure as the water cools.
Cookies and cans
As Bognar developed his hydrogen gas generator, he knew he needed to create a controlled chemical reaction so the gas wouldn’t release suddenly but rather over 30 seconds to 2 minutes. This required keeping the thermite-triggering material separate, so the pace of the reaction could be controlled.
For the demonstration in Montana, Bognar designed an Oreo cookie-like stack of alternating layers of solid thermite and powdered hydride. The thermite was ignited by a NASA Standard Initiator, a pyrotechnic device that’s “like a bottle rocket ignitor on steroids,” Bognar says.
“We very much rely on this principle of transferring heat from one to the other so that we can control reaction rates,” he says.
Because the pressure created by the controlled reaction isn’t extreme, the gas generation chamber can be designed in almost any shape necessary to fit it aboard a spacecraft.
Prior to selecting the metal drum employed for the 2021 test, Bognar chose a standard steel coffee can for the chamber that houses the cookies and sealed the lid on with a hand-cranked canning machine. He then drilled holes for ignition wires and for the gas to escape.
“We literally are doing nothing different than people who do home canning,” he says.
When Anasphere began its research for NASA four years ago, it started with hydrogen generators that produced 250 liters of gas. Now, the company is building generators that can produce 1,000 liters of hydrogen. Over the next year and a half, it plans to develop cooling pipes and air filters for even more powerful gas generators. The end goal for the largest HIAD-inflating gas generators is about 70,000 liters, Cheatwood says.
Launching inflatables
As NASA and its contractors continue this work on generators, they might soon have a wealth of test flight data to refer to. The agency has agreements to share HIAD technology with Outpost and with ULA. Each company needs something smaller than the 16- to 20-meter shields NASA is developing for Mars missions. Outpost intends to return smaller payloads to Earth from satellites, such as science experiments or space-manufactured alloys and optical fiber, for which it would need 2- to 3-meter inflatable shields. As for ULA, the company requires heat shields about 10 meters in diameter to recover booster engines from its Vulcan Centaur rockets.
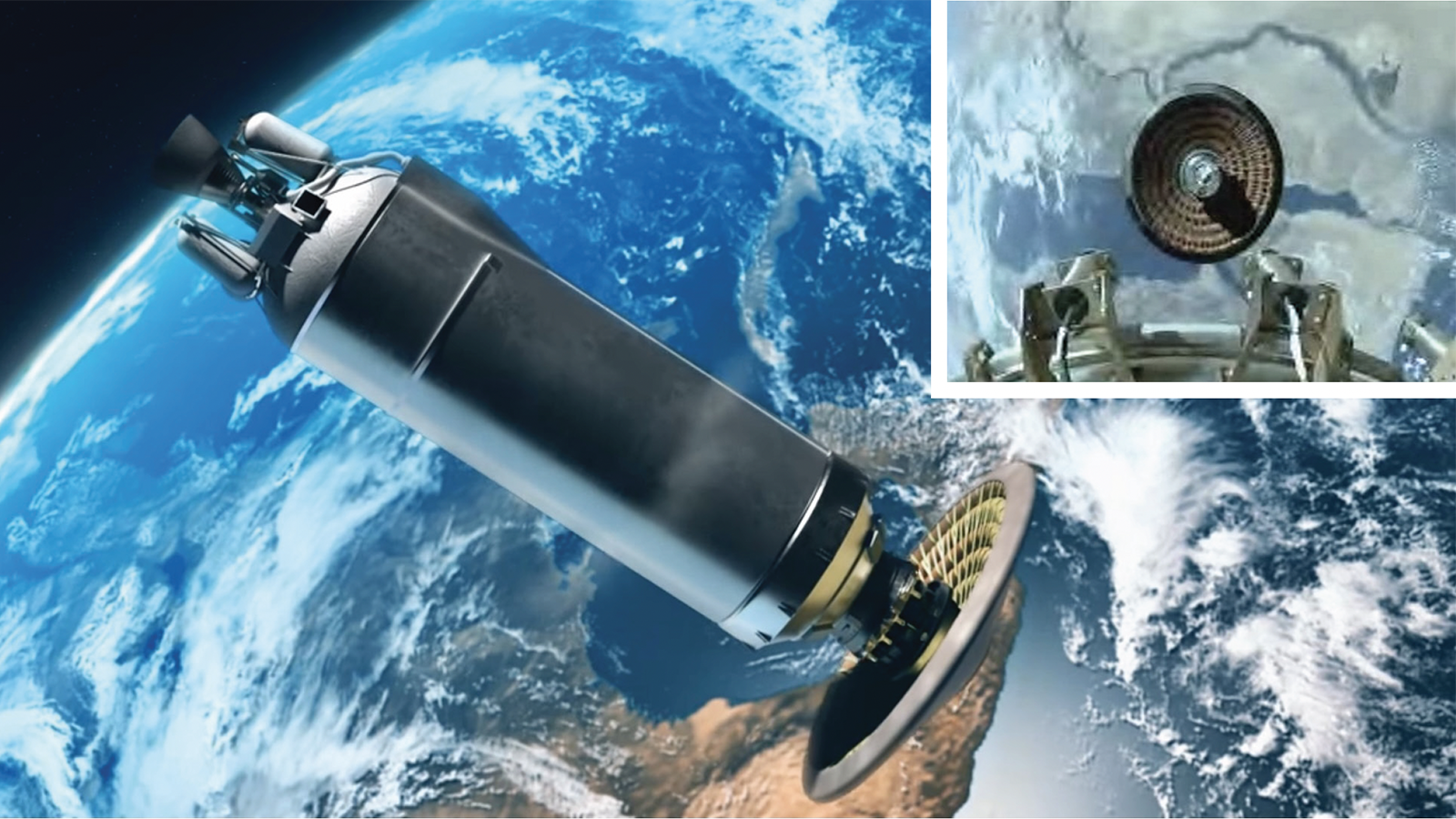
NASA says ULA plans to begin launching its HIADs in about four years, and Outpost in about two years. With each launch, NASA can apply the results to its own HIAD designs, Cheatwood says.
“You can imagine each time they launch one of those, if we can learn things that let us reduce the mass of the inflatable or the mass of the heat shield or the mass of the inflation system, that frees up more mass for payload,” he says. “I imagine their design will evolve over at least the first few flights as we learn, say, ‘Well, you could take out this layer of insulator or get by with one less gas generator.’”

About Keith Button
Keith has written for C4ISR Journal and Hedge Fund Alert, where he broke news of the 2007 Bear Stearns hedge fund blowup that kicked off the global credit crisis. He is based in New York.
Related Posts
Stay Up to Date
Submit your email address to receive the latest industry and Aerospace America news.
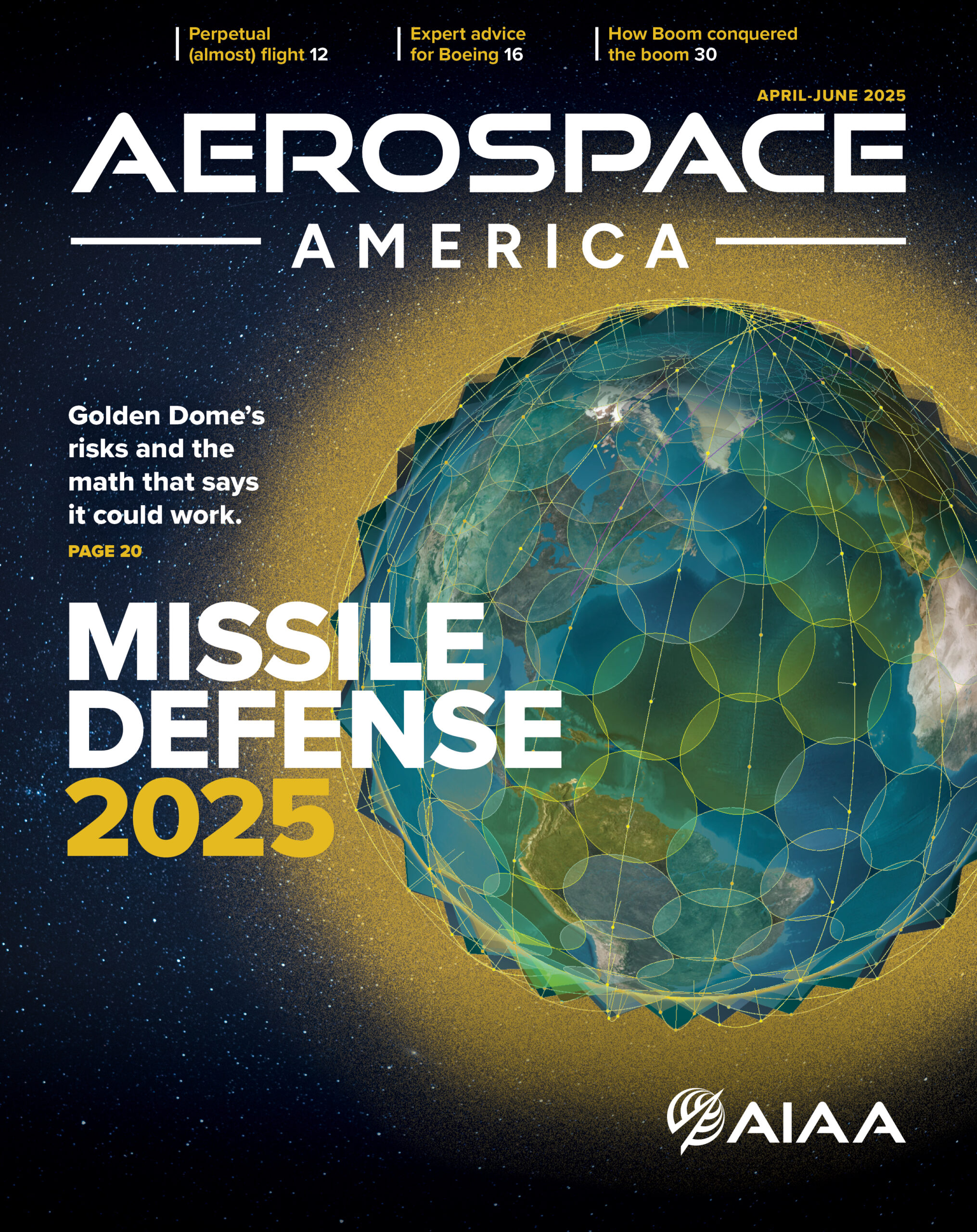