Stay Up to Date
Submit your email address to receive the latest industry and Aerospace America news.
In the tale of the airline industry’s attempts to reduce its environmental impact, hydrogen is either a godsend or an impossible challenge. Paul Eremenko is firmly in the first camp. His 70-person startup Universal Hydrogen has taken its first concrete steps toward creating a hydrogen fuel distribution network that would initially power small aircraft and eventually airliners. The startup’s first products will be carbon fiber capsules that would be trucked to airports where technicians would swap out empty capsules for fresh ones. Plans call for selling the capsules to regional airlines starting in 2025 as part of a Universal Hydrogen kit for converting turboprop planes to hydrogen-electric aircraft. I reached Eremenko via Zoom at his California office to learn why he predicts the rest of the aviation industry will soon become hydrogen believers.
Q: How does one go from spearheading tech development at DARPA and Airbus to creating a hydrogen startup?
A: One develops a very high level of frustration with the fact that the industry is basically ignoring the Paris Agreement. If you look at like the International Civil Aviation Organization forecast for aviation emissions, it goes in the opposite direction of the Paris Agreement. I was the guy in the Airbus C-suite and then in the United Technologies C-suite who was like, “What are we doing about this?” So I’ve looked at this problem of decarbonizing aviation for the better part of the last decade. I’ve worked on battery-powered aircraft, I’ve worked on hybrid-electric aircraft, I’ve worked on biofuels, and if you take the timeline of the Paris Agreement seriously — which I think we should because it’s about as close to a consensus as we have as a species about where we need to go from an admissions perspective to avoid catastrophic climate change — there are only a few technologies that are plausible on the timescale that you need. If you want to decarbonize the sector, it’s not enough to do small airplanes or air taxis; you’ve got to do the single aisle, the Airbus 320s and Boeing 737s. For that class to get to zero emissions, there’s two options: You can go nuclear — probably not desirable from a safety perspective and from other kinds of environmental impact — or you can go hydrogen. And the answer to why that hasn’t happened yet is not because hydrogen airplanes are difficult to build. The first manned hydrogen airplane flew in the ’50s; Pratt and Whitney’s entire West Palm Beach operation was created around a hydrogen engine program in the 1950s. The problem is affordable green hydrogen and getting hydrogen from the point of production to the airplane, the point of consumption. So we founded this company in 2020 when it started to become clear that the cost of green hydrogen was dropping at such a rate that by around 2025, it will be equivalent to the cost of jet fuel on an equivalent energy basis.
Q: What’s prompting this price decrease?
A: The first is volume, which is a bit of a self-fulfilling prophecy: As you increase production, the cost of production goes down drastically. You can make hydrogen a number of different ways, but a lot of them take hydrocarbons and strip out the carbons and you have the hydrogen left, but then you got to do something with the carbon. But then you have carbon emissions, which is the exact opposite of what we’re trying to do here. But you can make hydrogen by splitting water molecules into hydrogen and oxygen using electricity, and then the oxygen you can either release into the atmosphere, or you can use it for medicinal or other applications. That’s green hydrogen, which means no carbon footprint so long as you use renewable electricity. There’s two components to the cost: There’s the cost of the electrolyzer and the cost of the electricity needed to run the electrolytes. The cost of electrolyzer has dropped because we’re in that virtuous cycle of increased production. What reduces cost on the electricity side is the general increase in renewable electricity production. Take wind farms. They’re blowing day and night, generating electricity, but the city or whatever you’re powering is only consuming so much. And there’s no way to store the excess electricity because you can’t build batteries at that scale, so that off-peak electricity is available very, very cheaply and you can literally scavenge and produce hydrogen whenever there is less than peak demand on your power plant or wind farm.
Q: Why is your approach the right one to provide the missing link between fuel producers and operators?
A: If you take the conventional approach of how we move jet fuel today, we do it through pipelines to big airports, or we do it through fleets of tanker trucks and then we have a storage reservoir at the airport. In some rare cases, there’s even on-site refining. You could do all three for hydrogen; the issue is that if you take the scope of even a modest regional airline network, much less the entire commercial air transportation network, a hydrogen infrastructure at every airport becomes a trillion-dollar investment. Then the question is “Who pays?” So if you take the Paris Agreement timeline and emissions trajectory as the constraint, the answer was to make hydrogen compatible with the existing network and with the existing cargo handling equipment that’s at the airports. So we created capsules for gaseous and liquid hydrogen, we ship the capsules in a shipping container, and then at the airport we use the cargo handling equipment that you would use for palletized cargo to move it around and load it directly into the aircraft. There’s no fueling operation, nothing has to change, every airport is hydrogen ready. I like to analogize it to the Nespresso coffee capsule model: You have Nespresso capsules, but somebody has to build the first coffee maker. We couldn’t be a company that just solves infrastructure when there is no hydrogen airplane. So we’re doing hydrogen delivery as a service, and we’re going to build the first coffee maker, which is in our case that conversion kit for regional airplanes. Now, regional is not going to solve the Paris Agreement problem for aviation, but it’s doable in the next couple years. It’s doable within the scope of existing motor technology, existing fuel cell technology, and the airframes frankly are massively overdesigned; they’re relatively easy to modify and they have a fair amount of volume.
Q: Tell me about the different fuel tank designs the company came up with to transport and store both gaseous and liquid hydrogen.
A: With gaseous hydrogen, you get less hydrogen in a given size capsule, but it’s cheaper to produce because compression is less energy intensive than liquefaction. And it’s cheaper to transport because they have an infinite shelf life. The liquid capsules have a shelf life of a couple days, so you have a pretty tight logistics network around them. You can hit about two-thirds of all regional routes with gaseous capsules, and you need liquid for the last third to be able to fulfill the range requirements. In anything smaller than regional, you want to go with gaseous. In anything bigger than regional, you want to go with liquid. Those forms require different capsule materials, but they are interchangeable in the aircraft. The same airplane can take liquid capsules on one route and a gaseous capsule on the next route. The gaseous capsules are made of a woven carbon fiber. It’s a braid — not a composite in the sense that it does not have an epoxy matrix — and then there’s a membrane inside the braid that traps the hydrogen molecules while the braid carries the pressure loads. We get rid of the epoxy to save weight. And then for the liquid capsules, they are today a dual-wall metallic solution with a vacuum insulation layer in between the two walls. We are looking at going to cryogenic composites in the future.
Q: For the conversion kits, you’re taking out a few seats to make room for the fuel pods, but how much additional weight is added by the fuel cells and motors?
A: The wings of regional aircraft are significantly overdesigned, so they’re able to carry the weight of the fuel cell and electric motors — which weigh somewhat more than the conventional turboprop engines — without modifications. We also stay within the design max takeoff weight and balance envelope of the existing aircraft to simplify the certification process. Then in addition to the conversion kit for regional airplanes, we’ll provide fuel as a service for other sectors — because again, the next big step in the decarbonization journey for the sector is going to have to be the single aisle. We have a good 10 years before the first hydrogen single aisle is likely to be in service. And our focus for them is fuel logistics and fuel services.
Q: Is Airbus’ 2035 target for its first hydrogen aircraft realistic?
A: It’s totally realistic; the Soviets already did this once in the 1980s. There are plenty of engineering challenges — I’m not saying that it’s easy — but nothing has to be fundamentally invented. Both Airbus and Boeing are going to do a new single-aisle design anyway because the 737 is old and the 737 MAX debacle shows that there’s not going to be another derivative. And Airbus will have to do a clean-sheet airplane as well; the 320s are a little bit newer, but it’s still a fairly old family of airplanes. So this new clean-sheet airplane will probably enter service in the mid-2030s, which means a program launch decision in the late 2020s — let’s say 2027, 2028. Our goal is to be in service with regional aircraft by 2025 so that we have passenger butts in seats flying on real scheduled commercial flights that are truly zero-emissions. And I think once that happens, the fundamental dialogue around the single aisle is going to change. The tenor of that conversation is going to be such that passengers are going to demand it because they’re going to say, “Well, I can fly in a hydrogen airplane here. How come you guys are building a brand new airplane that burns dinosaurs?” And maybe those airliners will be using a sustainable aviation fuel, but it’s still an offset scheme; you’re still burning a hydrocarbon at 35,000 feet. Passengers are going to say, “What are you doing?” Airlines are going to say, “Why are you doing less?” Governments are going to say, “Don’t do that.” It will be an impossible decision for Boeing and Airbus to do anything other than launch a hydrogen single-aisle program in the late 2020s. The environment is going to change much more quickly than either of those companies anticipates today.
Q: Why did you decide to base Universal Hydrogen in the U.S., where the federal government and Boeing are much more open to tax credits and the like for SAFs, versus Europe, which is all in on hydrogen from a policy perspective?
A: Ultimately, this is a global problem. The aviation sector is a global sector, and it’s going to have to be a global solution. We based ourselves in what we believe to be the two top aviation talent pools: One is Los Angeles; then we have our engineering center in Toulouse. Going back to World War II and in the ’30s, all of the U.S. airplane production was in southern California, and Toulouse was the city in France that was farthest from reach of German bombers, which is why all airplane production got moved to Toulouse and is still there. They’re the two talent hotspots, and so we want to be in both.
Q: If this sea change in public opinions occurs as you predict in the late 2020s, how does the industry ensure there’s enough green hydrogen to meet the demand?
A: You hit the nail on the head with public policy and government incentives. Today, green hydrogen costs more than jet fuel on an equivalent energy basis. It’s on a steep decrease, but for sure having cap and trade schemes or carbon taxes or hydrogen subsidies and other forms of economic incentives will help ramp up production. For regional, we think that the green hydrogen production capacity is going to be there, but that sector is relatively small. For single aisle it’ll be a challenge; a very significant ramp has to happen in the late ’20s and early ’30s. For sure, government loans and government investment are very, very helpful. The other part of it is the contextualization of SAFs, biofuels and synthetic fuels. SAFs are great if you have no other choice, meaning that you want a drop-in replacement that works today on existing airplanes and existing engines. But biofuels are just not scalable. The biomass areas that you need to produce the feedstock for the fuels are immense, and if you’re starting to harvest those amounts of biomass, you will have other environmental catastrophes. That’s why the most fashionable topic on SAFs today is synthetic fuels. It’s still a hydrocarbon: To make it you take green hydrogen made by electrolysis and then you tack on carbon atoms, and you make your hydrocarbon. Then you take that hydrocarbon to 35,000 feet and you burn it, which is exactly the thing that you’re trying to compensate for. But the reason
that’s more appealing to some people than hydrogen is because a hydrogen-powered aircraft means you got to change the engine, you got to change the airplane, you got to have a distribution network. All these things sound really hard, and to me that’s just laziness on the part of the aviation industry. I didn’t become an aerospace engineer to be like “Oh, it’s too hard. I’m not going to be able to solve that problem; it’s a fuels problem.”
Q: Right, it seems like something like the blended-wing body that’s among Airbus’ hydrogen concepts should be an engineer’s dream.
A: I don’t think that the blended wing is going to happen for the single aisle, but it may need to happen for the next widebody, which I think would be in the 2040s as the replacement for the Boeing 787 and Airbus 350. All the data sets that Boeing and Airbus have are around the tube-and-wing configuration, so if you’re going to do entry into service by 2035, I don’t think anybody is realistically going to do a blended-wing body on that timescale. But nor do you have to. You can do a hydrogen single aisle with a very modest increase in length of the tube: about 9 meters of length extension on a standard narrow-body to store enough hydrogen for the Heathrow to JFK route transatlantic, which is the farthest you would ever fly now in a narrowbody. And if you’re just trying to do LAX to JFK, it’s about 5 meters lengthening of the fuselage to store enough hydrogen. These not huge design changes; this doesn’t break anything. This is why I can confidently say that if the tenor of the discourse around the next-generation narrowbody changes, the technology’s there; Boeing and Airbus and the Pratt and Whitneys and Rolls-Royces of the world are going to absolutely be able to do this airplane. The reluctance is more around an incrementalism mindset that is pervasive in this industry. We founded Universal Hydrogen to be freed from that tyranny of incrementalism and say, “Look, we’re going to show the way, and we’re going to catalyze it and we’re going to make it so that doing anything else is just impossible.” That’s the goal.
Q: Would that about face be enough to get the industry back on track to meet its portion of the Paris Climate Agreement and the net-zero by 2050 goal?
A: Remember, the buzzword “net-zero” means that you’re offsetting. I think the industry can actually get close to true zero by 2050, but it will depend on the speed with which these airplanes sell. Roughly speaking, if hydrogen regional is available in the mid-2020s, then it’ll take five to seven, maybe 10 years, for the entire regional market to convert. On the single aisle, there’s a question of whether it’s just one of Boeing and Airbus or both. The very interesting scenario would be if one of them does a hydrogen single aisle and the other doesn’t. But my guess — and this has always been true in the duopoly between the two — is that it’s tit for tat, and as soon as there’s rumors that one is moving toward hydrogen, the other one will. So you start flying them around, say, 2035, it’s going to take through the mid- to late 2040s for the entire single-aisle fleet to get replaced. The good news is that the single aisle accounts for about 60% of all aviation emissions, so between single aisle and regional you’ve mitigated two-thirds of your emissions, and then the widebody is the remaining. I refuse to believe the aviation industry can’t achieve this because if we can’t, people will stop flying. People will switch to trains or video or whatever. I think a lot of people go into aerospace because they think it’s cool, but as I have grown up, I also recognize that one of the important facets of our industry is that we are one of the most powerful forces for globalization and cultural exchange and trade. It would be a real shame if aviation starts to decline because it’s too carbon intensive of an industry. Because if aviation goes away, a lot of the positive forces of globalization and cultural exchange will go away.

About cat hofacker
As acting editor-in-chief, Cat guides our coverage, keeps production of the print magazine on schedule and edits all articles. She became associate editor in 2021 after two years as our staff reporter. Cat joined us in 2019 after covering the 2018 congressional midterm elections as an intern for USA Today.
Related Posts
Stay Up to Date
Submit your email address to receive the latest industry and Aerospace America news.
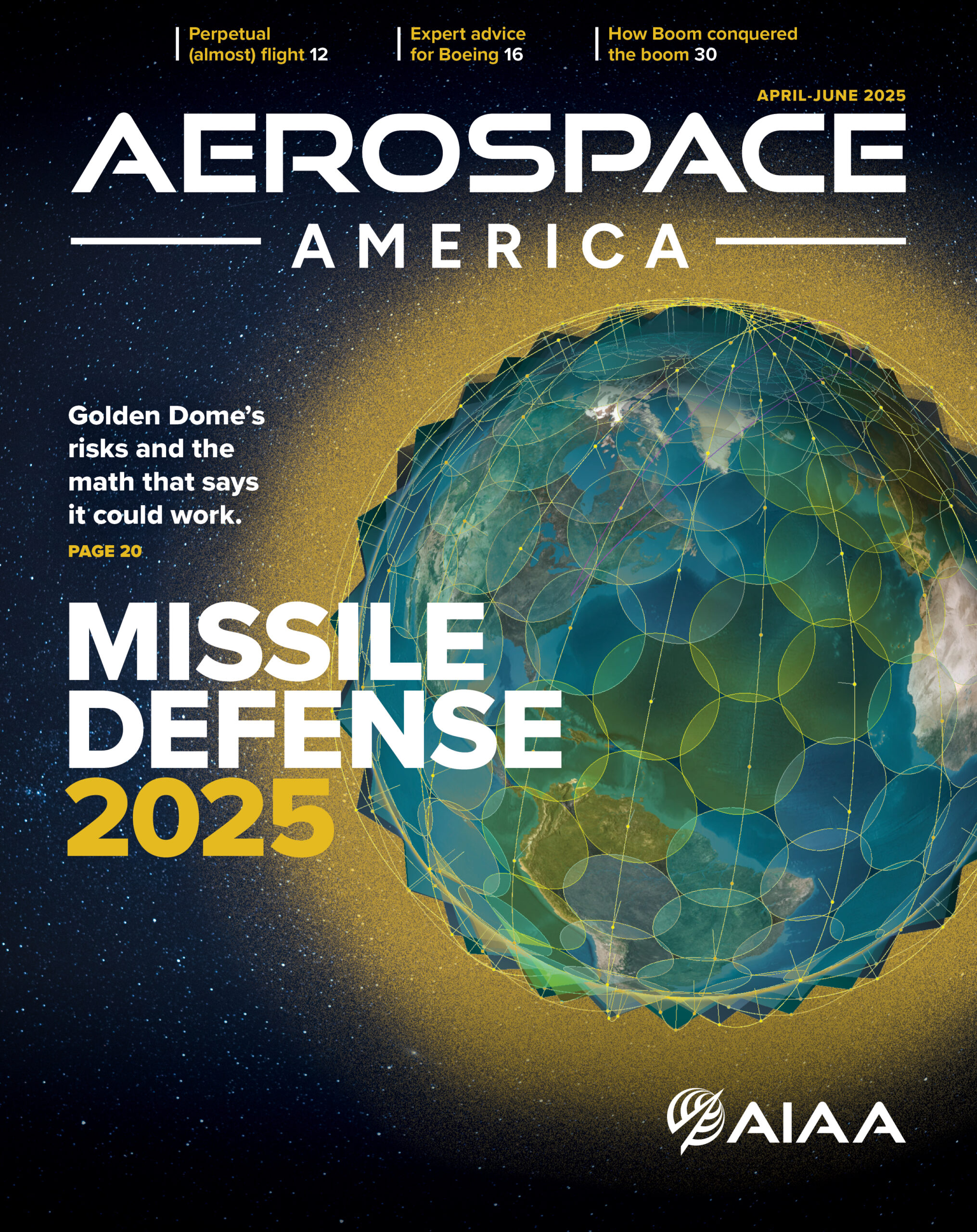
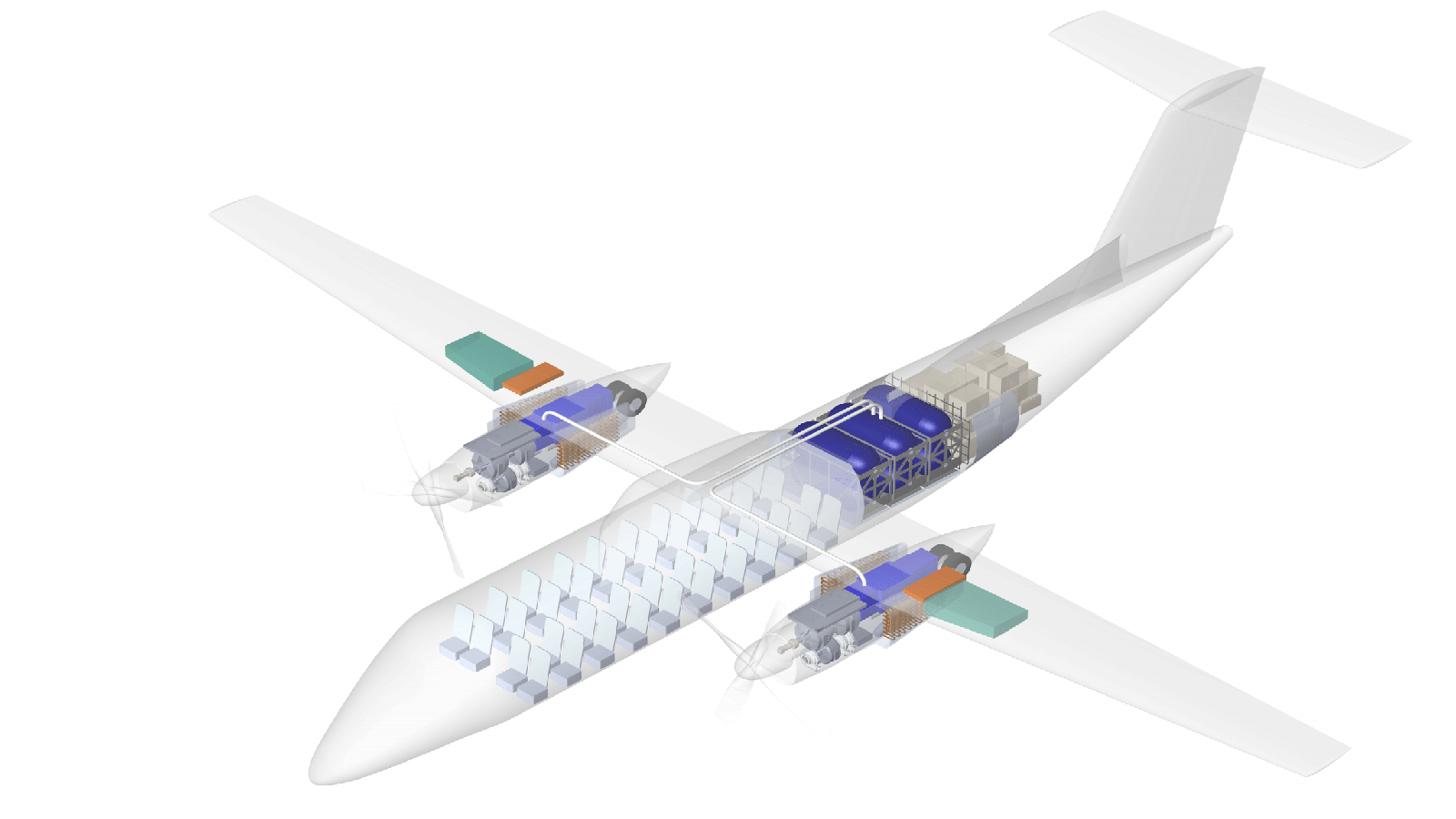