Stay Up to Date
Submit your email address to receive the latest industry and Aerospace America news.
DARPA’s plans for a demonstrator UAS for the Navy
The Navy’s catapult-launched ScanEagle drones can see beyond the horizon, but they’re too small to carry Hellfire missiles or guided bombs. The unmanned Fire Scout helicopters need only a small deck for takeoffs and landings, but generating lift solely with rotors means burning fuel faster than a fixed-wing plane would.
For the Navy, the missing piece of the unmanned puzzle is a MALE, or medium-altitude long-endurance unmanned aircraft, that could fly from its frigates and destroyers. DARPA and the Office of Naval Research set out in 2013 to find a possible design for such a craft. They put DARPA in charge of development, divided funding responsibility equally and named the program the Tactically Exploited Reconnaissance Node, although they now prefer to call the program simply Tern.
In 2014, they settled on a concept proposed by Northrop Grumman, the Fire Scout builder, for a flying-wing aircraft that would be stowed in pairs on their tails inside the hangar of a destroyer or frigate.
Concept of operations
As “tail-sitters,” the aircraft would take off vertically powered by counter-rotating rotors on their noses and then transition to fixed-wing flight. If the Navy decides to buy them, two Tern airframes would form a single system that would maintain continuous surveillance for 10 days. When one aircraft needed to land, the other would relieve it on station. Tern needs to fly at about 15,000 feet and orbit 600 nautical miles from the ship while carrying 500 pounds [227 kilograms] of sensors, data links for communication and under-wing weapons. The aircraft would keep watch for missiles that might be launched from many hundreds of nautical miles away.
That’s how things could work if a series of at-sea flight tests goes well in 2018. Northrop Grumman is building two demonstration versions of Tern and completing development of the software that will manage their flights. Developers knew from the start they were entering “uncharted territory,” says DARPA’s Brad Tousley. “No one has flown a large unmanned tail-sitter before,” he says in an article on the agency’s website.
The two demonstrators must fit in the same size ship hangar that today carries a single MH-60 helicopter. In the test flights, Tern must take off from and return autonomously to the helicopter deck of a small ship, even in rough seas.
“This is revolutionary, we had never put such a level of performance on a small ship. That made it a hard problem, a DARPA problem,” says Bob August, who manages Tern for Northrop Grumman.
Narrowing the field
DARPA initially looked at several possible configurations, including pure fixed-wing aircraft. This approach was ruled out early on because the fixed-wing designs were too large, and the required accessory equipment to launch and recover them would have been complex and substantial. “Aircraft size and geometry were strongly influenced by the size of existing MH-60 hangars,” explains DARPA Tern Manager Graham Drozeski. DARPA converted the fixed-wing idea into another program, SideArm, a self-contained, portable apparatus to launch and retrieve other unmanned aircraft from trucks, ships and fixed bases.
The space restrictions urged a rotorcraft, but long endurance urged the efficiency of fixed-wing flight. DARPA decided it needed an aircraft that could transition from vertical flight to fixed wing and back. In principle, tilt-rotor, tilt-wing, vectored thrust, tail-sitting and ducted fan concepts might meet this requirement.
Northrop Grumman’s tail-sitter approach seemed the most practical. “The tail-sitter was simple in mechanics and system integration, and simple is generally good,” August says. Two Terns, with wings folded, could fit in the small hangar.
Flying a tail-sitter
With the basic design settled, challenges in control, propulsion and software remained. Tail-sitting aircraft had been developed and abandoned before. The Ryan X-13 Vertijet flown by the U.S. Air Force in the 1950s illustrated the inability of a pilot to see well during landing or takeoff, something that’s not a problem for the unmanned Tern. Vertijet was of course powered by a jet engine, unlike the rotor-propelled Tern.
What Tern does require are precise controls to take off and land on a small ship in the tumult of the sea. “The dynamic interface of flight deck and air wakes behind ships in elevated sea states drove configuration and control designs,” Drozeski says. Specifically, Tern must take off and land even in sea state 3 and ideally up to sea state 5, which means waves of up to 4 meters.
Northrop Grumman settled on two coaxial rotors, one rotating clockwise, the other counter-clockwise. This way, the demonstrators won’t need a tail rotor to counter torque by generating a yawing moment. The concept takes advantage of the best attributes of rotors and propellers. Like all rotors, Tern’s are hinged at their roots. They will change angles collectively, like solid propellers, when necessary for maximum vertical lift, and individually to generate the exact pitch and roll needed to keep the aircraft stable during vertical flight and to change angles of attack in the transition to horizontal flight. Tern moves steadily through these angles rather than spending time at different angles, as the V-22 Osprey tilt-rotor does. Once in horizontal cruise flight, the rotors change angles only collectively, like propellers, so air will flow over the wing and flight-control surfaces, which now steer the plane.
Testing
Northrop Grumman engineers spent many hours running computational fluid dynamics models to solve the aerodynamic problem and design the rotors, the wing and power requirements for the demonstrators. A special concern was the need to design rotors that could operate in horizontal and vertical modes. Designers of the V-22 Osprey achieved that, but no one has managed it with any previous tail-sitters, Drozeski says.
The demonstrators must generate a thrust-to-weight ratio greater than 1 in hover and substantially less than 1 in cruise. To gain long endurance, cruise efficiency becomes much more important than speed. This efficiency is in turn a function of airframe efficiency — primarily lift to drag engine efficiency — at low throttle and fuel weight.
DARPA and Northrop Grumman selected carbon fiber reinforced polymer for the airframes being made by the company’s subsidiary Scaled Composites. August says this choice of material was driven mostly by the need to rapidly prototype the demonstrators.
For propulsion, Northrop Grumman chose to modify the General Electric T700 turboshaft engine, the same kind of engine that powers the Navy’s MH-60 Seahawk helicopters. August says T700 had the right power and the Navy knew the engine well, but that some changes had to be made for the Tern application.
The T700 is positioned horizontally when supplying power to the vertical shaft of the Seahawk, but on Tern it will be tilted vertically during takeoff and landing. GE had to modify the engine to ensure that both engine and gearbox would be lubricated in this vertical position.
Turboshaft engines like the T700 also have gears and a gearbox between engines and power shaft. New gears and a new gearbox had to be designed and built for Tern. Northrop Grumman needed to devise gearing to give the T700 enough power at full throttle for vertical climb, and also a throttle-back mode that would achieve efficiency for cruise. And it had to design a new gearbox that would fit into demonstrators’ wings.
For the autonomous control, Northrop Grumman is adapting autonomy software from the firm’s Fire Scouts. The autonomy is key, because the Navy won’t add crew for the Tern beyond the number required to maintain and operate two Seahawks aboard. If operational versions of Tern are built, crew members would move the planes in and out of the ship’s hangar and then an operator would initiate the launch sequence and give the aircraft its mission plan from a control station either onboard the ship or remotely. The aircraft would fly the mission and autonomously return and land on the ship, unless the operator decides to override this autonomous operation for some reason.
The Fire Scout experience and computer modeling were helpful in developing the flight management software for the aircraft, but Northrop Grumman also needed wind-tunnel tests to document how the aircraft will behave in flight.
So in 2016 DARPA tested scale models of Tern in the National Full-scale Aerodynamic Complex at NASA’s Ames Research Center in California. The agency will do more wind-tunnel tests of models in mid-2017 to generate data describing how the aircraft reacts to different airflows. “We need to see the lift and drag at different speeds, attitudes and levels of thrust,” Drozeski explains.
Meanwhile, Northrop Grumman this year will put the integrated propulsion system, including the T700-variant engine, through its paces in ground tests at full and lesser power and at different tilt angles. These tests will be aimed at validating engine and gearbox performance at key operating angles.
These wind tunnel and engine tests should set up the demonstrators for the planned series of flight tests in 2018 in which the demonstrators will take off, execute their mission and return to a ship.
Drozeski expects any production version will look a lot like the demonstrators. But the Navy will make the final tradeoffs between cost and performance on, for example, the materials used for the airframe.
Factoid
In the 1950s, the Air Force tested the X-13 Vertijet, a vertical takeoff and landing jet.According to the Smithsonian National Air and Space Museum, the U.S. was interested in developing an aircraft that could be based at a small operating site rather than a large base that was more vulnerable to missiles and nuclear weapons.
“The tail-sitter was simple in mechanics and system integration, and simple is generally good.”
Bob August, Tern manager for Northrop Grumman

About cat hofacker
As acting editor-in-chief, Cat guides our coverage, keeps production of the print magazine on schedule and edits all articles. She became associate editor in 2021 after two years as our staff reporter. Cat joined us in 2019 after covering the 2018 congressional midterm elections as an intern for USA Today.
Related Posts
Stay Up to Date
Submit your email address to receive the latest industry and Aerospace America news.
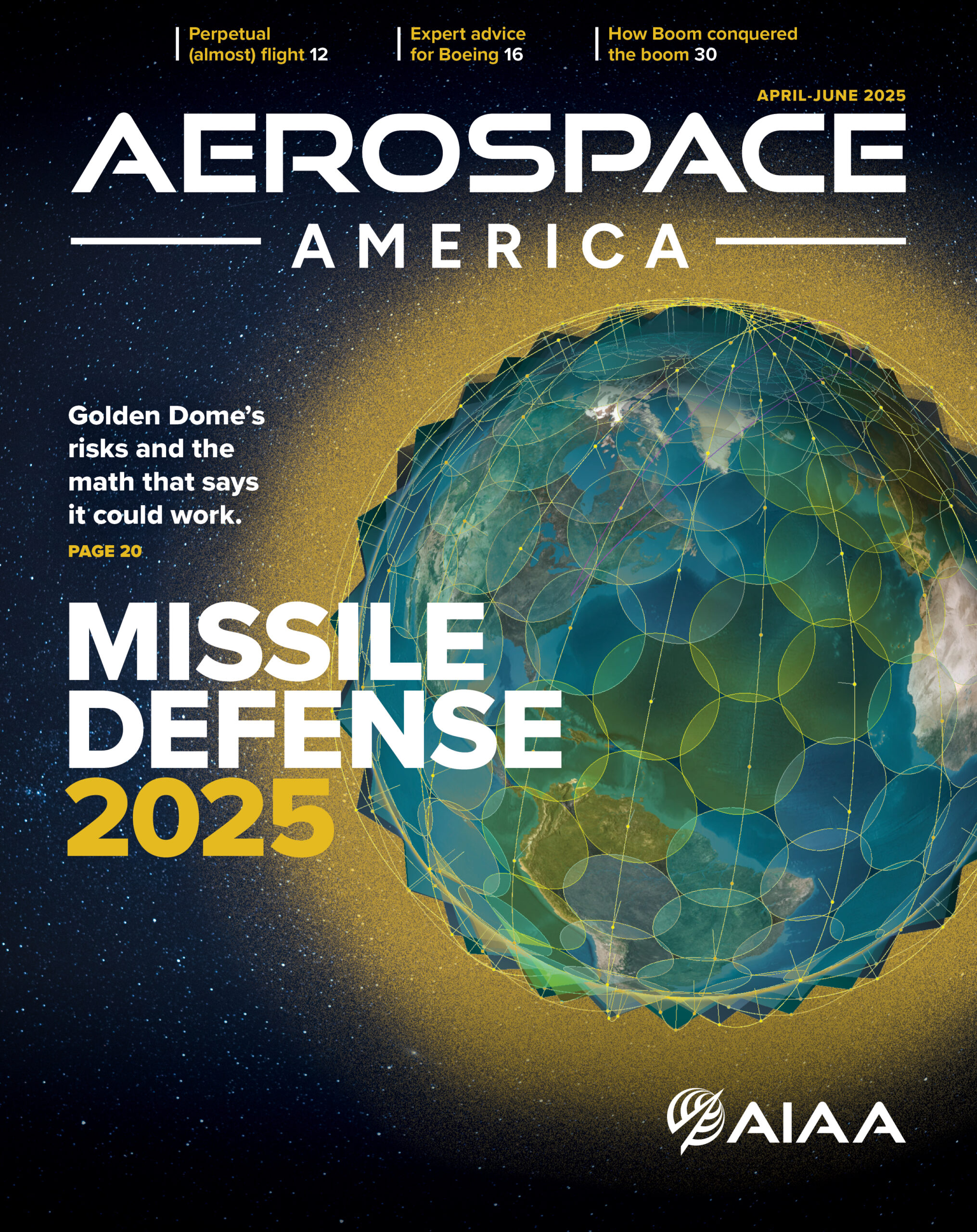
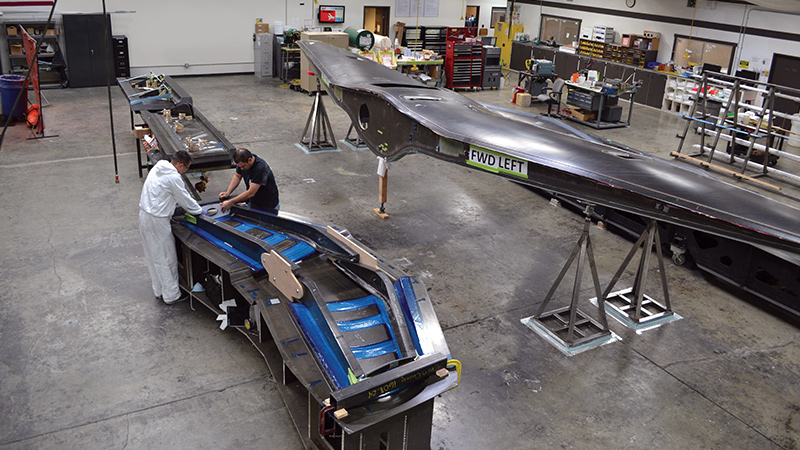
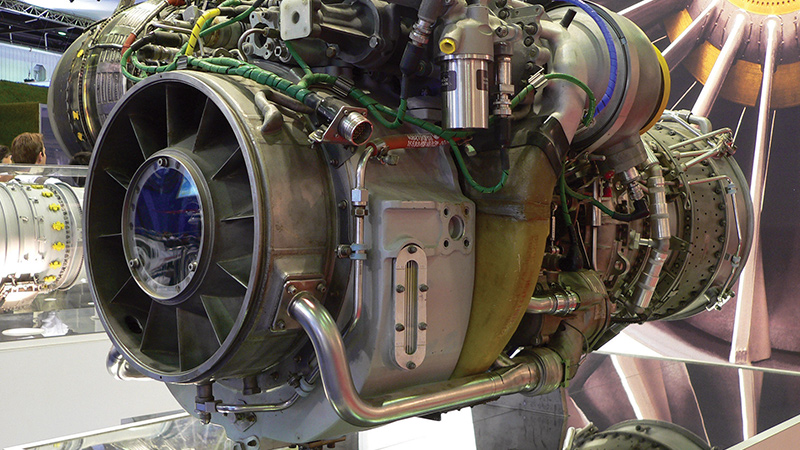