Stay Up to Date
Submit your email address to receive the latest industry and Aerospace America news.
James Kropp, 27, programming engineer, Norsk Titanium
James Kropp nurtured his love for machines helping his father work on cars and other projects around their home. Those projects included woodworking, where he learned the principles of design and fabrication. More hands-on experience during vocational courses in his Michigan high school sparked a passion for the science of welding and other materials joining processes. He earned a Bachelor of Science in welding engineering technology from Ferris State University in Big Rapids, Michigan. Kropp now works in Plattsburgh, New York, for Norsk Titanium, a Norwegian additive manufacturing company with 150 employees. Norsk produces the first FAA-certified additively manufactured structural titanium parts for a commercial aircraft, Boeing’s 787 Dreamliner, through its patented Rapid Plasma Deposition process, which builds parts with layers of melted titanium wires.
How did you become an engineer?
My first encounter with the aerospace industry was through an internship at Woodward Fuel Systems Technologies. I developed weld procedures for F135 engine fuel system components. Next, I worked for United Launch Alliance as a welding engineer, supporting production components for Atlas 5, Delta 2 and Delta 4, and then as a test/propulsion system design engineer, developing and qualifying components for ULA’s Vulcan rocket booster. Seeing the potential for the implementation of additive manufacturing during hardware development inspired me to pursue the advancement of the additive technology, which led me to Norsk Titanium. I work alongside Norsk’s Part Development teams to establish deposition techniques and process parameters for additively manufacturing titanium components using the Rapid Plasma Deposition process. I work to increase process efficiency and capability, while maintaining customer requirements and product integrity. It is exciting to work with a relatively new process in such an innovative field. There are few areas in the aerospace industry where you can go to work and push the limits of what people believe can be done, on a daily basis. Additive manufacturing is one of them.
Imagine the world in 2050. What do you think will be happening in aviation?
We will continue to see a push for increased efficiency while maintaining or reducing manufacturing cost. To achieve these goals, I think we will see a shift from traditional manufacturing techniques to lower cost and more efficient methods such as additive manufacturing. This change is starting, but there is still an enormous effort required to reach full industrialization. Within the next five years, industry standards will be established and applied, leading the way for industrial implementation. Additionally, with the significant increase in composite structures utilization, there will be a need to develop new methods for the mating of composite and metal structures. There are substantial opportunities for the development of a hybrid metal/composite additive process on the industrial scale. Creating metal composite structures as a single piece instead of a mechanical assembly will significantly improve aircraft performance by 2050, leading to an increase in societal growth through faster and more economical air travel.

About Debra Werner
A longtime contributor to Aerospace America, Debra is also a correspondent for Space News on the West Coast of the United States.
Related Posts
Stay Up to Date
Submit your email address to receive the latest industry and Aerospace America news.
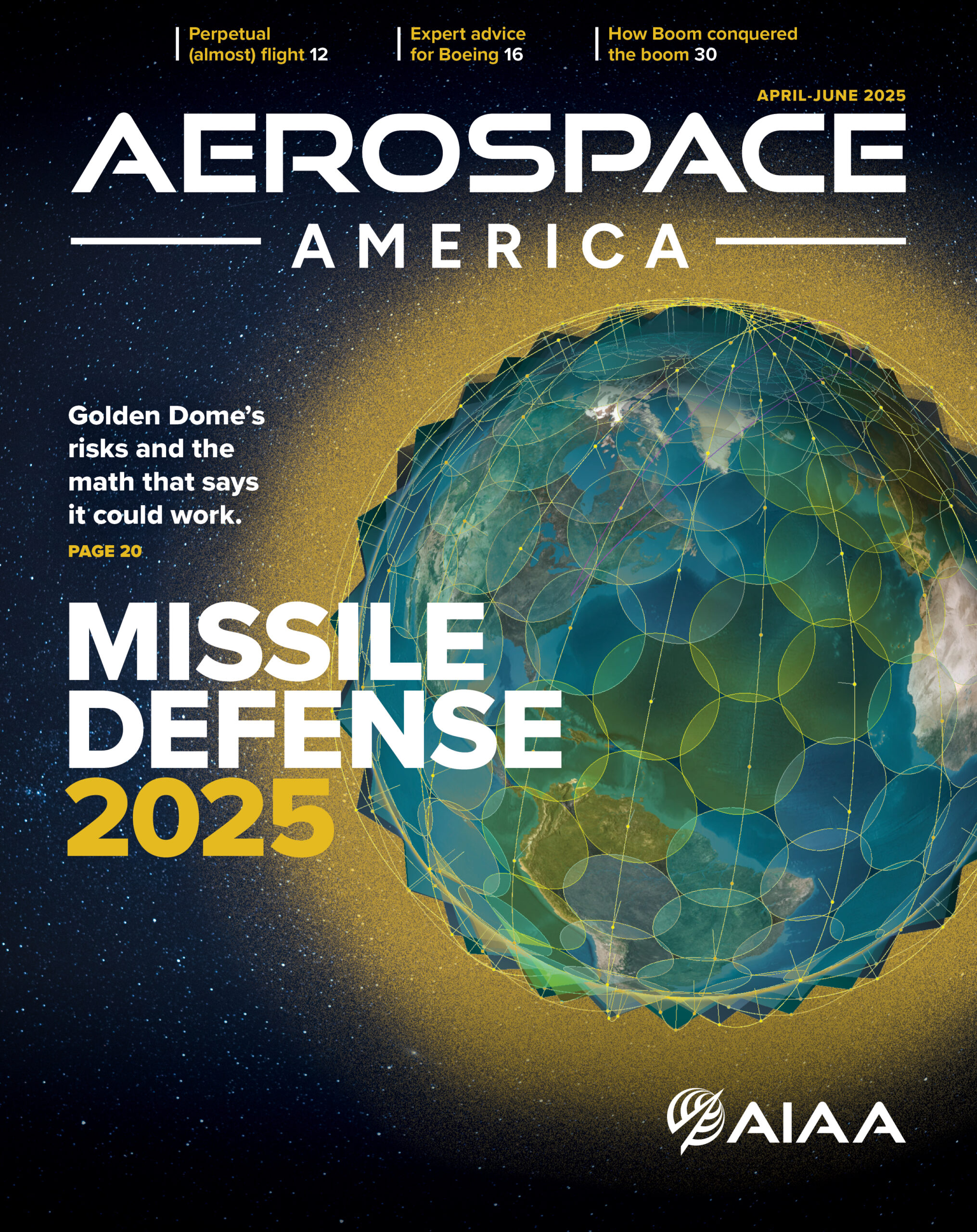