Stay Up to Date
Submit your email address to receive the latest industry and Aerospace America news.
On the face of it, converting a seaplane built in 1957 to electric operation might seem like a strange decision. After all, why not electrify a modern, lighter and probably longer-range seaplane?
The reason, say executives of Harbour Air, a Canadian airline whose fleet includes 14 six-seat de Havilland Beaver seaplanes, comes down to familiarity for pilots and maintainers — and even regulators.
“Everybody knows how [a Beaver] handles and exactly what it flies like. So by changing just the motor, we’ve kept the number of changes down to a minimum,” says Shawn Braiden, Harbour Air’s vice president of aircraft maintenance.
In theory, that should eventually smooth the way for certification by Transport Canada and FAA as development proceeds on a certification version now being built.
“We’ve got to where we think we want to go, but the regulators have not yet agreed to any path. So we’re working with them to figure out how we’re going to get there,” says Harbour Air’s Erika Holtz, project manager and lead engineer for electrification.
The project began in 2019 when the company set a goal of going fully electric, eschewing the hybrid-electric approaches adopted by other companies retrofitting small or regional aircraft. Harbour Air first flew its version 1.0 ePlane, a 1957 Beaver equipped with lithium-ion batteries, that December. The aircraft was transformed under a joint project with aviation motor maker magniX of Washington and battery maker Electric Power Systems of Utah. This involved swapping out the Pratt and Whitney Wasp piston engine for magniX’s 560-kilowatt magni500 motor, plus the same lithium-ion battery packs that EP Systems made for NASA’s X-57 experimental electric aircraft.
Braiden says Harbour Air has learned much from this experimental plane’s 55 test flights, including one on Aug. 17 that mimicked a 24-minute, 70-kilometer passenger trip. With version 2.0, the 1956 model now in the hangar, they have some ideas that could increase range and payload.
Flight tests showed the 560-kilowatt motor was overkill, so they have dropped down to a 350-kilowatt magniX model. And instead of using the X-57 battery packs, the company plans to test a lighter design from H55 of Switzerland, co-founded by Solar Impulse 2 pilot Andre Borschberg. The NASA design was “awfully heavy” because of the containment barriers installed to prevent thermal runaway from cell to cell, Braiden says. H55 relies instead on monitoring technology at each cell to try to prevent thermal runaway, an approach inspired by the overheating Borschberg and his co-pilot experienced during their 2016 around-the-world flight.
Holtz and Braiden say investigating the heating and cooling of the batteries in flight and how the temperatures reached in the air and the weather affects their recharge times, will be among the major parameters they investigate with ePlane 2.0. It may be, they say, that a ground-based cooling system could be hooked up to the batteries post-flight so they can be recharged all the quicker.

About Paul Marks
Paul is a London journalist focused on technology, cybersecurity, aviation and spaceflight. A regular contributor to the BBC, New Scientist and The Economist, his current interests include electric aviation and innovation in new space.
Related Posts
Stay Up to Date
Submit your email address to receive the latest industry and Aerospace America news.
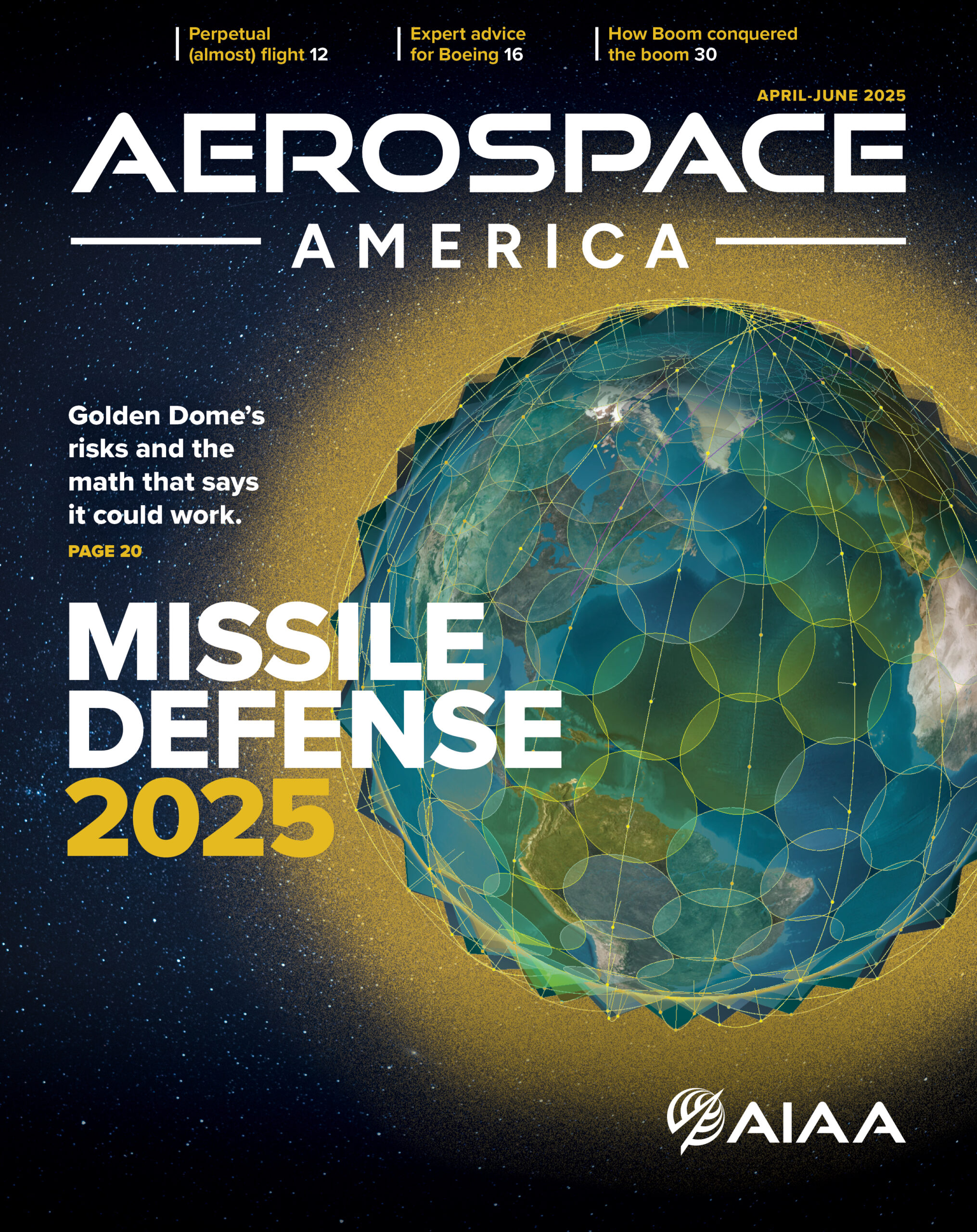