Stay Up to Date
Submit your email address to receive the latest industry and Aerospace America news.
It’s one thing to manufacture a few experimental hypersonic missiles. It’s quite another to manufacture hundreds or more production versions. Automation has to come into play if it’s to be done affordably. Keith Button tells the story of a company that figured out how to apply thermal protection material by robot.
How do you get a robot to precisely spray a gloppy, oatmeal-like coating onto a part for a hypersonic missile before the mixture hardens into a concrete-like substance?
That was the problem facing engineers at Alabama-based robotics developer Aerobotix four years ago. Lockheed Martin, one of the company’s long-standing customers, was relying on workers toting high-
pressure spray guns to apply the material onto test versions of its hypersonic missiles. Lockheed Martin asked Aerobotix to automate the process, so it would be ready should a production order for hypersonic missiles come down from one of the military services. Then as now, the United States was anxious to research, develop and possibly field such weapons in its competition against China and Russia.
Lockheed Martin is but one example of the desire for automation. “The U.S. is right in the middle of that process of handing over things that have been done manually,” says Iain Boyd, director of the Center for National Security Initiatives at the University of Colorado Boulder.
So far, contractors to the U.S. military services have focused on testing and developing the missiles.
“It’s eight or 16 or 32; it’s tens,” Boyd says. “It’s a big step to go from there to thinking about manufacturing hundreds or thousands of these things.”
The work by Aerobotix illustrates the kinds of challenges that manufacturers are facing and the creative innovations that engineers must make to meet manufacturability goals.
The scope of the automation challenge was obvious from the start of the project in 2018. “I thought it was going to be quite difficult,” concedes Mark Breloff of Minteq International, the Pennsylvania company that makes the gloppy but essential coating. “It comes out in mixed consistencies and therefore doesn’t land very smoothly.”
Conventional wisdom said that only a human would have the finesse to evenly apply the coating and know when to pause the spraying because the nozzle was starting to clog. This material was unlike those that Aerobotix robots had applied to F-22s, F/A-18s and F-35s: It contained large particles suspended in the liquid, the material was known to clump in humid conditions and it had to be heated to lower its viscosity. Plus, it had to be mixed up from two components, a catalyst and a resin, for immediate spraying into a plume shaped like a semicircle hand fan. The application had to be correct for the coating to perform its crucial role of ablating, or wearing down, to carry heat from the outer surfaces of a missile slicing through the air at speeds of Mach 5 or greater.
At Aerobotix, step one for Keith Pfeifer, the engineer in charge of the project, was to travel with his team of 15 engineers and technicians to Wisconsin to watch a worker with Quality Paint & Coatings apply the Minteq coating for Lockheed Martin. Wearing a full hazmat suit, the worker held a pressurized spray gun attached to a 9-meter hose filled with the catalyst-
resin mixture. As he sprayed, he carefully watched the material begin to cover the nose cone of a prototype missile. He would slow his pace now and then to give the mixture time to heat up, and pause when he saw buildup on the nozzle tip.
“The tricky part that we all saw was the decisions the operator was having to make based on how the material spread, or what he was seeing,” Pfeifer says. “In real time, he’s able to make a decision like: ‘Oh, the plume doesn’t look right; I need to do this to clean my gun.’”
When the spray gun is functioning properly, its spray plume should look like a triangle from the side; a lopsided plume means that the coating application will be uneven.
The plan
After returning from Wisconsin, Pfeifer’s team members sat down to plan their approach. They were familiar with an off-the-shelf manufacturing robot made by Fanuc, a robotics company in Japan, that was popular as a spot welder. Aerobotix had installed at least 100 Fanuc robots for painting or sanding work for various customers. So they decided to adapt one of the armlike machines to mimic the Quality Paints setup.
At the end of the robot’s arm, they bolted on a high-pressure spray gun like the one the worker in Wisconsin wielded. But unlike in Wisconsin, they decided to keep the catalyst and resin separate for as long as possible. This would make the mixture less prone to curing too soon. So they strung two separate stainless steel braided hoses — strong enough to withstand high pressures — over the arm and joints of the robot. The resin and catalyst would flow in separate hoses and meet in a single hose a short distance from the gun.
Another crucial difference: They knew that the robot, unlike a human, wouldn’t be capable of watching the spray pattern and adjusting in real time. They would need to find a different way. Inspiration came from the pressure sensors that in a more straightforward robot sprayer would alert the device’s operating software of any irregularities in the flow of paint. On a typical robot spray system, they would install a pressure sensor at the pot — where the material to be sprayed is mixed — and a pressure sensor in the line after a pump pushes the material out of the pot toward the spray gun.
“We needed to know more than ‘Hey, the pump is running.’ We needed to know exactly how fast it was running and how much material was exiting that pump,” Pfeifer says.
For example, if one of the pumps was pushing too much of its component into the coating mixture, then the ratio would be unbalanced and the coating would cure too quickly or not fast enough. So the team installed pressure sensors at the spray gun and in the two pots that each held a component of the coating. They also installed thermocouples to measure the temperature of both components after they were heated and at the spray gun. If the team could find the right temperature and pressure at which to spray the coating, then they could program the robot to maintain those levels and adjust accordingly.
After watching the human operator, they also realized that every delivery of the coating components from Minteq needed to have the same consistency before it was loaded into the pots, with little or no variations in viscosity. The robot wouldn’t see changes in viscosity due to variations from delivery to delivery, and it wouldn’t be able to adjust its approach like a human could. So they spoke with Minteq and were assured they would receive consistent batches.
Test runs
Once the team had set up the robot with high-pressure spraying equipment similar to what the human operator employed, they pumped the coating material through the gun without an air cap — the component that adds air to the spray and shapes the plume — just to determine the right nozzle size at which the material could flow through without having to exert extreme pressure, Pfeifer says. Then they added the air cap and started spraying samples on flat panels of aluminum.
They were searching for the right combination of conditions that would produce a perfectly shaped layer: an extremely flattened bell curve, when seen in a cutaway view from the side. It would be thicker in the middle and tapering off at the edges. That meant accounting for the temperature and pressure of the spray material, the air applied in the spray gun, distance from the surface and speed at which the gun passed over the surface.
If a sample didn’t have the bell curve pattern, the team could adjust the pressure for one or both of the types of air delivered through the spray gun: fan air, which creates the semicircular fan pattern of the plume, and atomizing air, which atomizes the coating material as it comes out of the gun. If, for example, a coating sample was thin in the middle and thick at the edges, that could mean that the spray had too much fan air that blew the coating to the edges of the spray plume. If the coating was splotchy on the sample, that indicated bigger droplet sizes, possibly from the atomizing air not breaking up the coating material well enough. If the coating was too dry on the surface or drying before it hit the surface, then the spray probably had too much atomizing air.
To measure the coating thickness — and tell if they had achieved that bell curve — the team employed blue light and white light scanners, which project a pattern on the surface to be measured and then take a digital image of the pattern, calculating an elevation map of the surface accurate to within less than 25 micrometers. They would image the surface before and after spraying it and calculate the elevation differences to project the side view sprayed coating pattern.
Through the spray experiments, the team discovered that the high-pressure spray approach was inefficient — very little was making it to the surface, Pfeifer says. At 1,200 pounds per square inch, a large volume of coating material came out of the gun quickly, creating a plume about 1 meter wide from a distance of 1 meter from the surface. The result was that very little of the material would reach the surface, especially if that surface was narrow or cylinder shaped.
“It’s just going into the atmosphere and you’re just sweeping it up,” he says.
Making adjustments
So they adjusted the setup to spray from a closer distance, under a lower pressure — 300 psi. To keep the coating material flowing through the gun at the lower pressure, they increased the temperature to 54 degrees Celsius from 32 degrees. They installed shear mixers, with blades designed to cut up the large particles in the coating mixtures as they flow from their mixing pots to the spray gun.
To fight blockages, they added logic to the robot’s software that would very quickly turn the spray gun trigger off and on whenever it detected a pressure spike. Because the spray gun is the smallest orifice in the system, it would most likely be the location of a blockage. Toggling the trigger would cause a needle in the nozzle to rapidly push into the orifice and then draw back, quickly unblocking the passage without affecting the spray results.
Once the team had adjusted the robot setup to produce bell curve-worthy sprays on flat, horizontal panels, they experimented with vertical panels and with spraying onto a horizontal surface from below to make sure the sprayed coating would adhere and not slide off.
With the setup and settings figured out for producing a reliably consistent bell curve spray pattern, they could direct the robot to spray at the correct step distance — the distance that the spray gun is moved over for subsequent passes. This technique makes the bell curve-shaped deposits from consecutive passes overlap to create a uniform coating depth across the entire surface.
So far, Lockheed Martin has two of the robots operating in Courtland, Alabama, and the setups will be replicated if the company ramps up for large-scale manufacturing, Pfeifer says. In the meantime, Aerobotix is adapting its solution for another customer: The company announced in June that it will share its robotic coating techniques with Automated Solutions Australia as allowed by a 2021 U.S.-Australia hypersonics research pact. Pfeifer says those robots will also be built from off-the-shelf components, with similar challenges to the Lockheed Martin project.
The team had a humbling moment after one of its first attempts at spraying a part for Lockheed Martin. Initially, the spray was a success, and the team members were high-fiving and congratulating one another. A few days later, Pfeifer says, he received an email from Lockheed Martin with photos showing the coating peeling away from the part surface.
“You think, ‘Oh, man, how much of this do we have to start over, and what do we have to look at again?’” he says. “‘What did we mess up, or what did we miss?’ It takes your confidence away pretty quick.”
All of the test results and settings for the tested setups were stored in a database, so the Aerobotix team and Lockheed Martin were able to figure out the problem in about a week: They had underestimated how precisely they needed to get the ratio of the two components of the coating mixture. The ratio was off, and the coating hadn’t cured properly.
“That’s one moment that kind of sticks with me,” Pfeifer says. “Everyone was doing their own soul-searching.”
“We needed to know more than ‘Hey, the pump is running.’ We needed to know exactly how fast it was running and how much material was exiting that pump.”
Keith Pfeifer, Aerobotix

About Keith Button
Keith has written for C4ISR Journal and Hedge Fund Alert, where he broke news of the 2007 Bear Stearns hedge fund blowup that kicked off the global credit crisis. He is based in New York.
Related Posts
Stay Up to Date
Submit your email address to receive the latest industry and Aerospace America news.
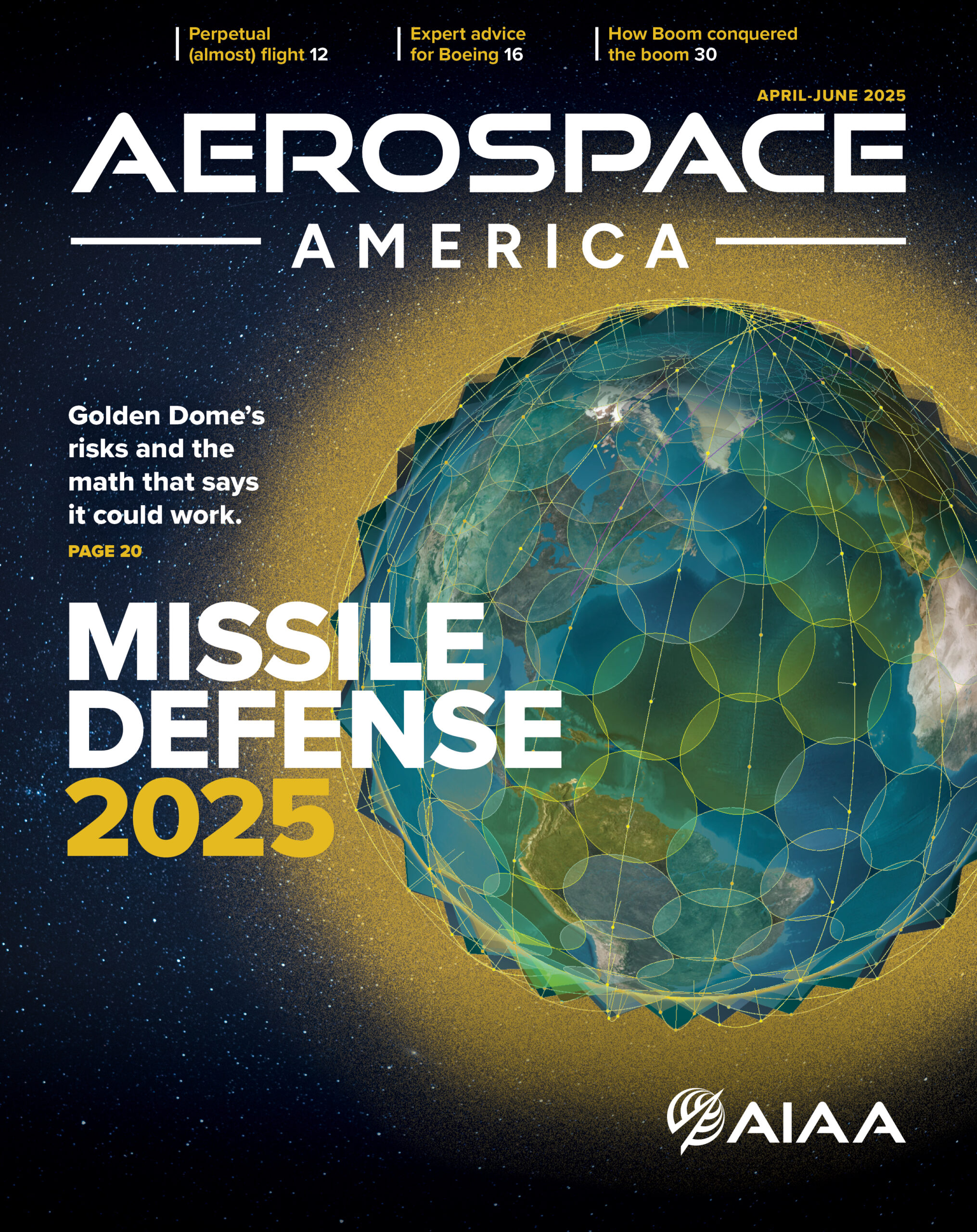
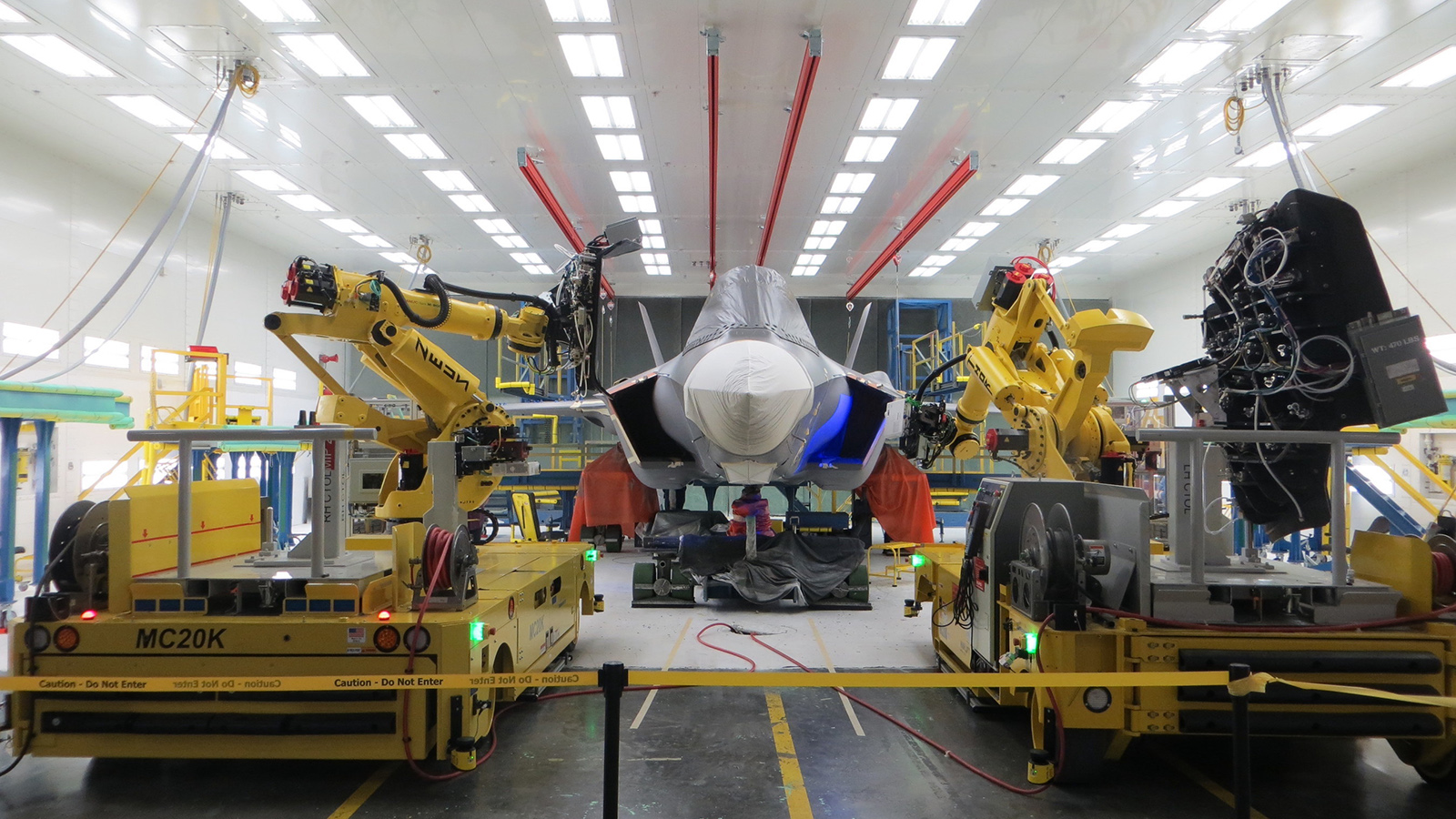
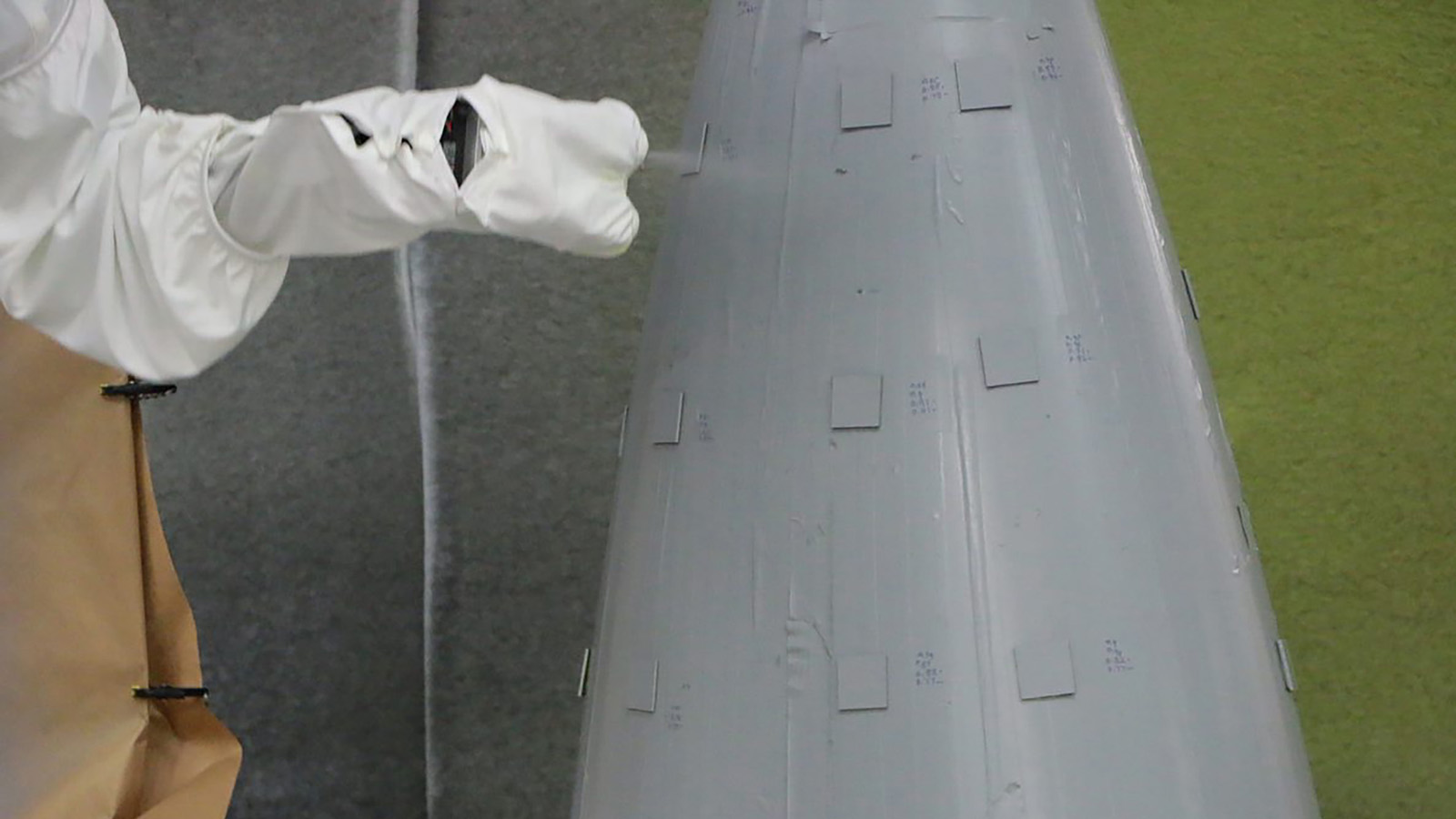