Stay Up to Date
Submit your email address to receive the latest industry and Aerospace America news.
Making a single hypersonic weapon or space launch vehicle is one thing. Mass producing them is quite another. The strong, heat-resistant ceramic components they require are extremely difficult to produce. Keith Button spoke to materials scientists who think they have the solution.
As aerospace engineers dream up new hypersonic weapons and space launch vehicles, they will need ceramic parts that can withstand temperatures as high as 2,700 degrees Celsius and drag forces of hundreds of kilograms that are encountered at speeds of Mach 5 and higher, such as on nose cones, wing leading edges and engine inlets.
The problem is: These ceramics are harder than titanium and brittle, making them tricky to work with.
To make a ceramic part, a technician typically presses a soft clay-like material into a die to create an approximation of the desired shape, hardens it in a furnace and then grinds it down to the precise shape. This milling process can take months and result in chipped or cracked parts.
Materials engineers and chemists at the U.S. Naval Research Laboratory in Washington, D.C., are developing a 3D-printing method that could produce the precise ceramic part shape with no milling required. Components could be made by any aerospace manufacturer with a particular kind of off-the-shelf commercial 3D printer, a paste of metal and polymer devised by the NRL scientists, and a furnace to cure the parts.
Early research
The idea of printing ceramic parts sprang from the NRL chemistry group’s development, starting about 12 years ago, of a polymer resin powder that it mixed with various metal powders to make refractory carbides, which are a type of extremely heat-resistant ceramic. The NRL researchers made pellets from the polymer resin mixed with metals like silicon, titanium or tungsten, and then smushed the pellets with a hydraulic press and die into simple shapes. When they heated these pressed shapes in a furnace filled with argon gas at 1,500 degrees Celsius — like firing a clay pot — the polymer resin charred into carbon and reacted with the metals to form a ceramic.
The researchers investigated the 3D-printing idea because they wanted to apply their polymer-metal ceramics chemistry to more complex shapes than the discs, spheres and cones that they were making, explains Boris Dyatkin, a materials research engineer at the NRL. With the die-press method, the size and shape of the ceramic part is dictated by the die, and some shapes aren’t possible with a die press. Also, “if you need to change the dimension of the part, or if you need to change a certain geometry aspect of it, it’s more tricky to do it quickly,” he says.
With 3D printing, “you’re basically getting more customization in terms of what kind of a ceramic you can make,’’ Dyatkin says.
Printer options
When the NRL researchers began to work in earnest on the 3D-printing concept, in 2018, they first had to decide which type of 3D printing was best. They considered lots of printer options. One possibility was fused deposition modeling. A printer head mounted on a robotic arm deposits beads of molten polymer that harden, layer upon layer, to form the object. Another candidate was powder-bed 3D printing. A laser melts specks of powder as layers of the powder are added to a box-like bed, and these specks harden together to create a structure. The shape is revealed by removing the loose powder. Or, alternatively, a printer head injects binding material into the powder to create the structure.
The researchers settled on a 3D-printing method called robocasting. They based this decision on the advice of NanoArmor, a California research and development company that pays the NRL to make the ceramics and test them for the Missile Defense Agency’s hypersonic materials development program.
Normally, these robocasting printers make items ranging from pottery with intricate lattice structures to complex-shaped concrete panels for buildings. The printer’s robotic arm moves a printer head that extrudes beads of paste that harden as they dry.
These printers were attractive, because robocasting can print larger structures than other 3D-printing methods, and it’s cheap and simple. With virtually no training, “anybody could essentially print whatever they wanted to,” says Tristan Butler, a materials chemist at the NRL.
Robocasting also opens possibilities for creating new ceramic composites. Manufacturers could add ground-up carbon fibers, in powder form, to the paste to make a carbon-fiber composite ceramic, Dyatkin says. Or, under two concepts the researchers haven’t explored yet: 1. A printer could extrude paste onto woven carbon-fiber mesh. Or, 2. Without a printer, the mesh could be dipped into a less viscous version of the paste or the liquidy paste could be poured into a mold containing the mesh. With both concepts, the combined mesh and paste would be fired in a furnace to create the composite ceramic.
Their big challenge was to make a paste that would be accepted by the printer and harden into parts that would be as dense as those they had made earlier. Generally, denser ceramics are stronger and more heat resistant.
They needed a binder to hold the mix together while dispersing the metal and resin molecules evenly throughout the paste.
The paste had to be liquid enough to flow through the printer head, but once extruded it couldn’t be too damp or too dry. “There’s kind of a delicate balance,” Butler says. “You don’t want it to dry too fast, because it will induce cracking. But you want it to dry quick enough that you can deposit multiple layers to build taller structures. It’s something you have to dial in.”
The key to achieving the right viscosity would be the choice of binder, which is a polymer and plasticizer that’s mixed in powdered form with the powdered resin and metal. Liquid is added to create the paste. Once a part is printed, it’s fired in a furnace to trigger the chemical reaction that turns the hardened paste into a ceramic, after burning off the binder.
The NRL researchers tried 10 to 15 binders common in 3D printing. Some were water-soluble and others alcohol-soluble. The scientists made pastes with each and created test discs. One of the water-soluble versions was chosen, because it proved best at creating a homogeneous mix of the right viscosity.
Looking ahead
At the moment, the shapes they’ve made by robocast printing are not as dense as those they’ve made with the die-pressed technique. The NRL researchers continue to search for the optimal heating rate for the furnace, meaning one that burns off the binder completely while fostering the resin and metal chemical bonds that must form to create a suitably dense ceramic. The researchers are also working toward printing objects — hollow cylinders and tapered and conical discs — that are taller and made from smaller beads of extruded paste, known as pixels in the industry. The smaller the pixels, the more precise and finely detailed the 3D-printed object can be. The NRL researchers are printing parts that are several centimeters tall made up of pixels that are just under a millimeter in diameter. They think eventually their printing method could produce parts as large as needed — building-size, in theory — of any shape. They haven’t set a pixel size target yet.
Another goal: Figuring out how to create 3D-printed ceramics that are as close as possible to the density of die-pressed ceramics. To test hardness, they employ a microindentation tester. A small sample of the ceramic is placed on the device’s platform, and a pin head measuring about 100 microns in diameter presses down on the surface to a preset pressure. The larger the microscopic indentation, the softer the material.
To assess how stable and strong the material will be when heated, they examine microscopic crystals in the ceramic with the help of an X-ray diffraction machine. A sample is placed on a pressure plate in the center of the machine; an X-ray tube shoots X-ray beams at the sample while a detector behind the sample rotates through a range of angles to pick up the reflected beams. The machine churns out graphs depicting the angles at which the X-rays are reflected by the crystals in the material and the intensity of the reflected X-rays. The various peaks in the graphs create signature patterns that software analyzes to identify the type and phase of metal or carbon crystals in the material, as well as size and volume of the crystals.
Another issue is that, so far, the 3D-printed ceramics have come out more porous than the pressed discs. In some cases, those microscopic gaps need to be filled to make the material denser and therefore stronger and more heat resistant. One option would be vapor infiltration. A gas in the furnace chemically reacts with the ceramic — either as it is forming or after it has formed — and fills in any pores. Another idea is to paint a solution on the 3D-printed object that would fill in the pores through a chemical reaction at lower temperatures, Butler says.
Even at this stage, the NRL researchers are thinking about how to make the process as easy as possible for aerospace manufacturers to adopt. The researchers sought advice from NanoArmor, whose executives have helped commercialize new materials and electronics technologies for several companies. Parts must be affordably mass produced, which means initial ingredients must be chosen with cost in mind. Efforts must be taken to eliminate any unnecessary steps. “We pushed down requirements about scaling up, about costs, about timing,” says Terrisa Duenas, NanoArmor chief executive. “A lot of times when you make a material, you don’t even think about how to scale it up. And it just seems like: ‘Well, we’ll multiply by three or 10 or whatever you need,’ but a lot of technologies don’t scale like that.”

About Keith Button
Keith has written for C4ISR Journal and Hedge Fund Alert, where he broke news of the 2007 Bear Stearns hedge fund blowup that kicked off the global credit crisis. He is based in New York.
Related Posts
Stay Up to Date
Submit your email address to receive the latest industry and Aerospace America news.
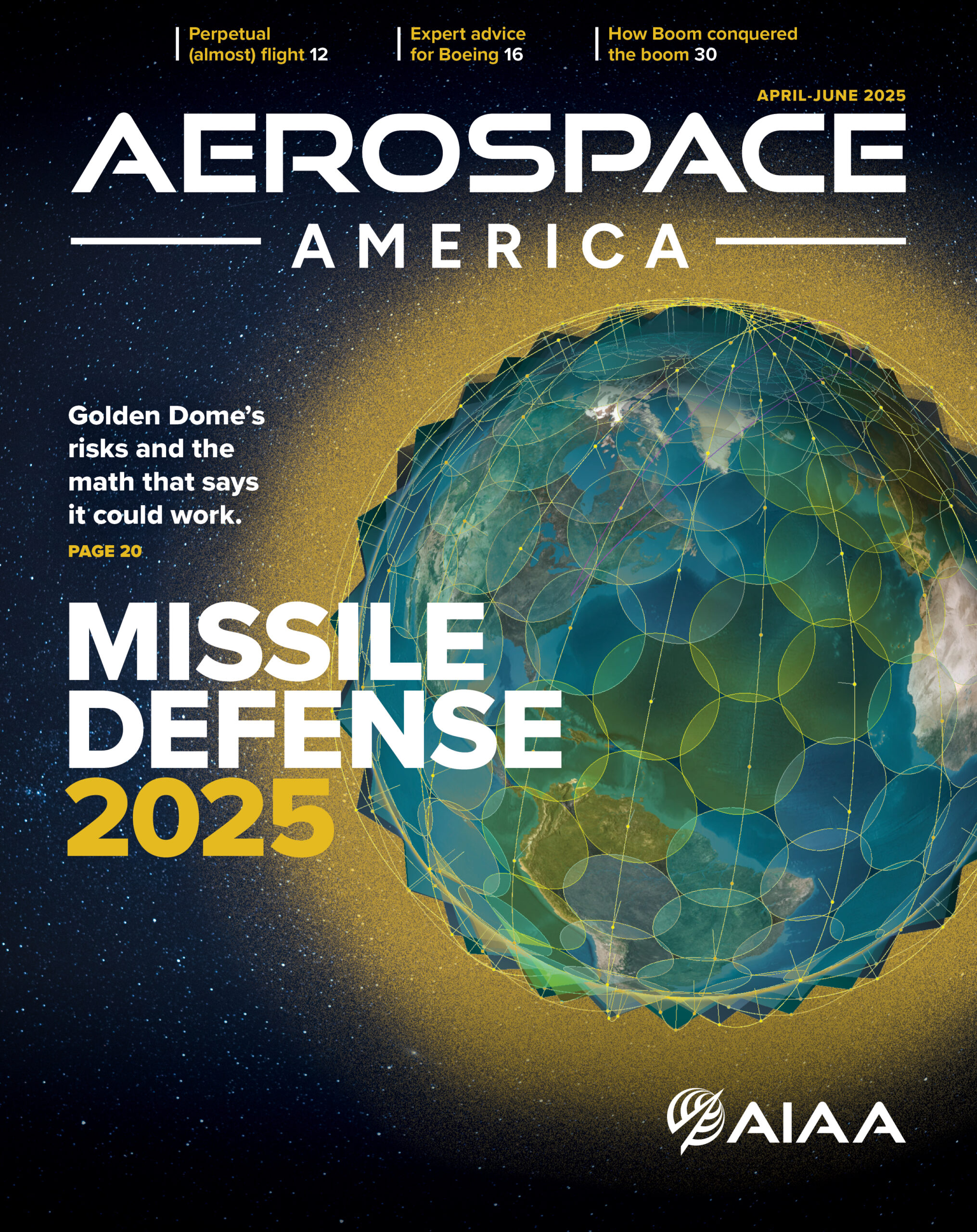
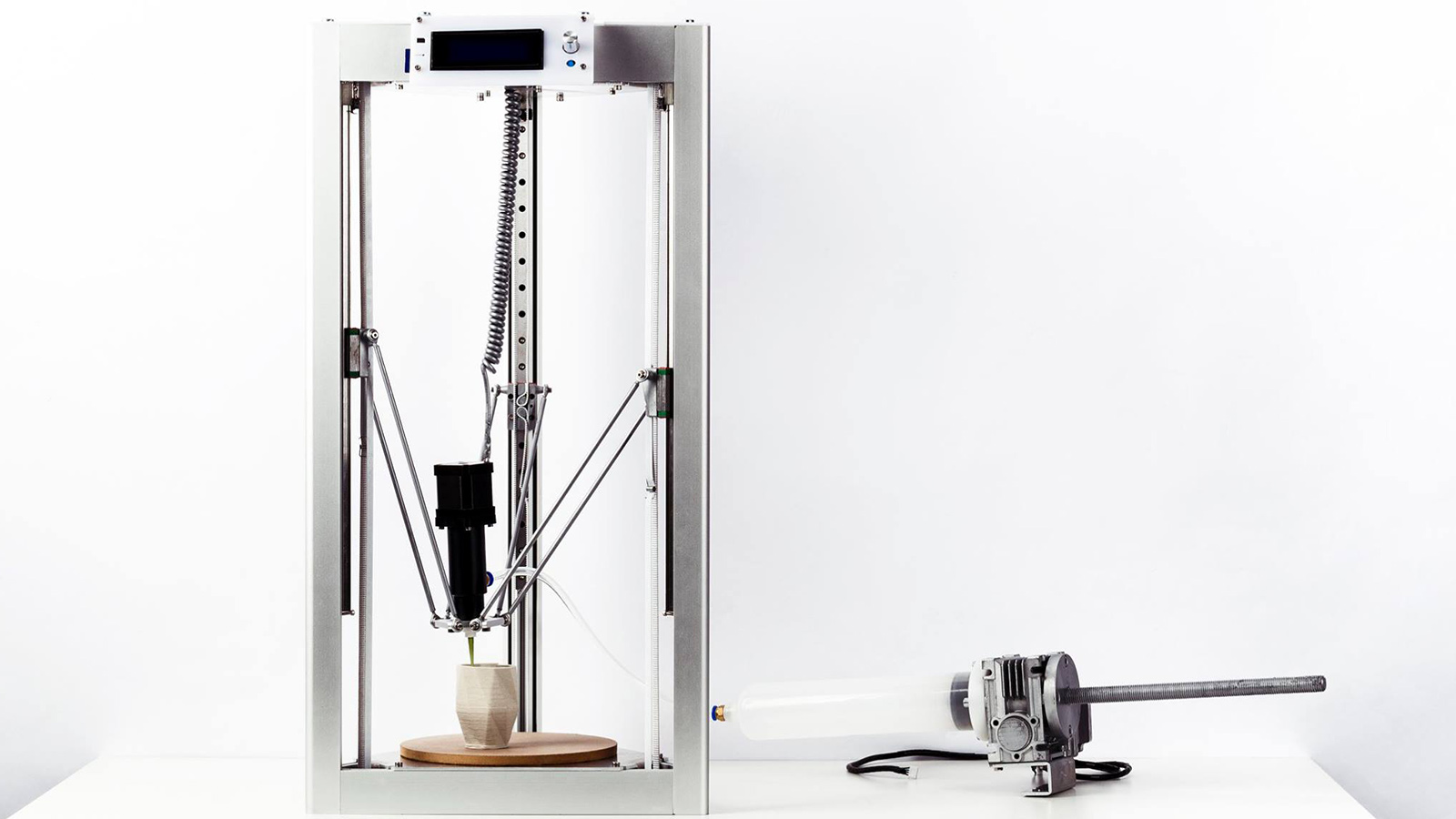
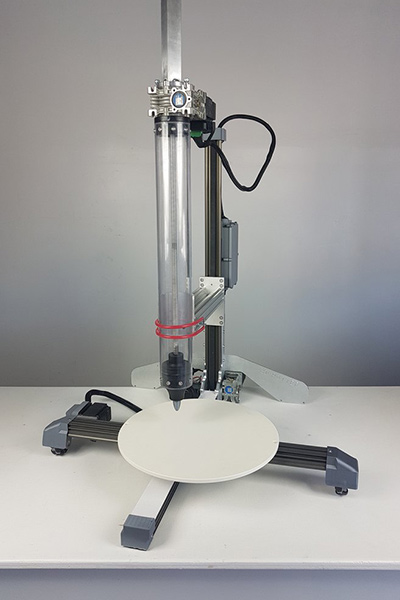
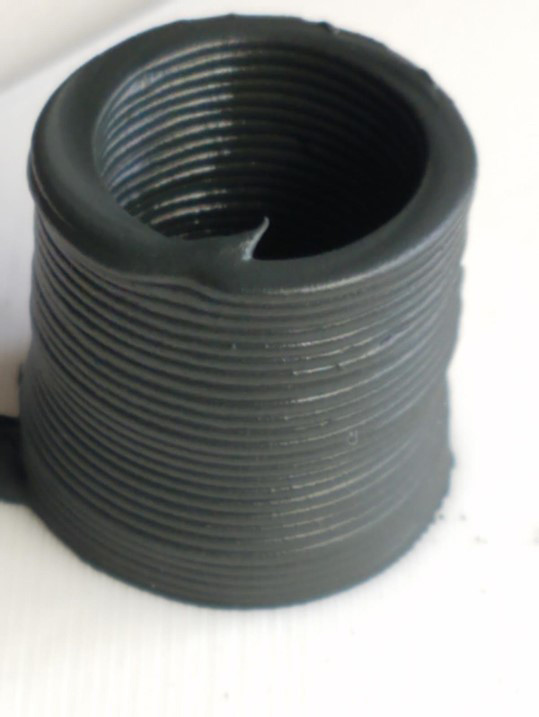
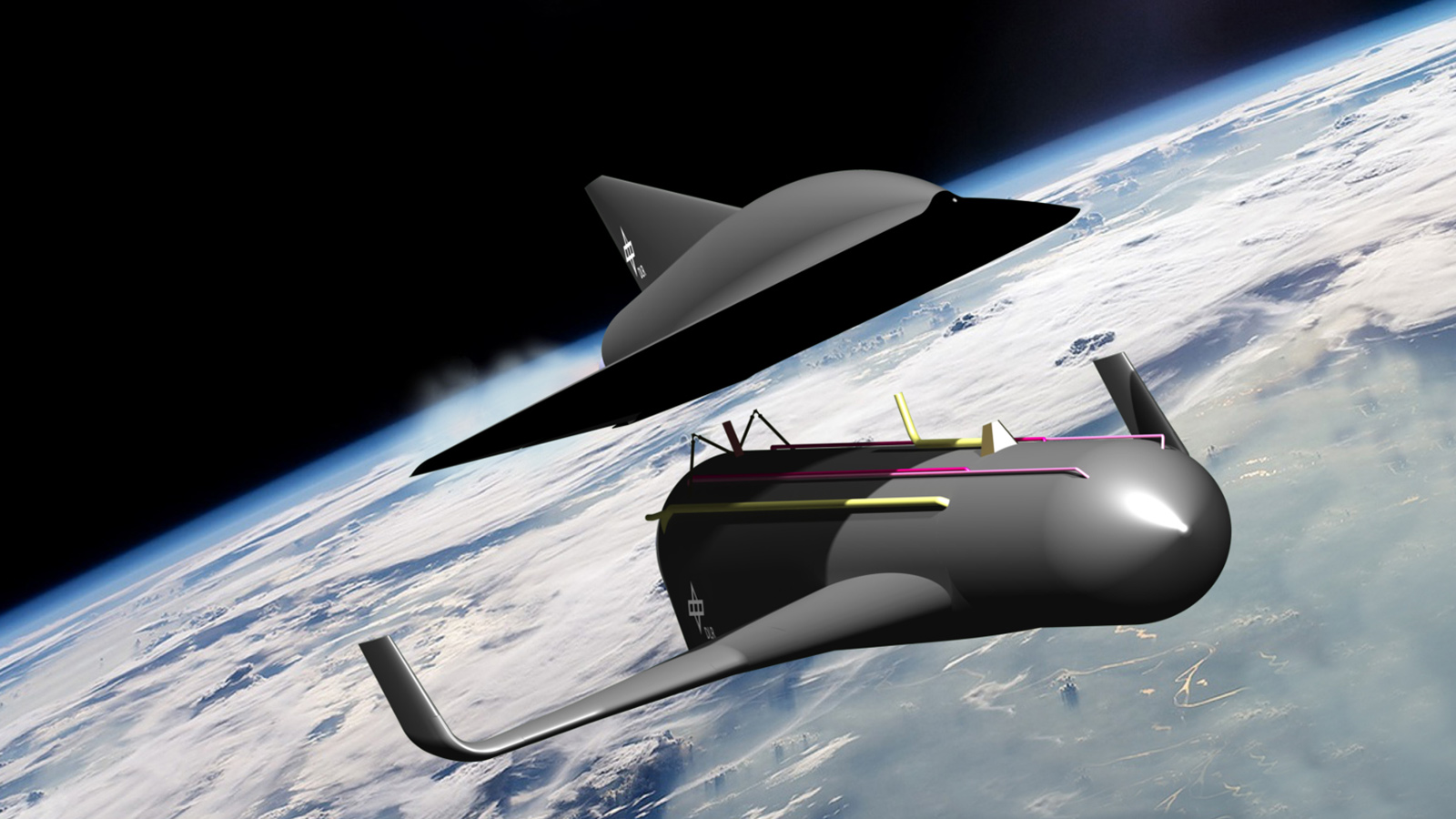