Stay Up to Date
Submit your email address to receive the latest industry and Aerospace America news.
NASA researchers plan to present complete findings in May
When NASA dropped a carbon fiber mockup of an electric aircraft cabin from a crane in November, the cabin impacted the ground with a sickening crack. Researchers and others in attendance were surprised to see that the roof of the six-seat mockup had collapsed down into the cabin where six crash dummies were located.
If humans had been aboard, how would they have fared? Answers might come in May, when NASA researchers plan to present a paper at the Vertical Flight Society’s 79th Annual Forum and Technology Display in West Palm Beach, Florida. At the moment, NASA is still evaluating camera footage and pressure readings from sensors on the dummies and throughout the structure to determine the severity of the impact, said Justin Littell, a mechanical engineer at NASA’s Langley Research Center in Virginia, who helped design the test.
The roof collapse was a surprise. “The drop test was based on simulations we had been running. Our computer models predicted one thing and then, of course, the test results said something else,” Littell said. “So we are now going through the results to refine our computer modeling.”
He added: “That’s not necessarily bad. That’s the reason you test.”
The results will help researchers design the next cabin test and assist FAA and other regulators when the time comes to decide how rigorous the standards for certification will need to be for passenger eVTOLs, electric vertical takeoff and landing aircraft.
The test at Langley’s Apollo-era Landing and Impact Research Facility, proposed by NASA for demolition, took almost three years to design and was implemented by about 40 people, Littell said. Although the test article did not have wings or rotors, NASA designed it to represent a typical lift-plus-cruise eVTOL body, which carries two types of rotors — some for vertical lift and others, usually one or two, for forward propulsion.
Littell said NASA used published industry specifications to design the cabin. Although the mockup was modeled after a lift-plus-cruise configuration, the data from the crash test could be applicable to other types of eVTOLs, such as tiltrotors, Littell said.
The agency designed and built its own energy absorbers in the subfloor and the seats of hybrid material made up of carbon fiber and aramid (aromatic polyamide) fiber, which is used in applications ranging from ballistic-rated body armor to marine hull reinforcement. NASA said the subfloor and seats functioned as intended and limited the effect of the impact on the crash test dummies.
To advance the research, conditions in the next drop test will be altered in some way, Littell said: Either the design of the cabin, the overhead weight in the roof or the speed or trajectory of the drop. The November test was conducted under NASA’s Revolutionary Vertical Left Technology project that includes research on advanced air mobility, a field that includes passenger eVTOLs.
Get the latest news about advanced air mobility delivered to your inbox every two weeks.

About paul brinkmann
Paul covers advanced air mobility, space launches and more for our website and the quarterly magazine. Paul joined us in 2022 and is based near Kennedy Space Center in Florida. He previously covered aerospace for United Press International and the Orlando Sentinel.
Related Posts
Stay Up to Date
Submit your email address to receive the latest industry and Aerospace America news.
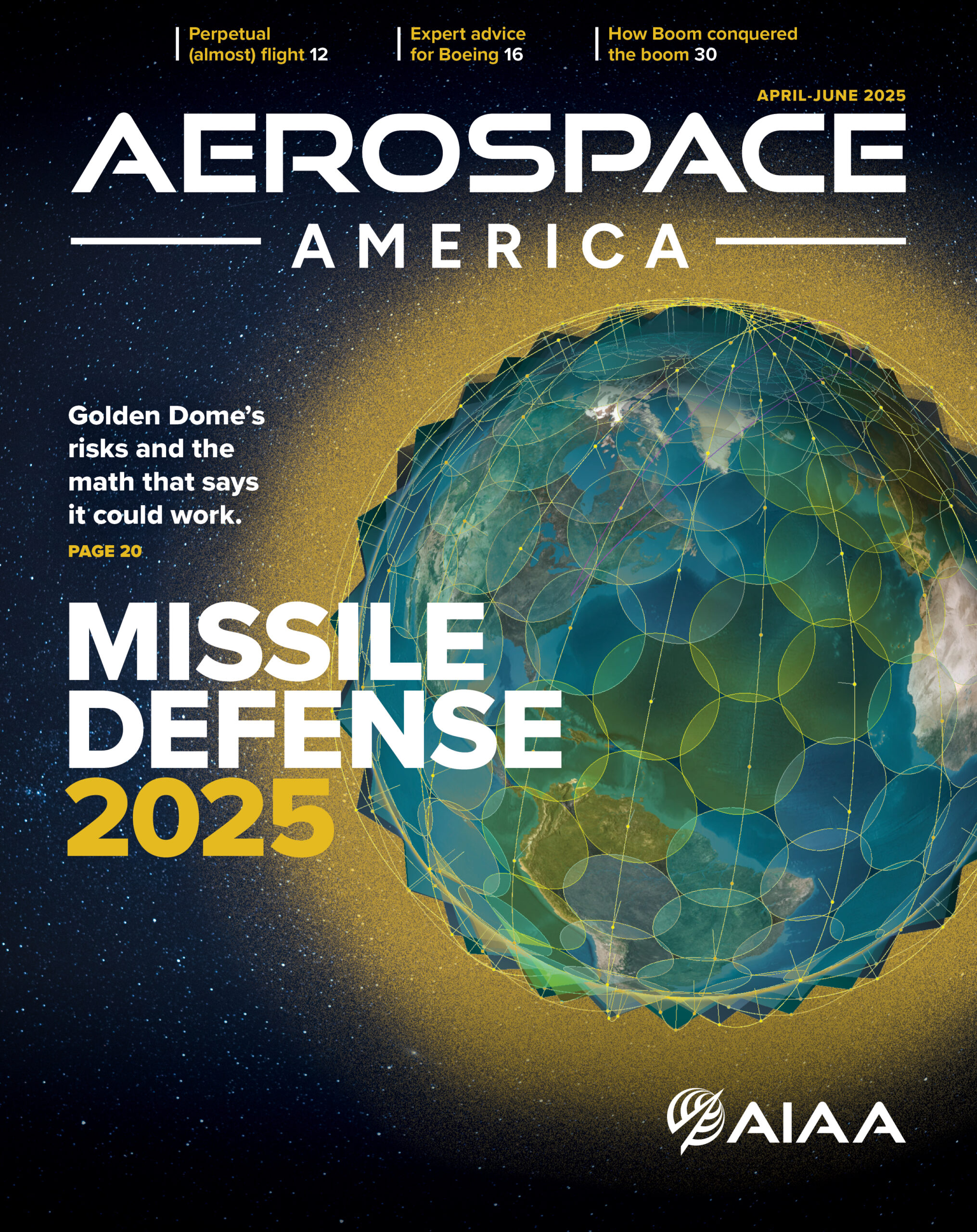
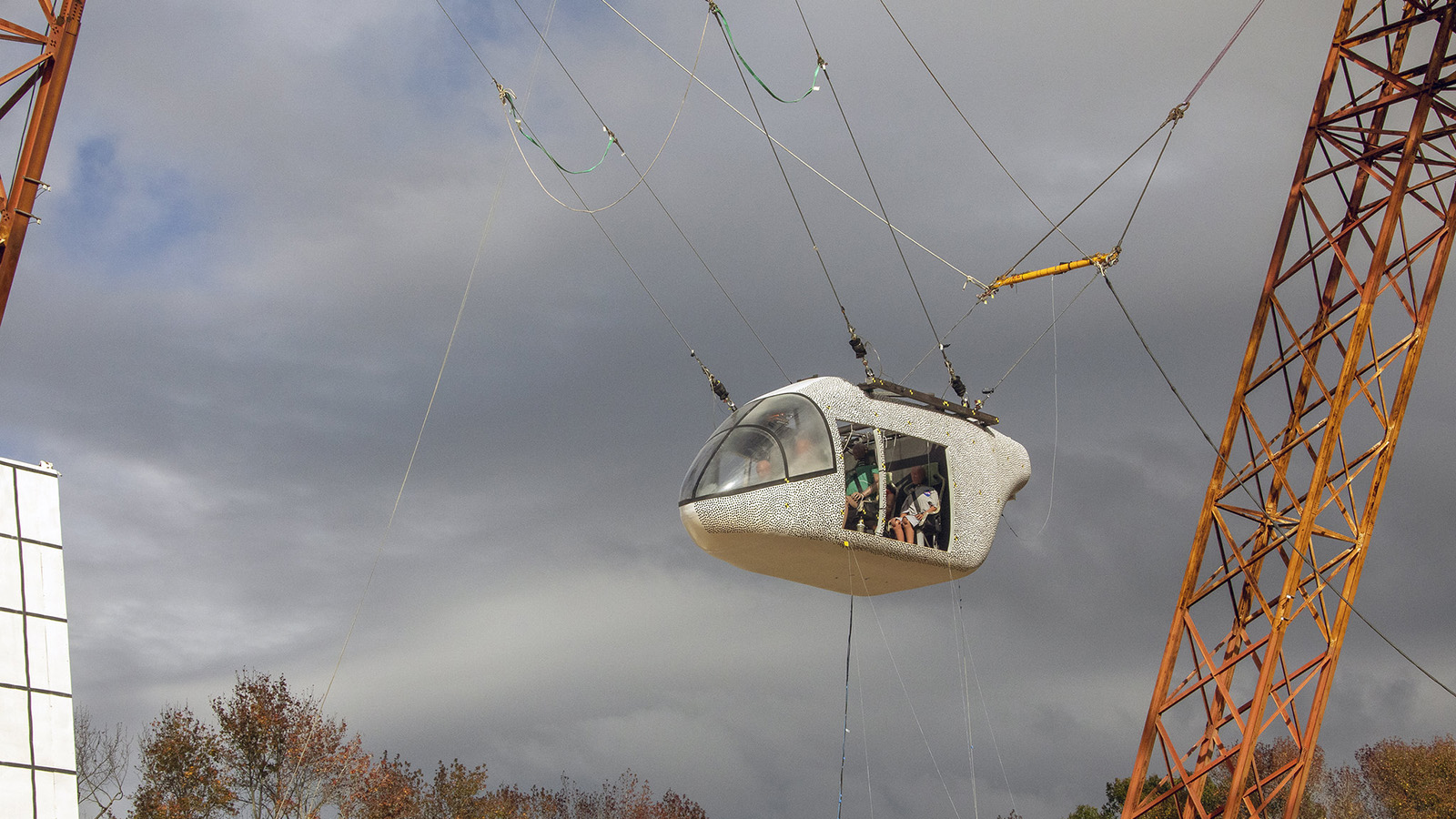