Stay Up to Date
Submit your email address to receive the latest industry and Aerospace America news.
The Thermophysics Technical Committee promotes the study and application of mechanisms involved in thermal energy transfer and storage in gases, liquids and solids.
During the past year, several milestones in aerospace vehicle heat transfer analysis and thermal management were accomplished. These include commencement of an asteroid sample return mission, post-flight analysis from the initial flight of NASA’s next crewed spacecraft, advances in testing of thermal protection system (TPS) materials, and new technology development for in-space heating mitigation.
NASA’s Origins, Spectral Interpretation, Resource Identification, Security-Regolith Explorer, or OSIRIS-REx, lifted off from the Kennedy Space Center in September with the goal of retrieving a sample from the asteroid Bennu and returning the sample to Earth. The OSIRIS-REx spacecraft leverages the entry, descent and landing system of the sample return capsule from the Stardust mission in 2006. The OSIRIS-REx atmospheric entry speed of 12.2 kilometers per second will be only slightly lower than that of Stardust, which was the fastest spacecraft in history to enter the Earth’s atmosphere. Engineers from the NASA Ames Research Center in California provided aerothermal environment analysis, and worked closely with prime contractor Lockheed Martin to confirm the applicability of the Phenolic Impregnated Carbon Ablator material used in Stardust for the OSIRIS-REx mission. Arc jet test facilities at Ames were used to validate and verify the TPS design selected for mission implementation.
In June, the 46th AIAA Thermophysics Conference in Washington, D.C., included a thorough multisession review of TPS flight data and post-flight analysis for the first test flight of NASA’s Orion Multi-Purpose Crew Vehicle in December 2014. For this flight, named Exploration Flight Test 1, the re-entry heat shield was instrumented with thermocouples, radiometers, pressure sensors and ablation sensors. After recovery, the heat shield was removed from the structure, and samples were extracted for post-flight inspection. Detailed analysis of flight data has been performed with the aim of improving the predictive capability of numerical models, thus reducing uncertainty margins. Extensive TPS design and fabrication work has been performed in 2016 for the next Orion mission, Exploration Mission 1, scheduled to launch in September 2018. Diverging from the honeycomb-reinforced material used for the first Orion flight, the heat shield for this second flight will be constructed from molded tiles.
As part of the Advanced Ablation Characterization and Modelling program at the German Aerospace Center, a series of TPS material tests has been conducted at the center’s L3K arc-heated wind tunnel with the goal of providing detailed validation data for numerical modeling of TPS material response. Ablative materials including carbon phenolic, silica phenolic and cork phenolic were investigated at selected conditions for Earth and Mars entry trajectories. Gas temperature measurements employing the Coherent Anti-Stokes Raman Spectroscopy method provided important data concerning the thermal nonequilibrium behavior in both the freestream and disturbed flow regions around the samples.
The past year has seen significant progress toward effective passive thermal management of next-generation Gallium Nitride based solid-state power amplifiers, or GaN SSPAs, for use onboard spacecraft. Next-generation GaN SSPAs are expected to reach heat fluxes well beyond the limitations of current thermal management techniques, and the full potential of these devices can be realized only through development of new cooling systems with minimal size, weight and power requirements. In collaboration with the Air Force Research Laboratory, small businesses ThermAvant Technologies of Missouri and Advanced Cooling Technologies of Pennsylvania demonstrated passive thermal management devices capable of spreading GaN SSPAs heat loads for transport through conventional heat pipes to spacecraft radiators. ThermAvant Technologies implemented innovative microchannel patterns and high performance working fluids in a novel heat spreader design. Advanced Cooling Technologies used new wick configurations and an internal locking feature to develop a high heat flux vapor chamber with low thermal resistance. ★
Contributors: Ali Guelhan, Mairead Stackpoole, Brent Taft
Stay Up to Date
Submit your email address to receive the latest industry and Aerospace America news.
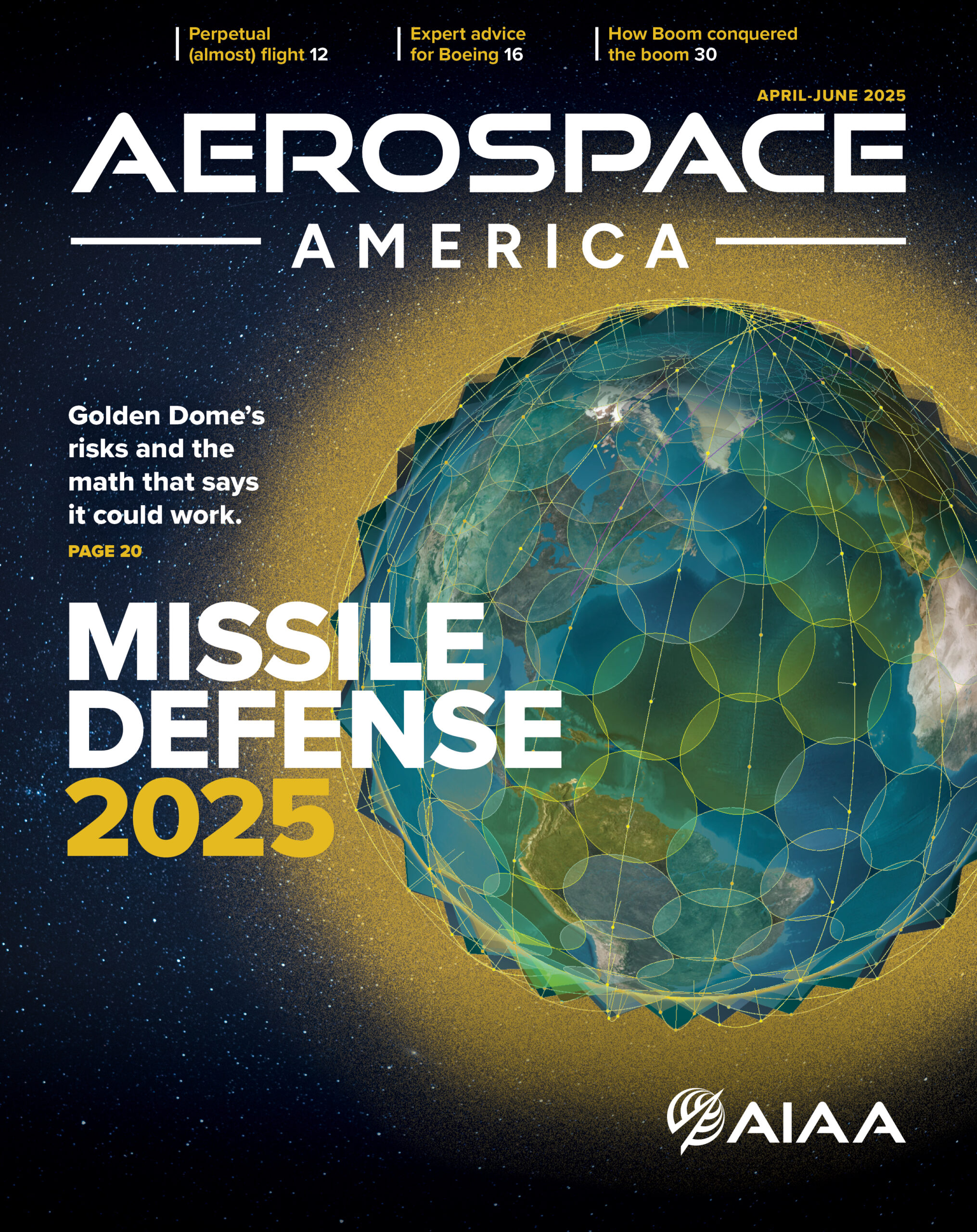