Stay Up to Date
Submit your email address to receive the latest industry and Aerospace America news.
The Applied Aerodynamics Technical Committee emphasizes the development, application and evaluation of concepts and methods using theories, wind tunnel experiments and flight tests.
A new NASA design method, referred to as Crossflow Attenuated Natural Laminar Flow, was model-tested in June in the National Transonic Facility, a high-pressure, cryogenic wind tunnel at NASA’s Langley Research Center in Virginia. CATNLF carefully designs the leading-edge shape of the wing to enable natural laminar flow on typical transport wings with high sweep and Reynolds numbers. Laminar flow has been studied for decades because of its promise for reducing fuel burn via decreased aircraft drag. Laminar flow on typical transport wings would provide the largest performance benefit, but previous laminar flow strategies required the vehicle to either fly slower or add a complex suction system, and both penalties made the technology too costly to buy its way onto the aircraft.
Transition visualization techniques used in the June wind tunnel test showed a near doubling of the extent of laminar flow over the extents previously seen in any natural laminar flow experiment on wings with comparable sweep. Encouraging wind tunnel results have spawned a series of flight tests to further advance the CATNLF technology in flight environment.
In January, rotorcraft researchers reported making significant strides in determining the importance of flow transition and understanding mechanisms of vortex-wake breakdown. The findings were published at AIAA’s Hover Prediction Workshop in San Diego.
Whether a helicopter station keeps above a highway to report the traffic or stays in close proximity to the side of a mountain to deliver supplies to a remote community, hover is an elegant and complicated flight condition. Numerical simulation of hover is full of challenges but offers the reward of great understanding of performance and loads. Better understanding will lead to more efficient, capable and safer rotor designs. The upcoming NASA-sponsored tests at the National Full-Scale Aerodynamics Complex at NASA’s Ames Research Center in California will offer an even richer data set for code and process benchmarking. These tests are scheduled for mid- to late 2020.
In August, NASA and Boeing, as part of the High Aspect Ratio Wing Subproject within the NASA Advanced Air Transport Technology Project, completed tests on the 4.5%-scale, Mach 0.80 Transonic Truss-Braced Wing, or TTBW, model in the Ames 11-Foot Transonic Wind Tunnel. The objectives were to acquire a test database to validate the aerodynamic performance and vehicle stability and control characteristics. Force and moment, surface pressure, model deformation, oil flow visualization and drag rise data were collected to support the assessment of stability and control characteristics. Data were obtained at Reynolds numbers ranging from 2 million to 8 million per foot and Mach numbers ranging from 0.2 to 0.92. The TTBW concept shows promising fuel burn benefits toward meeting NASA system level metrics.
In May, a new active flow control innovation was tested under NASA’s Advanced Air Transport Technology project, using a 10%-scale high-lift version of the Common Research Model with simple-hinged flaps at Langley’s 14- by 22-Foot Subsonic Wind Tunnel. The objective of the test was to investigate a novel high-lift method that eliminates Fowler-flap mechanism and external fairing on a conventional high-lift configuration. High-lift configurations are needed only during takeoff and landing phases of any flight and are typically retracted during cruise phase of the flight. Eliminating external fairings associated with conventional Fowler-flaps reduces the drag during the cruise phase of the flight and saves fuel. The active flow control innovation, High Efficiency Low Power actuators, achieved a targeted lift coefficient increase of 0.50 using a moderate amount of mass flow and air pressure. The simple-hinged flap configuration equipped with this actuation technology was able to match or exceed the lift performance of the reference conventional high-lift configuration.
Contributors: John Lin, Michelle Lynde, Latunia Melton and Robert Narducci
Related Posts
Stay Up to Date
Submit your email address to receive the latest industry and Aerospace America news.
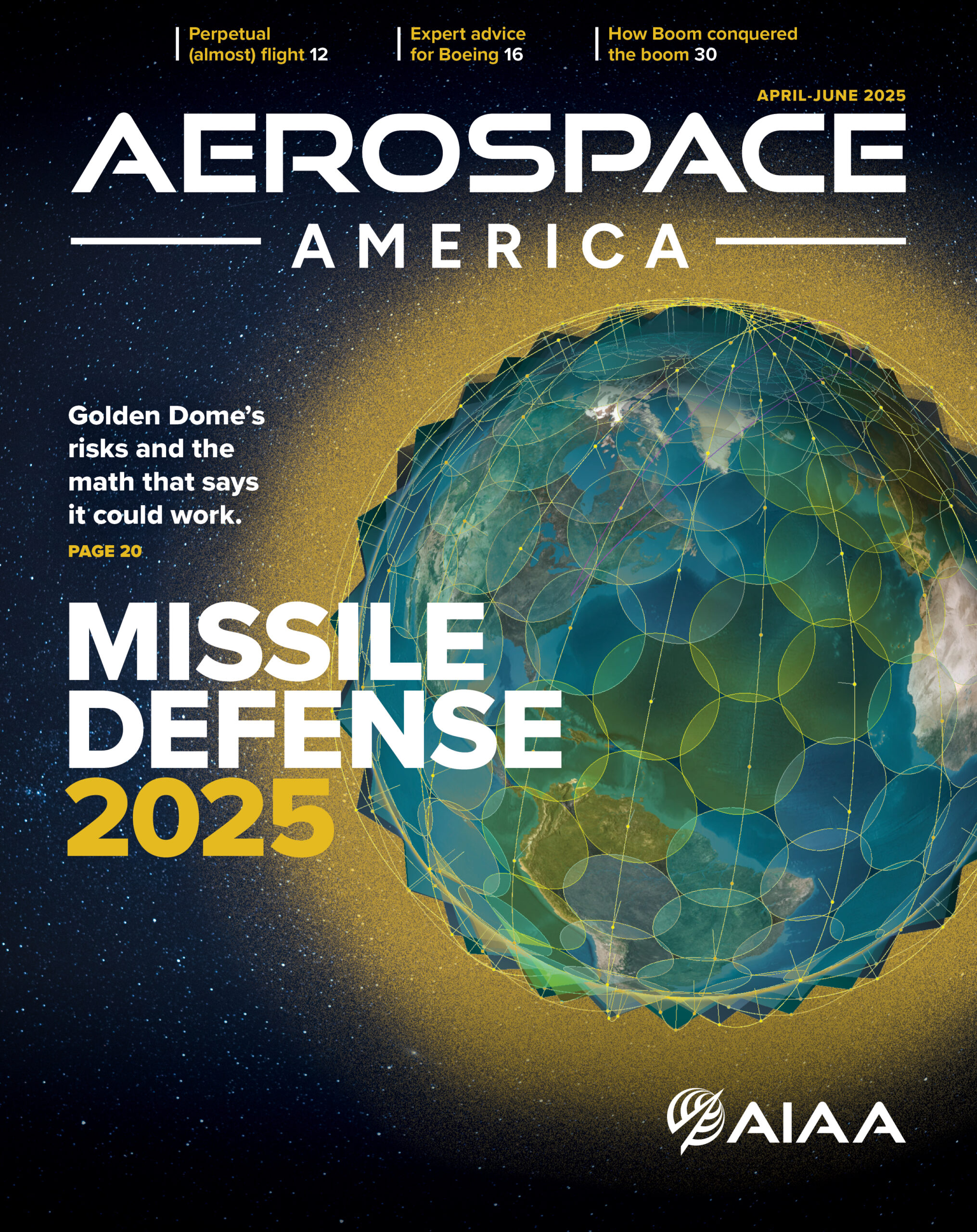