Stay Up to Date
Submit your email address to receive the latest industry and Aerospace America news.
The Materials Technical Committee promotes interest, understanding and use of advanced materials in aerospace products where aerospace systems have a critical dependency on material weight, multifunctionality and lifecycle performance.
In the realm of unmanned aircraft, long-duration mission profiles and increased reliability this year motivated development of innovative multifunctional mechano-luminescence-
optoelectronic, MLO, composites to be integrated into next-generation unmanned aircraft at New Mexico Tech in collaboration with NASA’s Armstrong Flight Research Center in California. MLO composites are composed of two functional constituents, such as mechano-luminescent copper-doped zinc sulfide-based elastomeric composites and mechano-optoelectronic poly (3-hexylthiophene)-based self-sensing thin films. MLO composites can be integrated with fiber-reinforced polymer composites to create autonomous composites, AutoCom, that exhibit a self-powered strain sensing capability that enables detection of fatigue damage and a mechanical-radiant-electrical energy harvesting capability that provides supplemental energy to the aircraft.
Researchers at the University of Alabama in January quantified efficiency of self-healing composites in Mode-1, the term for testing double-cantilever beams of composite. They determined the interlaminar fracture toughness using the ASTM-D5528-13 standard for such double-cantilever beam, or DCB, tests. Seven separate healing cycles with thermoplastic healants were performed to assess healing repeatability with maximum healing efficiencies of 73 percent, and 63 percent achieved after the seventh healing cycle for DCB specimens with and without shape memory polymers, respectively. The importance of this “close then heal mechanism” investigation of dispersed shape memory polymers along the delamination plane was demonstrated.
In March, NASA published its much anticipated technical report, “Vision 2040: A Roadmap for Integrated, Multiscale Modeling and Simulation of Materials and Systems.” Publication of this vision was significant, because materials scientists in the past separated modeling from experimentation. The vision draws these two functions together, so that in the future a simulation can span across all modeling scales to include the structure. The vision was developed under NASA’s Transformational Tools and Technology Project to define the potential 25-year future state required for integrated multiscale modeling of materials and systems to accelerate the pace and reduce the expense of innovation in future aerospace and aeronautical systems. Such an interdisciplinary effort with multiple stakeholders from various backgrounds coming together has profound implications for any engineering community optimization of the development of load-bearing structures.
This road map is a community consensus document and is a result of input from about 450 professionals. This input was obtained through a series of workshops organized by AIAA, the International Association for the Engineering Modelling, Analysis and Simulation Community (also known as NAFEMS) and the Minerals, Metals and Materials Society. Also, a communitywide survey was conducted, and a variety of expert panels were convened. This road map is intended to provide strategic guidance to both public and private research and development decision-makers to achieve the proposed vision for the year 2040.
In the photo: When twisted and deformed, an MLO (mechano-luminescence-optoelectronic) composite generates measurable direct current. New Mexico Tech has conducted research on MLO technology for unmanned aircraft. Credit: New Mexico Tech
Related Posts
Stay Up to Date
Submit your email address to receive the latest industry and Aerospace America news.
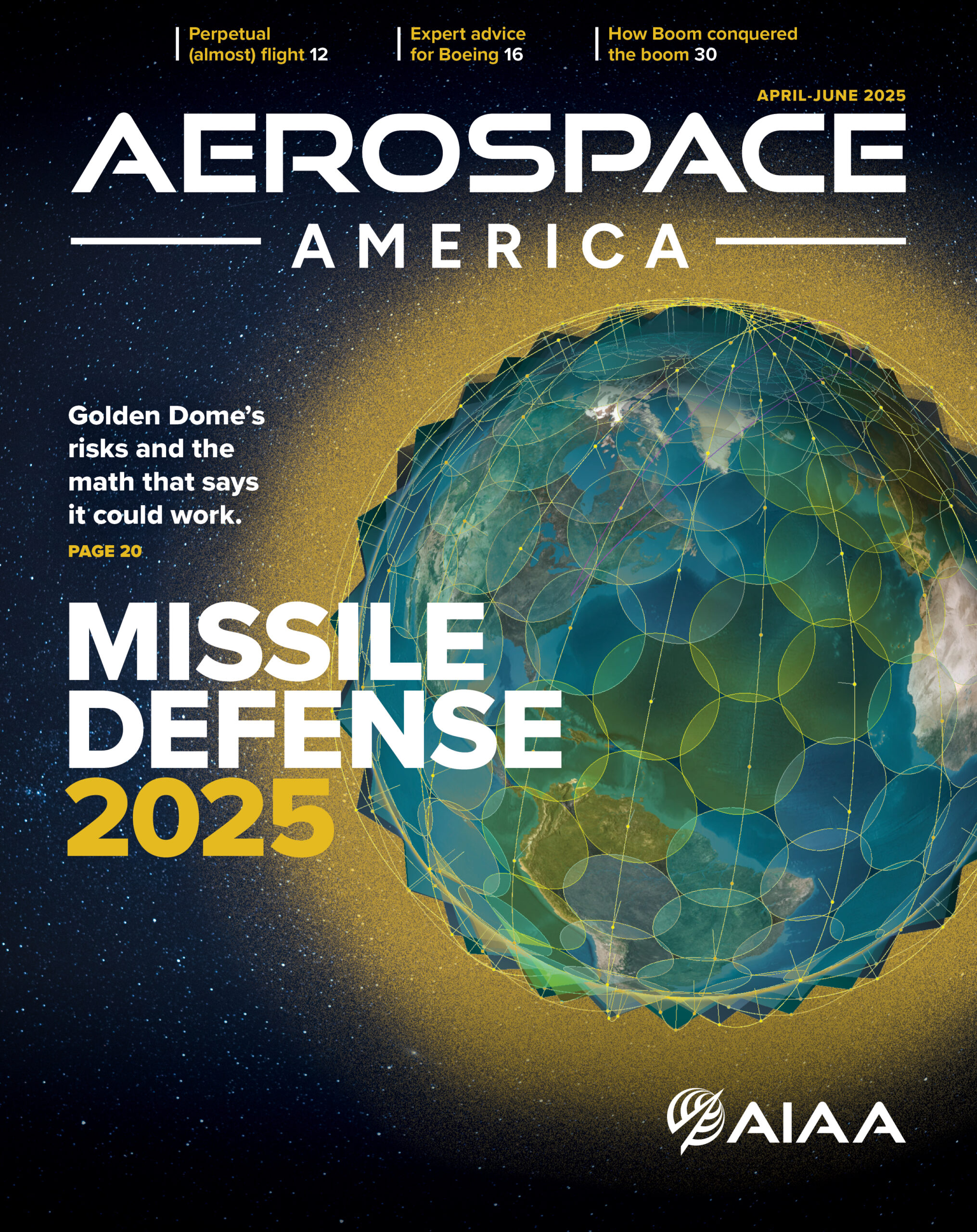