Stay Up to Date
Submit your email address to receive the latest industry and Aerospace America news.
Interest in toroidal propellers has been intense, researcher says
Four years ago, researcher Thomas Sebastian of MIT was given what seemed like a straightforward assignment. His colleagues had begun a NASA-funded project to test the idea of propelling an aircraft, even a small one, by generating an electric field along its wing to accelerate ions.
Electroaerodynamic thrust, or ionic wind, seemed sure to be quieter than generating thrust with propellers, but how much quieter? Sebastian’s mission was to find out.
Comparing the ionic wind to conventional propellers seemed like an unfair comparison, “so I looked at different ways to make them quieter,” Sebastian tells me.
He’d seen images of oddly shaped wings and propellers in experimental aircraft during the World War II era, including ring-shaped wings, rounded like a tank tread, only much lighter. “So I wondered, what would happen if you adopted a shape like that as a propeller?”
Sebastian drew up plans for propellers whose blade tips would meet to form a ring. Now, interest in this concept of toroidal propellers, and their possible applications, has exploded, driven in part by an R&D 100 Award in August from R&D World magazine, and then when MIT posted videos in November describing Sebastian’s work.
With so much publicity, Sebastian says he’s nearly overwhelmed.
“I have been inundated with messages. There’s lots of interest in the hobbyist community,” he says, referring to people who buy consumer drones and alter them. He says he’s also fielded inquiries “from engineers and a few commercial aircraft companies.”
Behind the scenes, engineers and designers are working to determine which aircraft such propellers could be right for. Not everyone is sold on the applicability for their needs.
“I’ve looked at toroidal propellers previously — they are a novelty, but in terms of being either more efficient or quieter, it all depends what you are comparing against and what the propeller is designed to achieve,” says Mark Moore, CEO of Whisper Aero, the Tennessee propulsion developer, in an email.
Whisper is targeting noise by going in a “very different direction” than propellers, “re-inventing the best way to turn electrons into thrust,” specifically with the needs of the U.S. Department of Defense in mind, Moore adds.
Sebastian nevertheless believes that the technology could be potentially groundbreaking for some applications. How could this technology have lain dormant and largely unexplored for so long? One reason might be that for many years, there was no efficient way to rapidly design, build and test variations of the shape for quietness and other factors.
“The big enabler was the fact that we were able to very quickly, with a 3D printer, iterate on these designs in a way that just wasn’t possible or practical, even a decade ago,” Sebastian says.
He is a senior staff member in the Structural and Thermal-Fluids Engineering group at MIT’s Lincoln Laboratory. He and his team tested the ring-shaped rotor forms first in the lab, tweaking them to make them lighter and quieter, and then attached them to drones and flew them indoors.
Though novel for aircraft, Sebastian learned that toroidal shaped propellers were known in the boating industry. A marine propeller company, Sharrow Marine of Detroit, sells them, for example. An MIT patent search turned up a few mentions of toroidal shapes having been studied conceptually, but no examples of them deployed on aircraft.
As MIT describes it in a brief published document, the “closed-form structure” of the ring-shaped or doughnut-shaped propellers “minimizes the drag effects of swirling air tunnels (i.e., vortices) created at the tips of blades and strengthens the overall stiffness of the propeller. These features reduce the propeller’s acoustic signature.”
But Sebastian warns that there might be a diameter limit for toroidal propellers for aviation because they have more mass on the outer edge than traditional pointed blade designs.
“I suspect the largest you could go with efficiency would be about 18 inches [45 centimeters], but that’s just me guessing,” he says. In the lab, the largest he tested was about 20 centimeters.
“You probably can’t just pop off your propellers and pop these on because they are heavier, which is probably going to confuse the heck out of the autopilot features,” he says.
He is working with MIT’s Technology Licensing Office to determine what the next steps should be. “We plan to produce a public briefing that will explain more details.” So far, MIT has published only the brief explanation of the project and some videos showing the propellers in action.
Companies involved in drone delivery and the Drone Racing League were among those who expressed interest, Sebastian says.
I surveyed four AAM companies developing electric air taxis, and each said they watch such research with interest but none had any immediate plans to investigate toroidal propellers. California-based Joby Aviation developed and tested their propellers with NASA researchers.
“We are definitely keeping an eye on innovative research congruent to the AAM space. Our propellers, and their low noise signature, are the result of years of design and testing,” Joby said in an email reply.
And there’s some indication that the ring-shaped propellers may be safer, based on what Sebastian calls a “hot dog test.” Lab workers watched how a conventional propeller and a toroidal propeller impacted hot dogs when striking them.
“The conventional propeller was cutting into the hot dog, but the toroidal propeller just smacked it out of the way, which we saw as, like, maybe it’s safer,” he says.
Get the latest news about advanced air mobility delivered to your inbox every two weeks.

About paul brinkmann
Paul covers advanced air mobility, space launches and more for our website and the quarterly magazine. Paul joined us in 2022 and is based near Kennedy Space Center in Florida. He previously covered aerospace for United Press International and the Orlando Sentinel.
Related Posts
Stay Up to Date
Submit your email address to receive the latest industry and Aerospace America news.
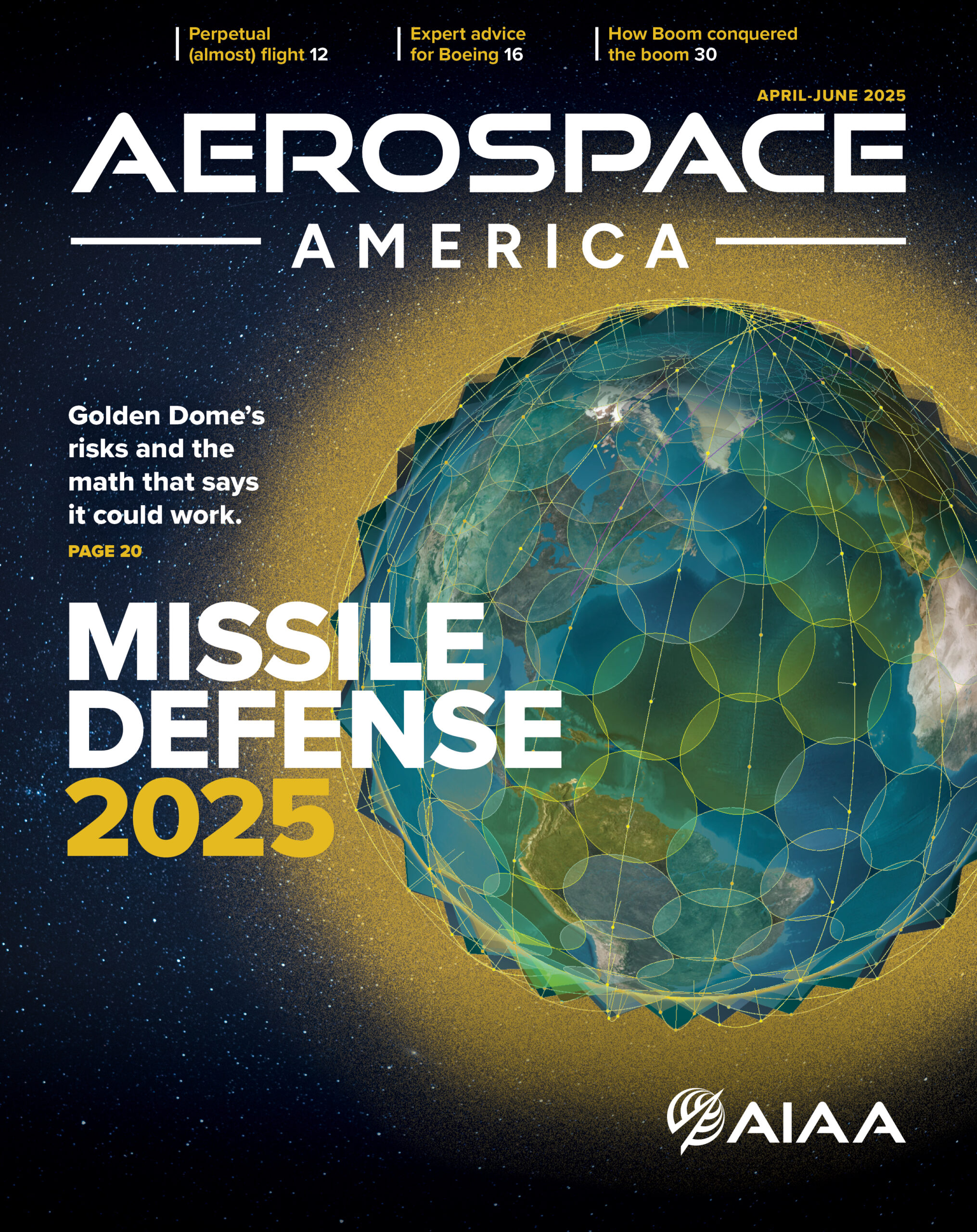