Stay Up to Date
Submit your email address to receive the latest industry and Aerospace America news.
Technologists undaunted by doubts over impact on aircraft designs
The idea of reconceiving the modern airliner to incorporate battery propulsion was all the rage just a few years ago. Boeing in 2010 released conceptual drawings for a 154-passenger hybrid airliner, dubbed SUGAR-Volt, for Subsonic Ultra-Green Aircraft Research, that by 2035 would be powered partly by batteries. Airbus and Rolls Royce followed two years later with the drawing of the 2050 version of E-Thrust — a hybrid electric 70- to 100-passenger regional airliner to be propelled by six electric engines. The concepts were premised on hoped-for revolutionary advances in battery technology that would help airplanes move down the path to reduced carbon emissions.
Then came a NASA advisory committee of aerospace experts, which in May declared that battery-powered regional passenger aircraft are unlikely to fly within 30 years. Even before release of the report, “Commercial Aircraft Propulsion and Energy Systems NASA Research,” battery technologists and aerospace engineers agreed that fundamental science imposes an ultimate ceiling on the energy capacity of batteries, and that powering large jets (defined as 300 passengers) solely with batteries would not be in the cards.
Even so, researchers say they have yet to reach the full potential of batteries for airplanes, and they predict a doubling or even tripling of energy storage compared to today’s versions. If they are right, batteries could still replace jet fuel for some applications and certainly supplement it. New design opportunities would be opened for improved energy efficiency.
One line of research would create a new class of batteries — rechargeable lithium metal batteries — capable of storing much more electrical power for their weight than current batteries, and also of discharging that power quickly. Future advances in battery technology will likely come from research that is focused on more financially lucrative potential applications outside of airplane propulsion, such as automobiles and consumer products. In the meantime, airplane designers will have to prove the reliability and performance of hybrid-electric propulsion — jet-fuel-fired generators powering electric motor propulsion to replace or augment traditionally fueled airplane turbine propulsion — applied to larger and larger aircraft.
The 123-page report says that battery-aided and battery-only propulsion shouldn’t be a high priority for researchers aiming to curb airplane emissions. One reason, according to the committee: Battery technology won’t be developed enough over the next 30 years to meet FAA certification criteria for regional passenger planes. Another reason: Reduction in emissions from using the batteries could be offset by an increase in emissions by the power plants that generate electricity for the batteries.
Batteries also lag conventional jet fuels in terms of energy density, a measure of potential energy per mass. Jet A, the standard kerosene fuel for commercial and military aircraft, has an energy density of 12,000 watt-hours per kilogram. The most advanced aviation batteries such as those powering small drones, have an energy density of 500 watt-hours per kilogram. Even after accounting for the fact that about two-thirds of jet fuel is lost as heat, fossil fuel still is six to eight times more energy dense than the most advanced batteries currently available.
The report findings didn’t quash any existing airplane battery research, but actually helped clarify the place batteries have in the development of electric propulsion for airplanes, says James Felder, an aerospace engineer at the NASA Glenn Research Center in Cleveland who develops next-generation electric propulsion concept aircraft for NASA.
“It went over, actually, very well. We’ve struggled to make clear that batteries have to advance far beyond what they can do today to play even a support role in larger aircraft,” Felder says. “I don’t think it was in any way a ‘You’re going in the wrong direction; you need to go in another direction.'”
The focus of electric airplane research should be on turbo-electrical propulsion — or onboard electric power generated by jet-fuel-fired generators, which could be feasible within 30 years for single-aisle passenger aircraft, according to the report. Turbo-electric propulsion combined with distributed propulsion — placing propellers at various locations on an airplane — and boundary layer ingestion, or moving the air currents that travel along the surface of an airplane, could cut fuel consumption by more than 20 percent for large commercial planes.
“The batteries, we de-emphasized quite a long time ago,” Felder says. “We’ve never really had it in our plan to develop those batteries ourselves. The intent was always to leverage off of advancements that were being made for other applications, such as cars.”
If advanced battery technology under development comes to fruition, then it can be easily slotted into electric systems under development with turbo-electric research, including research into lightweight motors and generators, Felder says.
Most batteries supplying power to electric airplanes under development currently provide about 200 watt-hours per kilogram, Felder says. Jumping to battery energy densities of 1,500 or 2,000 watt-hours per kilogram, their theoretical limits, likely would require radical new concepts for battery materials. Much of the weight of a battery comes from its electrodes, so one idea envisioned by battery developers would be to make the air from the atmosphere serve as the positive electrode, or cathode.
Batteries can have low carbon footprints, but only if they are recharged with electricity generated by environmentally friendly sources, Felder says. As with turbo-electrical propulsion, advanced batteries in the future could allow aircraft designers to create more fuel-efficient aerodynamic shapes or propulsion systems. For instance, battery-powered electric motors can turn any sized propellers or fans located on the wings or fuselage to minimize drag and maximize lift, called distributed propulsion. Likewise, supplemental battery power means conventional jet engines don’t have to be designed for maximum thrust, saving weight and boosting fuel efficiency.
By contrast, battery-powered electric motors and propellers can be small and light enough that they could be positioned at multiple locations, and their power source can be at another location in the airplane, connected by wires. Designers could choose wing shapes and propeller locations that minimize drag and maximize lift.
Even if it’s not possible to propel a plane entirely by battery, supplemental battery power could alleviate the need to design jet engines for maximum thrust. This would save weight and boost fuel efficiency.
“The electricity is always a means to an end. It’s never an end to itself,” Felder says. Electric propulsion “has fundamentally opened the design space. We don’t really know where it’s actually going to go. We just know that we have more options than we’ve ever had before.”
Next-generation batteries
For battery companies, such as SolidEnergy Systems in Waltham, Massachusetts, the initial goal is incremental improvement rather than a revolutionary breakthrough. SolidEnergy is developing a new class of batteries for drones that would combine the advantages of each of the two current types of aviation batteries.
Non-rechargeable lithium batteries must be discarded after they lose their charge. Often made of lithium thionyl chloride, their advantage is that they have high energy densities, says Qichao Hu, SolidEnergy’s chief executive. Other planes fly with rechargeable lithium ion batteries. These are heavier and lower energy density, but are attractive nonetheless. For one, they don’t have to be replaced after a single use, but even more importantly, they score high on another critical metric: Power density. That’s the term for how quickly a battery releases energy, something an airplane battery has to do fast for takeoffs and other high-speed applications.
New batteries developed by Hu’s company have both high energy density and power density. They can provide 500 watt-hours per kilogram, compared to 100 to 150 for rechargeable aviation batteries, Hu says. Lab tests show that the “new lithium metal batteries,” as the company calls them, can discharge their full power in 10 to 15 minutes, blisteringly quick compared to the 10 hours typical of primary batteries.
The difference is in the electrodes and the separator, or electrolyte, between the electrodes Hu explains. Inside a primary lithium battery, the anode or negative electrode consists of lithium, the lightest metal on the periodic table, which makes them lightweight and energy dense. In contrast, the anode in lithium ion batteries consists of a substitute for the lithium metal, typically a graphite or a graphite-silicon composite.
SolidEnergy’s new batteries are designed to have a thin layer of lithium metal as the negative electrode, and typically sulfur for the cathode, or positive side. The batteries can be recharged 100 to 300 times; Hu says they could triple the flight time of battery-powered drones.
Then there is the battery’s electrolyte, the material between the positive and negative electrodes. Lithium metal is very reactive, so designers need an electrolyte that is stable on lithium metal and also safe, which typically means it would have to be a solid material. But to maximize energy density, the electrolyte should be liquid. Making an electrolyte with solid and liquid properties was very challenging, says Hu, who declined to reveal how his company solved that problem, or what the electrolyte ingredients are in his new batteries.
Fundamental science dictates the ultimate limits for battery density. In theory, a battery could be created that used lithium, the lightest metal and therefore most energy-dense material that would work as an anode, and lithium oxygen — also called lithium air — from the atmosphere as the cathode, Hu says. Such a design would make the battery like a fuel cell or internal combustion engine. But the battery could never have the same energy density of a hydrocarbon fuel that is burned to release its energy, because a battery by definition leaves something behind for the next cycle.
One problem for a lithium oxygen battery is that moisture, carbon dioxide, nitrogen and other gases in the air would have to be separated from the oxygen. Another factor complicating the theoretical battery would be its solid conductive framework working with a liquid electrolyte and with a gas on the cathode side.
“If you want to have lithium metal, which is a very delicate, sensitive material, in contact with all of the junk in the air, then it’s just really hard to make that work,” Hu says. “Practically, there are a lot of technical challenges and even fundamental science limitations that are preventing this.”
Battery-aided design
Engineers anticipate batteries making a propulsion contribution along a continuum, from providing all or most of the power for small planes to contributing power in a hybrid arrangement for large planes.
Even today, currently available lithium batteries could power one-to-two-seat aircraft from 160 to 240 kilometers, which equates to about an hour of flight time, says NASA’s Felder. As an example, he cites the two-seat Alpha Electro, a trainer made by Pipistrel of Slovenia.
In the near future, battery powered airplanes will be popular in the one or two-seat recreational airplane market, particularly in Europe, where airports typically have to comply with community noise restrictions, predicts Stefan Gehrmann, managing director and founder of Air Energy of Aachen, Germany, a maker of lithium ion batteries for small planes and solar aircraft.
Felder calculates that in the near future batteries with improved energy densities of 300 to 400 watt-hours per kilogram could propel a nine-seat airplane for a flight of 280 to 370 kilometers.
For airplanes of all sizes, batteries could augment conventionally fueled generators that would supply electricity to motors that spin propellers. The batteries and a generator or generators could run simultaneously in a “range extender” setup. In this design, the generator would run constantly during flight, while the batteries would supply a small amount of power during cruise conditions and a larger amount during periods of flight that demand extra power, such as during takeoffs and landings.
In 2010, Boeing had batteries apply electric power to a turbine jet engine to help the engine spin the shaft attached to the fan that propelled the aircraft. The tests were conducted in the NASA-funded SUGAR Volt program. With this battery assistance, turbine designers can explore the possibility of shaving off the peak thrust requirements so the engine can be sized for cruise, where it spends most of its time, Felder says. Engines without battery assistance must be designed to deliver maximum thrust for takeoffs.
As the second year of follow-up studies to the SUGAR Volt study wrap up, researchers from UTRC, Pratt and Whitney, and Rolls Royce are finding that currently available batteries — at 200 watt hours per kilogram — can augment typical propulsion and save overall energy consumption for the aircraft, Felder says. Researchers are also running scenarios for peak-shaving, or using battery power to augment jet-fuel-fired engines at takeoff, with batteries that currently don’t exist — at 750 and 1000 watt-hours per kilogram.
But batteries show a diminishing return as airplanes get larger, with the limit for pure-electric battery powered aircraft at 9 to 19 seats with a 370-kilometer range. For airplanes in the 100- to 150-seat size range, batteries could augment traditionally fueled aircraft.
Airbus and Rolls Royce drew up the E-Airbus in 2013. E-Thrust would be powered by a single turbine engine driving an electric generator supplying electric power to six fans embedded in the wings. A large battery pack would act as the backup power supply — for flying the plane to safety if the turbine breaks down — as well as providing extra power needed for takeoff. As NASA’s Felder puts it: “If everything fails, you’re not a glider.”
For electric and hybrid-electric airplanes larger than the E-Thrust — in the Boeing 737-and-larger categories — batteries would play a support role, supplying up to 10 percent of the total energy required to power the airplane. Doing more would require a radical breakthrough in battery technology — a lithium air battery that immediately delivers the maximum energy and power densities possible with batteries, for example. But even for an electric airplane in which conventionally fueled turbine generators supplied the lion’s share of the propulsive power, batteries would have an important role. They would stabilize the power level in the electrical grid between generator and propeller motor power, like the function of a spring in a mechanical system. Without batteries and an electric controller, the grid would be rigid, which can lead to oversupply or undersupply of electric power and the harmful effects of brownouts or surges.
Batteries would play such a role in the N3-X, a 300-passenger, 80-megawatt, distributed propulsion, hybrid-electric airplane envisioned by Felder and other NASA aerospace engineers. They came up with the concept in 2012 by anticipating the technologies that would be available 15 years into the future, such as motors and generators with superconductor materials with virtually no electrical resistance. The N3-X would have a range, speed and capacity comparable to the Boeing 777-200LR.
If scientists were to achieve a radical breakthrough in battery technology — designing batteries with energy densities of 1,500 or 2,000 watt-hours per kilogram, for example — that would be high enough for aircraft designers to create new designs specifically to take advantage of the batteries, Felder says. Even though that energy density level still wouldn’t match jet fuel, battery-only airplanes could fly shorter flights — New York to St. Louis instead of New York to Los Angeles, for example. But at the 600 to 700 watt-hours per kilogram projections, the batteries aren’t capable of taking larger passenger aircraft very far on their own.
“As these technologies in batteries and motors and power electronics improve, they can play a role,” Felder says. “They may not be good enough for the N3-X 300-seat plane, but they might be good enough for a 50-seat regional. A little bit further on, and they might play a significant role in reducing fuel consumption in the 150-seat 737-class aircraft, which consume most of the aircraft fuel. If we can reduce fuel consumption there, then we take a bite out of the biggest segment of fuel use by all aircraft.”
NASA’s latest evolution of the N3-X concept — the STARC-ABL, for single-aisle turboelectric aircraft with aft boundary layer propulsion — has shown that with a single-aisle Class 800 737, with 150- to 180 passengers, a concept plane with partial turbo-electric propulsion can produce 7 percent to 12 percent fuel savings versus the same airplane with highly efficient typically fueled turbofans, Felder says. Even with advances in battery technology in the future, there is a barrier that technology advancements probably won’t be able to cross because energy density cannot increase beyond a certain ceiling.
“As you go bigger, I think batteries are going to become less of a central player and more of an adjunct, or support player,” Felder says.
Battery density has an ultimate density. In theory, a battery could be created that used lithium, the lightest metal and therefore most energy-dense material that would work as an anode, and lithium oxygen — also called lithium air — from the atmosphere as the cathode, Hu says. Such a design would make the battery like a fuel cell or internal combustion engine. But the battery could never have the same energy density as a hydrocarbon fuel that is burned to release its energy, because a battery by definition leaves something behind for the next cycle.
A factor complicating the theoretical battery would be its solid conductive framework working with a liquid electrolyte and with a gas on the cathode side.
“If you want to have lithium metal, which is a very delicate, sensitive material, in contact with all of the junk in the air, then it’s just really hard to make that work,” Hu says. “Practically, there are a lot of technical challenges and even fundamental science limitations that are preventing this.” ★
I don't think it was in any way a 'You're going in the wrong direction; you need to go in another direction.'
James Felder of NASA Glenn Research Center, on the impact of a National Academies report describing a limited near-term role for batteries in jetliner propulsion.

About Keith Button
Keith has written for C4ISR Journal and Hedge Fund Alert, where he broke news of the 2007 Bear Stearns hedge fund blowup that kicked off the global credit crisis. He is based in New York.
Related Posts
Stay Up to Date
Submit your email address to receive the latest industry and Aerospace America news.
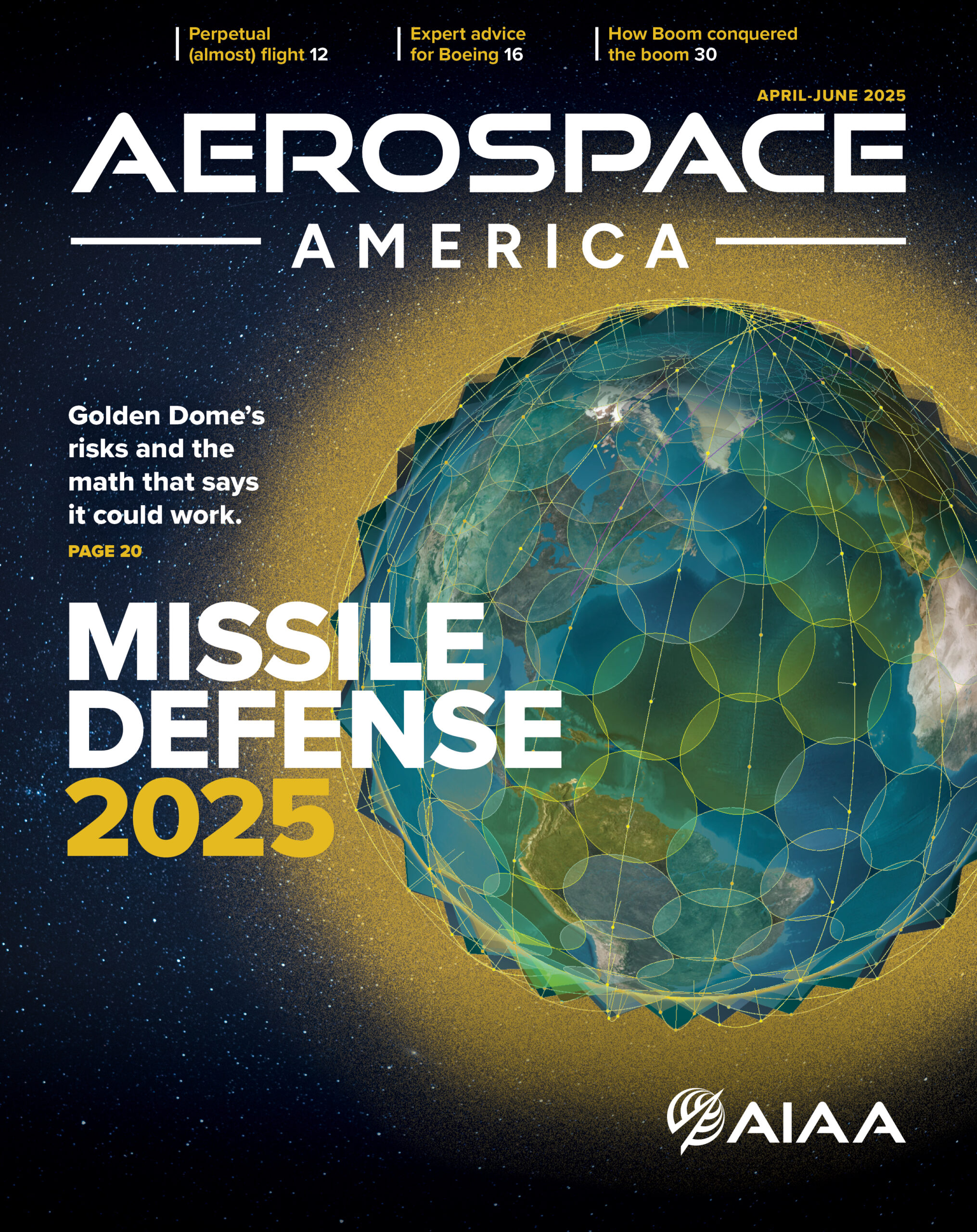
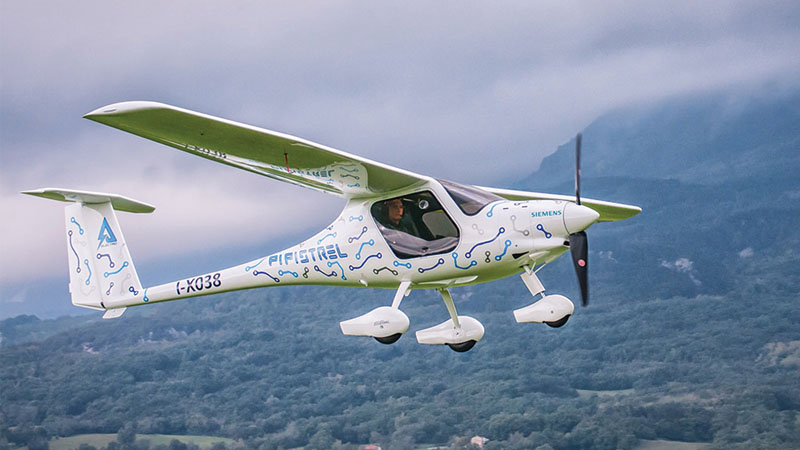

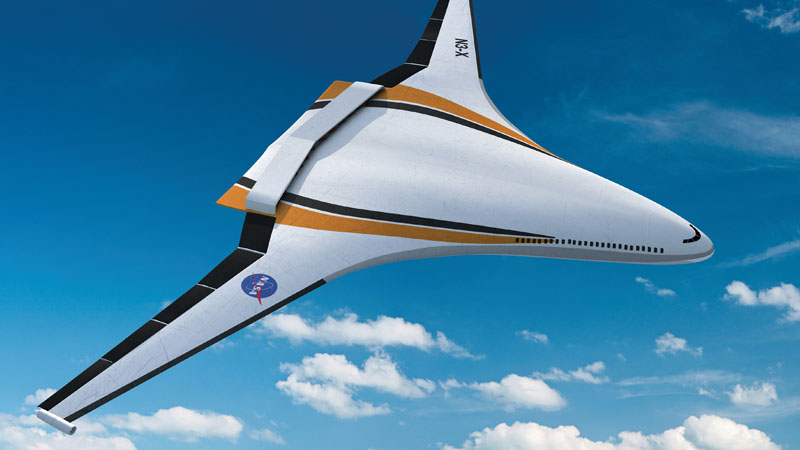
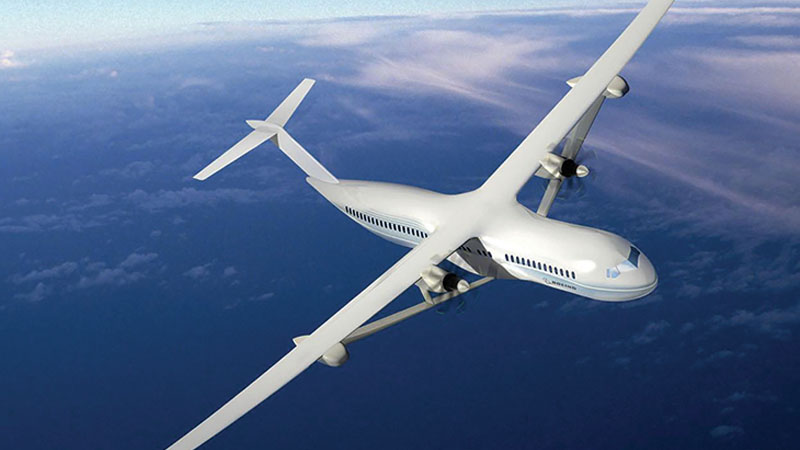
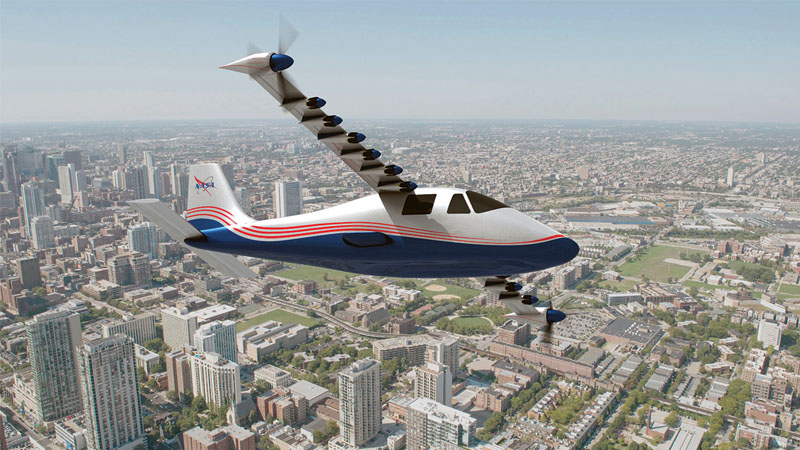