Stay Up to Date
Submit your email address to receive the latest industry and Aerospace America news.
Companies in the U.S. and abroad have big plans to extend the lives of existing multimillion-dollar geosynchronous satellites and equip new ones from the start for servicing. Standardization and regulatory bodies are figuring out how to make servicing a normal part of business. Karen Kwon has the story.
Only a few weeks into his new engineering job, Joe Anderson found himself at Intelsat’s then-Washington, D.C., headquarters, watching the screens in the primary operations center as astronauts from the space shuttle Endeavour conducted a series of spacewalks. The year was 1992, and two years earlier, the Intelsat VI F-3 communications satellite had become stuck in low-Earth orbit when the upper stage of its launch vehicle failed to release it. The only way to free the satellite from the upper stage was to jettison the kick motor that the upper stage was attached to. Intelsat did so, but now there was no way to boost it from LEO to geostationary transfer orbit, a waypoint en route to its planned geosynchronous orbit over the Atlantic Ocean.
This bad luck set up a bit of space history. Intelsat and NASA drew up an elaborate rescue plan for IS-603, as the satellite was later designated: Two spacewalking astronauts would grab the satellite and fasten a capture bar to the bottom of it, so that Endeavour’s robotic arm could then grab IS-603 and move it toward the orbiter’s open payload bay, where astronauts would attach the new kick motor.
It didn’t take long for that plan to go awry. One of the astronauts tried to stop the satellite’s spin to attach the bar, but the momentum of the liquid fuel spinning inside made that impossible. It took three astronauts to capture the rotating satellite and settle it, their commander quipping from his position at Endeavour’s flight deck, “Houston, I think we’ve got a satellite.” The new kick motor was attached, and the spacecraft arrived in GEO seven days later, happily hosting phone calls and routing television programming until its decommissioning in 2015.
Turn the calendar ahead three decades, and Anderson is among a cadre of executives in the space sector who aim to make servicing satellites a normal part of business that can be accomplished entirely robotically and without the drama of the IS-603 rescue. He now works at SpaceLogistics, a subsidiary of Northrop Grumman that plans to service satellites in GEO, which is home to approximately 550 satellites — about 50% of which Anderson estimates are healthy enough to justify, for example, extending their lives by taking over propulsion.
The effort is not just about near-term profits. Extending the lives of satellites reduces the “environmental impact of launching new platforms, mitigates the risks of failures in orbit and limits the amount of space debris,” Anderson says.
But if this is a revolution, it’s one that no single company can orchestrate or carry out alone. With so many satellites in GEO, one company won’t be able to handle the demand and variety of services needed. SpaceLogistics, for instance, is focused on extending the lives of satellites by taking over propulsion for them when they are nearly out of fuel. In contrast, Orbit Fab, a Colorado-based startup, plans to erect what it describes as gas stations in space to refuel GEO satellites. But keeping satellites operating will, in some cases, require more than refueling and restoring propulsion. It could require replacing a battery, supplementing electrical power or adding new software. To that end, DARPA’s Robotic Servicing of Geosynchronous Satellite program has contracted Space- Logistics to conduct multiple in-orbit demonstrations, slated to begin in 2025, to test dexterous servicing capabilities. Also, on top of this are a host of national security implications, given that corporations now plan to fly near to other satellites and even touch them.
SpaceLogistics has led the way on the propulsion part of the problem by conducting two life-extension missions, but it is far from alone in the field of in-space servicing, assembly and manufacturing, or ISAM. Astroscale, headquartered in Tokyo, in 2021 demonstrated a technique for removing debris from LEO, and it too plans to provide life-extension services. In fact, much of the ISAM effort to date has been focused on servicing, given that the technology is ready to be proven in space and there are lots of otherwise fully functioning satellites that are about to run out of fuel. These must either be serviced or moved to graveyard orbits before that happens.
At the SpaceLogistics headquarters in Dulles, Virginia, Anderson draws my attention to a computer screen showing the company’s technology roadmap. First comes “Life Extension Services,” marked as “today.” That’s a reference to the two life-extensions missions conducted so far: The first was begun in 2020 when a car-sized Mission Extension Vehicle rendezvoused with the IS-901 communications satellite. The MEV inserted a probe into the satellite’s liquid apogee engine nozzle, a class flown by 80% of GEO satellites, and once inside the nozzle throat it extended small fingers to hold the MEV in place, much like what a drywall anchor does to hold a heavy painting to a wall. The MEV then drew IS-901 up against a set of frame-like stanchions crafted to press against the ring that once held the client satellite to its launch vehicle. With the two firmly joined, the MEV turned on its solar- electric thrusters and shifted IS-901 back to its proper orbit. It will keep IS-901 there at least through 2025.
SpaceLogistics repeated the feat in 2021 by sending a second MEV that attached itself to IS-1002 to provide propulsion for at least five years from that date. These two satellites would otherwise have become space junk circling Earth in graveyard orbits. In the future, each MEV could be detached after five years, and each would have 10 more years of service life left for other clients.
The MEV concept, though, was just a start. Next on Anderson’s roadmap comes “Robotic Satellite Servicing” in 2024. Plans call for launching a new kind of spacecraft, a Mission Robotic Vehicle, that would grasp a prepositioned propulsion pod with one of its robotic arms and plug this dishwasher-sized unit into a client satellite, using a capture mechanism “evolved directly” from the blueprint for the two sent up in 2020 and 2021, Anderson explains. Each Mission Extension Pod’s electric thruster would take over propulsion for the client, but with a crucial difference from the MEV approach: Each would be light enough that the stanchions will not be necessary. The MRV would then release itself from the pod and go service another client.
Both designs completed their critical design reviews last year, and plans call for the MRV to be launched in 2024 with three MEPs. Under the terms of a February 2022 purchase agreement, an MRV will plug one of the MEPs into D3, a communications satellite operated by Optus of Australia.
SpaceLogistics, however, has more in mind than racking up a string of life extension missions. When I visited the Dulles headquarters in November, I saw gray cases in the Satellite Manufacturing Facility, where the MRV was getting ready to be assembled. The cases contained MRV modules sent from DARPA. The agency, under the 2020 agreement with SpaceLogistics, is providing two robotic arms and associated software for the MRV. In turn, SpaceLogistics must provide DARPA with information about how the automated robotic modules operate in space within three years of launch. These demonstrations will occur “in conjunction” with the MRV servicing commercial satellites, including the D3, “or during quiescent times in their servicing manifest,” RSGS program manager Ana Saplan told me by email.

But for new satellites to be serviced, they must be designed from the start with that in mind — not just by SpaceLogistics, but by other companies as well.
In the Rendezvous, Proximity, Operations and Docking Lab, which is overlooked by two giant robot arms used for testing docking operations, Anderson shows me a plastic mockup of an interface device that could be the solution. It’s a rectangular plate and about the size of a laptop computer, with various shapes protruding from it. One of them looks like the nozzle of a liquid apogee engine that the MEP and MRV are designed to latch onto. By installing a standard plate like this during manufacturing, spacecraft builders would ensure their satellite is serviceable by SpaceLogistics even if it does not have a liquid apogee engine, given that builders are shifting away from them toward electric propulsion. The other shapes include a passive refueling port, which would allow a servicer to hook up a valve and refuel the client vehicle.
Soon, the mockup will become a real part of satellites. One will be installed on the MRV, so that the MRV itself could be refueled if needed. Another will be on an unspecified U.S. Space Force satellite, which will be used in an operational mission, according to Anderson.
Anderson emphasizes that, even though Northrop Grumman and SpaceLogistics designed the plate, it will be an “open interface” that others can use. “This is not going to be a Northrop Grumman proprietary only used for our spacecraft,” Anderson says. “The idea is we want all of the industry to be compatible with the same interface so that others could provide refueling, for example, to the spacecraft.”
Of course, “Whether it becomes an industry standard or not will depend on the level of adoption by end users,” he wrote in a follow-up email.
Creating standards
Overall, a vibrant competition of ideas is underway. But those in the ISAM field worry that if competing technologies aren’t introduced in an organized manner, the result will be rampant incompatibility and a risk of miscalculations by the militaries of spacefaring nations over the intentions of these commercial players.
DARPA was among the first to see this, and in 2017 it created the Consortium for Execution of Rendezvous and Servicing Operations, or Confers, whose 60 member organizations in the U.S. and abroad include SpaceLogistics, Orbit Fab and Astroscale. Confers drafted and proposed recommendations about the functions for the refueling interface that newly constructed satellites should have, and those recommendations were submitted last year to the AIAA Committee on Standards for On-Orbit Servicing and Assembly. As of early March, the AIAA standard was scheduled to be made public for a review in about a month, committee chair Fred Slane told me via email.
Imagine pulling your car up to a gas station and realizing that you cannot fill up because the gas nozzles in the station are not compatible with your car’s fuel tank, says Brian Weeden, the executive director of Confers and an executive at the Secure World Foundation, a D.C.-based group whose mission includes space sustainability.
“That would be a much more inefficient system.” Or, on the data side of things, “What if there were 35 different USB ports, and you had to figure out what specific thing your computer had and look for the specific dongle for your camera or speakers?” Weeden adds.
Should specific equipment be required in exchange for a license to operate the satellite and launch from the host nation’s territory? “I don’t think there’s any reason for a government to say ‘You must carry a refueling port,’ ‘You must carry an electronics interface,’” says Gordon Roesler, the former manager who created DARPA’s robotic servicing program. “Because some people will see that as valuable to their business case, and some people won’t.”
So, whether a satellite should have certain equipment or not should be determined by the market demand, he adds.
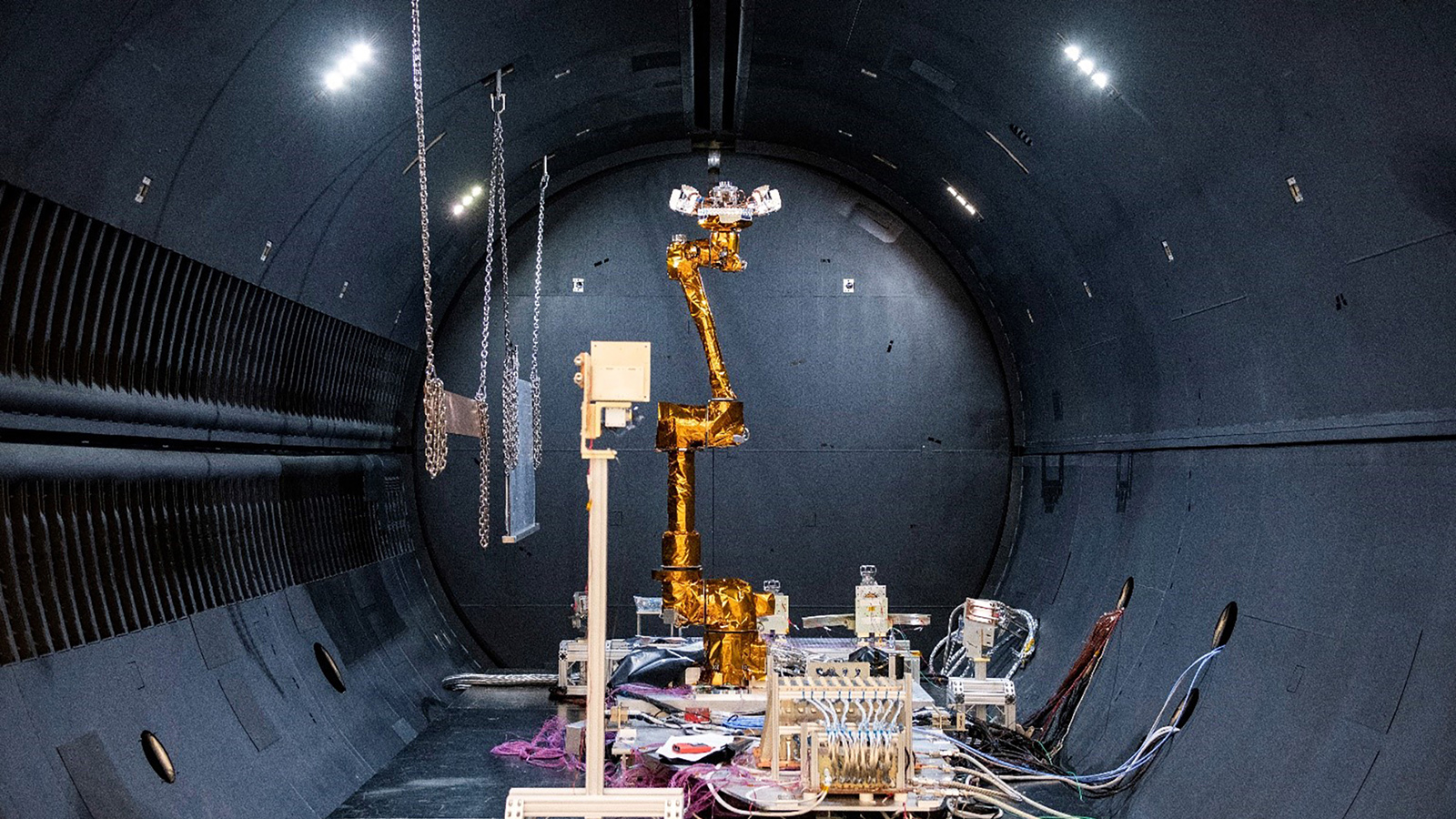
So far, the biggest achievement by Confers is earning the International Organization for Standardization’s approval of ISO 24330, a set of guiding principles and best practices for the servicing industry, published in July. Given that rendezvous and grappling technologies have military implications, ISO 24330 recommends that a service provider always seeks permission before approaching another space vehicle. It also defines various terminologies such as “client space object” and “servicing space object” because there hasn’t been a common vocabulary among companies and governments.
ISO 24330 was significant for more than what it says: “This was agreed to by the governments,” Weeden says. “So not just the companies, but the governments that were involved in this committee. We’re talking U.S., Canada, France, Italy, Germany, Russia, China, Brazil. They’ve all agreed to this as well.”
The emphasis on setting norms of behavior was driven by a desire to prevent actions that could unwittingly increase the risk of miscalculation by another nation’s military. Kaitlyn Johnson of the Center for Strategic and International Studies in, D.C. refers to the first episode of the Netflix show “Space Force,” which depicts a Chinese satellite approaching an American satellite, extending a robot arm and cutting off its solar panels.
“Obviously, that’s very dramatic and not actually what would happen,” she says, but with technological development, a satellite could have the capability to “physically disrupt that other satellite in the case of a conflict.”
A less physical example she gives: a satellite with a jamming capability approaching another one to disrupt communications.
Most often, hostile intent cannot be determined with absolute certainty until something happens, Johnson says. Take the case of Shijian-17, a satellite with a robotic arm designed and built by the China Academy of Space Technology. Launched in 2016, its purpose remains a a topic of debate among space watchers, though its developer says it is an experimental satellite that offers communication and broadcast service. When Shijian-17 arrived on GEO, it changed its direction multiple times, instead of staying put in one geosynchronous location. As a result, it came in close proximity to 10 satellites within the span of a little over four years — highly unusual behavior for a spacecraft in GEO at that time, but one that sounds not unlike what SpaceLogistics plans for its MRV. The difference? Today, ISO 24330’s transparency recommendation is in place.
The ISO standard is not a legal mandate, but setting guidelines and getting countries to sign on is still a good thing, says Anderson. Now, whenever some entity performs a space activity that is considered out of line, others have the agreement to point to. Also, various regulators of different countries can refer to the international standard when forming their own regulatory framework on satellite servicing, he adds.
Regulatory decisions?
The U.S. currently lacks a regulatory framework for satellite servicing, but perhaps not for long. The White House in April 2022 released the “In-Space Servicing, Assembly, and Manufacturing National Strategy,” which signaled to the rest of the U.S. government that it should focus on the ISAM industry moving forward, says Weeden.
While the U.S. government continues to explore how it wants to provide oversight regarding ISAM, SpaceLogistics is forging ahead with its plan, assembling its MRV and MEP as scheduled, knowing that operating licenses must still be acquired for the spacecraft.
As of now, it is unclear whether SpaceLogistics will have to follow the same licensing procedure for the MRV as it did for the MEV spacecraft, and whether a government agency — and if so, which one — will hold the regulatory authority over the MRV, along with other types of “novel space activities” such as asteroid mining and debris removal. The National Space Council led by Vice President Kamala Harris, per its charter, held three listening sessions between November and December to discuss how those activities should be regulated. As of mid-March, the council had not released a decision.
According to Anderson, MEV’s use of its on-board camera was licensed through NOAA, which is in charge of licensing remote sensing satellites, and the Federal Communications Commission licensed the vehicle’s communications to and from space. But because the MRV may perform up to five missions per year on different satellites — unlike the MEV, which remains docked to a client satellite for several years — the U.S. government may need to rethink its strategy.
SpaceLogistics has started talking to the relevant parties within the U.S. government, Anderson says, but it doesn’t expect to receive a license to operate the MRV until the end of 2023. For now, the company is forging ahead with development, which will follow a typical design and standard engineering processes.
While there is no direct connection between Anderson’s work during the IS-603 rescue and his current role, “there certainly were lessons learned from that mission,” he says. At the top of his mind are the need to be ready for the unexpected and the awareness of how sensitive the dynamics of objects are in space when touched by any disturbance. In that sense, his work on MEV, MRV and MEP represents a full-circle moment for his career, and a moment that also gives a glimpse of how governments and corporations might yet learn to operate their spacecraft in an environmentally sustainable manner.

About Karen Kwon
Karen is a science journalist based in the Washington, D.C., area, and is the associate editor of Optics & Photonics News. She holds a doctorate in chemistry from Columbia University and previously wrote about physics, space science and technology for Scientific American.
Related Posts
Stay Up to Date
Submit your email address to receive the latest industry and Aerospace America news.
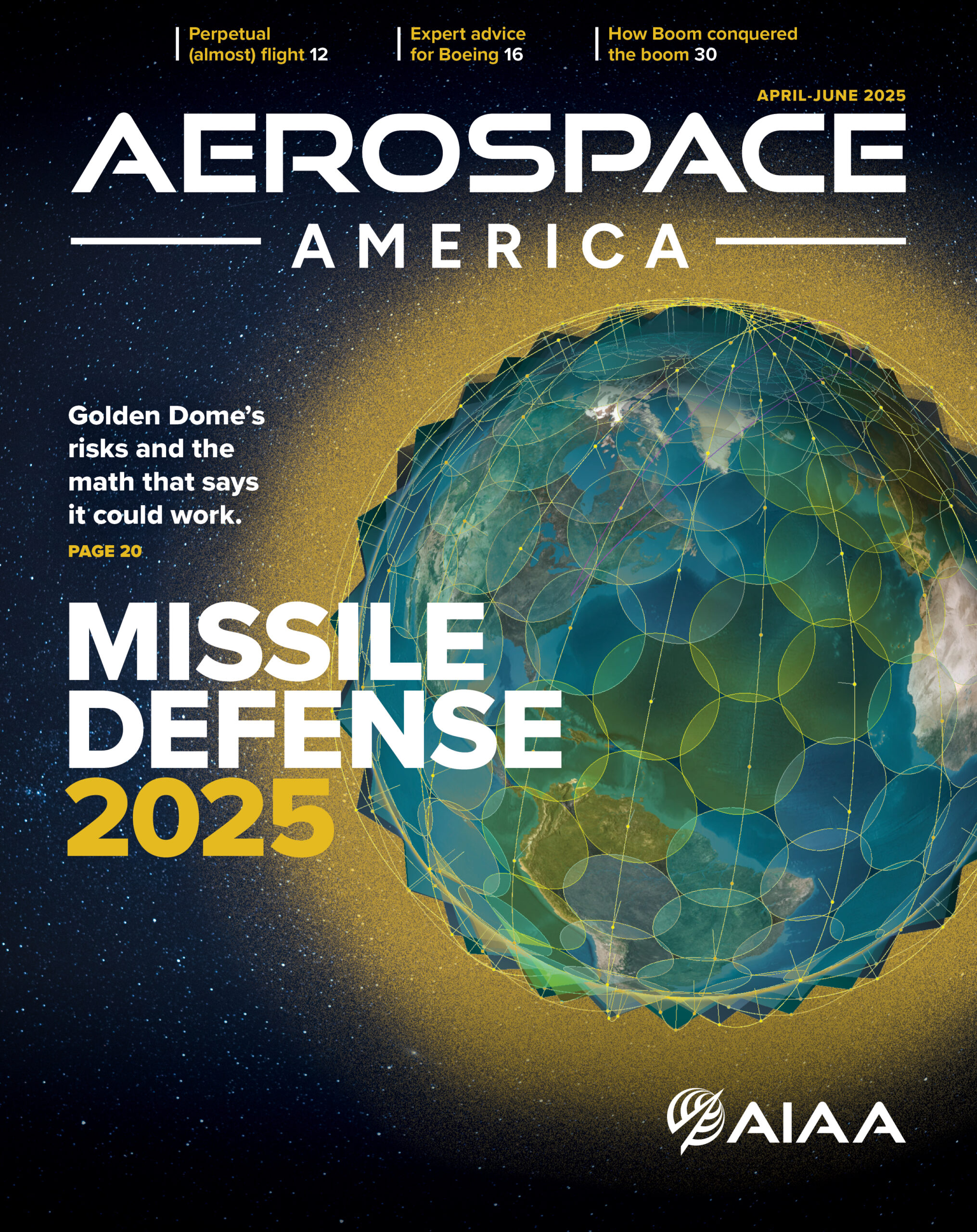