Stay Up to Date
Submit your email address to receive the latest industry and Aerospace America news.
With their ability to manipulate their surroundings, morph, bend and change color, our planet’s creatures and plants outperform our sophisticated flying machines in some respects. Though long intrigued by this reality, aircraft engineers have yet to fully plumb biology for design inspiration. This is set to change, and Jan Tegler shows us how.
British engineer and inventor Frederick Lanchester spent his afternoons during an 1892 voyage to the United States watching herring gulls gliding on rising air, their wings barely moving but curling up at the ends to help them stay aloft. Further studies of the birds led to his 1897 patent for an aerial machine that never flew but would have had “capping planes” rising from its wing tips to capture the airflow off the end of each tip and add lift.
It took until the 1970s and a spike in oil prices for something resembling Lanchester’s concept to be incorporated into commercial airliners and other planes. Today we know them as winglets, the near-vertical wing extensions that improve aircraft fuel efficiency and range.
Now, however, “we’re on the verge of a big acceleration” in bio-inspired design in aerospace, predicts Thomas Koonce, who manages the Revolutionary Technology Portfolio of Lockheed Martin Skunk Works in California. Why does he think so? Because of the advent of artificial intelligence and deep machine learning, he says.
Here are four biologically inspired innovations that are part of that acceleration:
Learning from Hercules beetles
Lockheed Martin Skunk Works has taken note of the amazing ability of the hand-sized Hercules beetles of tropical Central and South America to automatically darken or lighten to match the daily shifting hue of the surrounding rainforest whose colors look deeper in humid conditions than drier ones.
The secret to this camouflaging lies in each beetle’s multilayered forewings that fold up to form the beetle’s hard outer layer. A translucent, spongy yellow layer is sandwiched between a transparent outer layer and a black base layer. In dry conditions, pores in the yellow layer hold only air, and ambient light reflects yellow from this layer’s structure. As humidity rises, the pores fill with water, and now the black layer becomes visible.
Researchers at Skunk Works think something like this tactic could improve manufacturing of composite aircraft parts. They want to create “attritable sensors that could alert technicians to when a complex structure is at the right level of humidity to move on to the next step of the manufacturing process,” says Thomas Koonce, who manages the Skunk Works’ Revolutionary Technology Portfolio.
If the humidity is too high, the part could cure with weak areas or blisters, forcing it to be scrapped. “Color change sensors would be a fast, inexpensive, reliable way of determining whether or not the conditions are correct for manufacturing,” Koonce says. Instead of attaching electronic sensors and then interpreting the data, technicians could simply look at a color change sticker that would signal whether a part is ready for the next step. “It’s a low-cost, low-manpower solution,” he says.
Skunk Works is famous for its pioneering work on radar stealth, so could the company have in mind visual stealth? Koonce says only that the technology would be applicable “to a wide variety of vehicles including aircraft and spacecraft” but that it’s at a low stage of readiness and there’s no specific nonmanufacturing application for it “that Lockheed Martin can share at this time.”
Morphing surfaces edge toward “mainstream”
Pondering one of nature’s most common wonders some years ago, Sridhar Kota, a professor of mechanical engineering at the University of Michigan, had an epiphany. “Most anything that people have designed in engineering is strong but also stiff,” he recalls thinking.
“Things in nature are strong and flexible, like tree branches. Why can’t we design things to be strong and flexible?”
So began a 20-year effort by Kota and colleagues to develop aircraft flight control surfaces that would bend and twist, potentially replacing traditional stiff control surfaces articulated by hinges that induce drag and harm fuel economy.
Kota founded FlexSys Inc. in 2000 to develop these “morphing” control surfaces whose shape would be changed by adjusting the positions of aluminum or, in some versions, composite beams beneath the surface. The boldest test yet will come if the U.S. Air Force moves forward with plans to test the technology on the wings of a KC-135 refueling tanker under a $5 million program called ALACS, short for Active Load Alleviation Control Surface.
An earlier version of the morphing technology performed “beautifully” as a replacement for the standard flaps on a NASA Gulfstream III jet between 2014 and 2017, Kota says. The morphing flaps improved fuel efficiency by an estimated 3% to 4%.
That said, their direct fuel efficiency contribution is not the biggest reason the Air Force wants to try the morphing surfaces on KC-135s. The Air Force has long wanted to add winglets to its fuel-thirsty tankers to generate additional lift and improve fuel efficiency. That hasn’t been possible due to the aerodynamic forces that the winglets would impart onto the wings when the aircraft climbs, descends or banks. Tantalizingly, NASA proved this potential benefit when it fitted a KC-135 with them and flew it in 1979 and 1980, demonstrating an increase in range of up to 7% during cruise, when maneuver loading is not a worry.
Enter the FlexSys technology. Plans call for equipping each wing of a KC-135 with what Kota calls a “load alleviation surface” measuring 140 centimeters outboard of each wing’s aileron. Internally, electric motors would move aluminum beams to bend the surface upward, counteracting the maneuver loading. The latest design is much like the flaps tested on the Gulfstream III except that on the KC-135, electric motors would extend or retract arms to curl the load alleviation control surfaces up or down, whereas on the Gulfstream III that was accomplished with hydraulic cylinders. Also, the beams in the Gulfstream III flaps were composite, not aluminum. As with the Gulfstream III, the beams would be geometrically arranged to evenly distribute loading, keeping strain low across the structure, preserving its ability to withstand aerodynamic load.
On any aircraft, the surfaces can “act as one continuous surface,” Kota says, eliminating drag from seams or hinges. Flexible, articulating transition surfaces that unfold like hand fans keep the fixed parts of the wing connected to the shape morphing control surface.
He calls the concept distributed compliance, and although tree branches inspired the idea, he likes to compare it to the mechanics of a bow and arrow. “You pull back on the bow string and bend the entire bow or beam,” Kota explains. “That’s what the structure of our morphing control surfaces is like.”
As for the KC-135 flights, engineers have so far completed a design-data gathering phase and a ground test phase. If funding is approved, a KC-135R from the Utah Air National Guard’s 151st Air Refueling Wing would be modified for a series of test flights in 2022 to assess the load alleviation control surface and winglet combination. Modeling shows a 5.5% gain in fuel efficiency that could increase range and flight time, Kota says.
The KC-135 effort “represents a first step in getting flight crews comfortable with the idea of flying with morphing control surfaces, a first foray into making morphing mainstream.”
Taming sonic booms with a little help from penguins
On land, emperor penguins walk with a wobbling gait, occasionally falling down and scooting comically on their bellies over Antarctic ice and snow. But in the water, each “performs like a champion,” says Isaiah Blankson, a senior technologist at NASA’s Glenn Research Center in Ohio. They dive, turn and climb with graceful agility, catching prey and dodging predators.
Blankson first learned how emperor penguins swim so acrobatically during his studies of drag reduction in 1968. The knowledge stuck with him while working on NASA’s ongoing Low-Boom Flight Demonstration program aimed at diminishing sonic booms with aerodynamic shaping.
When he left the program in 2018, Blankson began research on an alternative approach to boom reduction. Instead of shaping an aircraft to delay the formation of supersonic shock waves that pile up on an aircraft’s nose and tail section, he wants to weaken or eliminate the waves that would otherwise form around the aircraft and do this by firing rapid pulses of laser in front of the aircraft. The rapid conversion of air to plasma should create primary and secondary waves that continually inhibit the formation of the bow shock waves that normally cause sonic booms that reach the ground.
“The result is that the local flow behaves as if it is subsonic instead of supersonic,” Blankson explains.
Believe it or not, this idea, called forward energy deposition, was loosely inspired by the strategy emperor penguins evolved to swim so effortlessly. When one dives into the water, thousands of tiny air bubbles trapped in its feathery coat are released. The bubbles combine with the water, creating a bubbly air-water mixture that encases the penguins’ body, “effectively breaking down the water flowing around the penguins’ bodies into a less-dense, lower-drag medium,” Blankson says.
Instead of releasing bubbles, Blankson would install a laser on the nose of a supersonic aircraft and fire pulses of laser tens of meters ahead of the aircaft. Firing them at millisecond rates would create a streak of plasma, called a filament, whose length would depend on the power of the laser, Blankson explains.
The concept is still at “the exploratory stage,” Blankson says. So far, he has created plasmas by firing a laser beam from the side of a supersonic wind tunnel in front of a long cylinder mounted in the tunnel. “We create a spot of plasma that hangs in the air, and you are almost tempted to touch it with your finger.”
Challenges to overcome include determining the optimal geometric pattern for laser pulses and timing the pulses to prevent shock waves from reforming. Also crucial would be scaling lasers with low system mass and weight and the right amount of power for use on a real airplane. Blankson is also investigating supplementary energy sources to produce and intensify plasmas and prolong their effects on shock waves.
Plans for testing forward energy deposition outside the lab ultimately include flying a scaled-up laser. That would be done on NASA’s F-15B at Armstrong Research Center in California, Blankson says.
“The F-15 has tremendous amounts of electrical power that can be used for this type of experiment, and we’re doing joint research with Armstrong Research Center that will eventually lead to a laser that can be tested in flight on the F-15.”
Harbor seal whiskers inspire turbine blades
Vikram Shyam, a researcher in the turbomachinery and heat transfer branch at NASA’s Glenn Research Center in Ohio, is designing low-drag turbine blades inspired by the whiskers of harbor seals. His research is part of NASA’s Advanced Air Transport Technology Project, an effort to develop revolutionary energy efficiency for fixed-wing aircraft.
Harbor seal whiskers loosely resemble ripe bean pods. They have bulges, and their edges are wavy. This way, the whiskers “produce much smaller wakes and significantly lower turbulence and drag than smooth whiskers,” Shyam says. This keeps the whiskers relatively still while the animal swims, so the whiskers can pick up the small vibrations and wakes crayfish create in murky Arctic waters.
Shyam’s small team of researchers began mapping the parameters of harbor seal whiskers eight years ago and created enlarged 3D plastic models for testing in Glenn’s low-speed wind tunnel with the goal of developing turbine blades that would draw air into the turbine stage of future hybrid-electric jet engines with less drag than those today, a change that could dramatically improve fuel efficiency and lower emissions.
The wind tunnel tests confirmed that, just as in the water, the whiskers’ bulges and zigzagging edges help keep the flow attached to their surfaces. The peaks, valleys and waviness create low-pressure paths for airflow to follow along the whisker shape, Shyam says, keeping the flow “from separating and creating drag.”
Turbine blades with similar bulges and zigzags at their leading and trailing edges could also reduce drag, enabling them to spin with less energy. That would be beneficial for hybrid-electric jet engines that pair a conventional turbine jet engine with a fan driven by an electric motor. In this configuration, the jet engine provides thrust but also transfers power to the electric motor to spin the fan and create additional thrust. Delivering power to the electric motor requires the engine to operate over a wide range of power settings, causing its turbine blades to spin at faster and slower speeds than blades in a conventional jet engine that operates over a smaller rpm range.
Think of each blade as an airfoil or wing. Like a wing, turbine blades are shaped to function best at specific angles relative to onrushing air. Spinning the blades faster or slower than the rpm range they are shaped for can change the angle at which each blade meets the air by enough to cause airflow to separate from them. Separated airflow produces less thrust for a given amount of fuel than smooth air and limits the range of power settings a jet engine can operate at.
Comparing models of smooth turbine blades to blades with bulges and wavy edges, Shyam’s team found that the bio-inspired shape can reduce drag, enabling turbine blades to operate efficiently at a wide range of speeds, potentially improving thrust output and decreasing fuel consumption.
But the shape for the whisker-inspired turbine blades will require fine-tuning, Shyam notes, explaining that unlike a harbor seal whisker, which has bulges over its entire surface, turbine blades must have bulges on one side only.
That’s because the blades must have a low-pressure side like the top side of a wing and a high-pressure side like the bottom of a wing to produce lift as the mixture of air and combustion exhaust rushes over the blades. This “lift is what makes the blades spin to generate power,” Shyam explains. “One of the changes we made was ensuring that the lift side of the blades did not carry those undulations.”
Modeling of turbine blades with bulges and zigzags at their trailing edges has also shown that “the waviness can reduce noise compared to smooth baseline blades because the shape produces less turbulence,” Shyam says.
Shyam’s team is now focused on translating its results into a 3D harbor seal whisker-inspired design for testing in simulated environments as close to realistic as possible over the next five years.
Could harbor seal-inspired blades become a reality by the end of the decade? Shyam says it’s possible. “The end result might not look like the seal whisker but will be three-dimensional, and it will include the waviness.”
When an emperor penguin dives into the water, thousands of tiny air bubbles trapped in its feathery coat are released. The bubbles combine with the water, creating a bubbly air-water mixture that encases the penguins’ body, “effectively breaking down the water flowing around the penguins’ bodies into a less-dense, lower-drag medium.”
Isaiah Blankson, NASA

About Jan Tegler
Jan covers a variety of subjects, including defense, for publications internationally. He’s a frequent contributor to Defense Media Network/Faircount Media Group and is the author of the book “B-47 Stratojet: Boeing’s Brilliant Bomber,” as well as a general aviation pilot.
Related Posts
Stay Up to Date
Submit your email address to receive the latest industry and Aerospace America news.
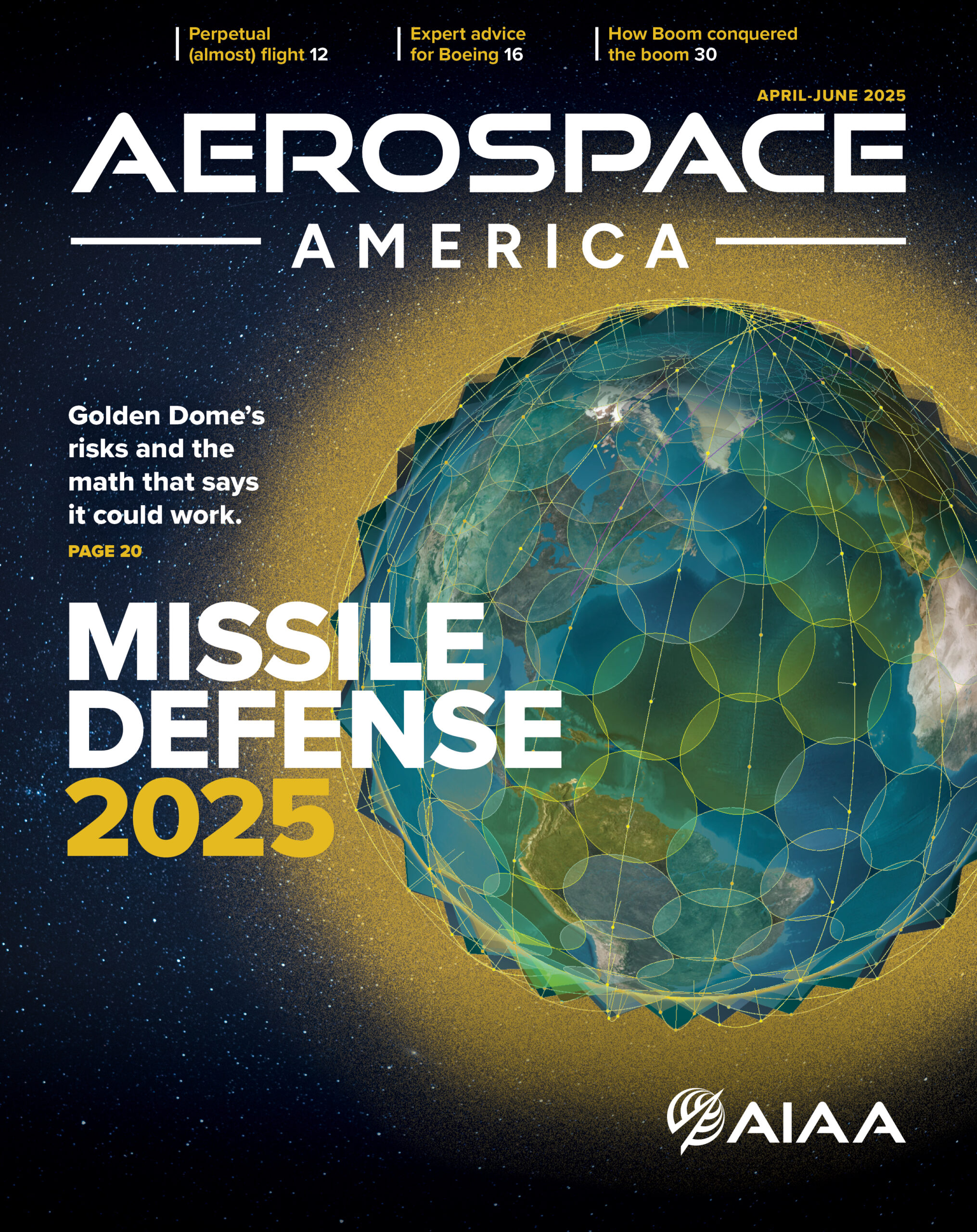

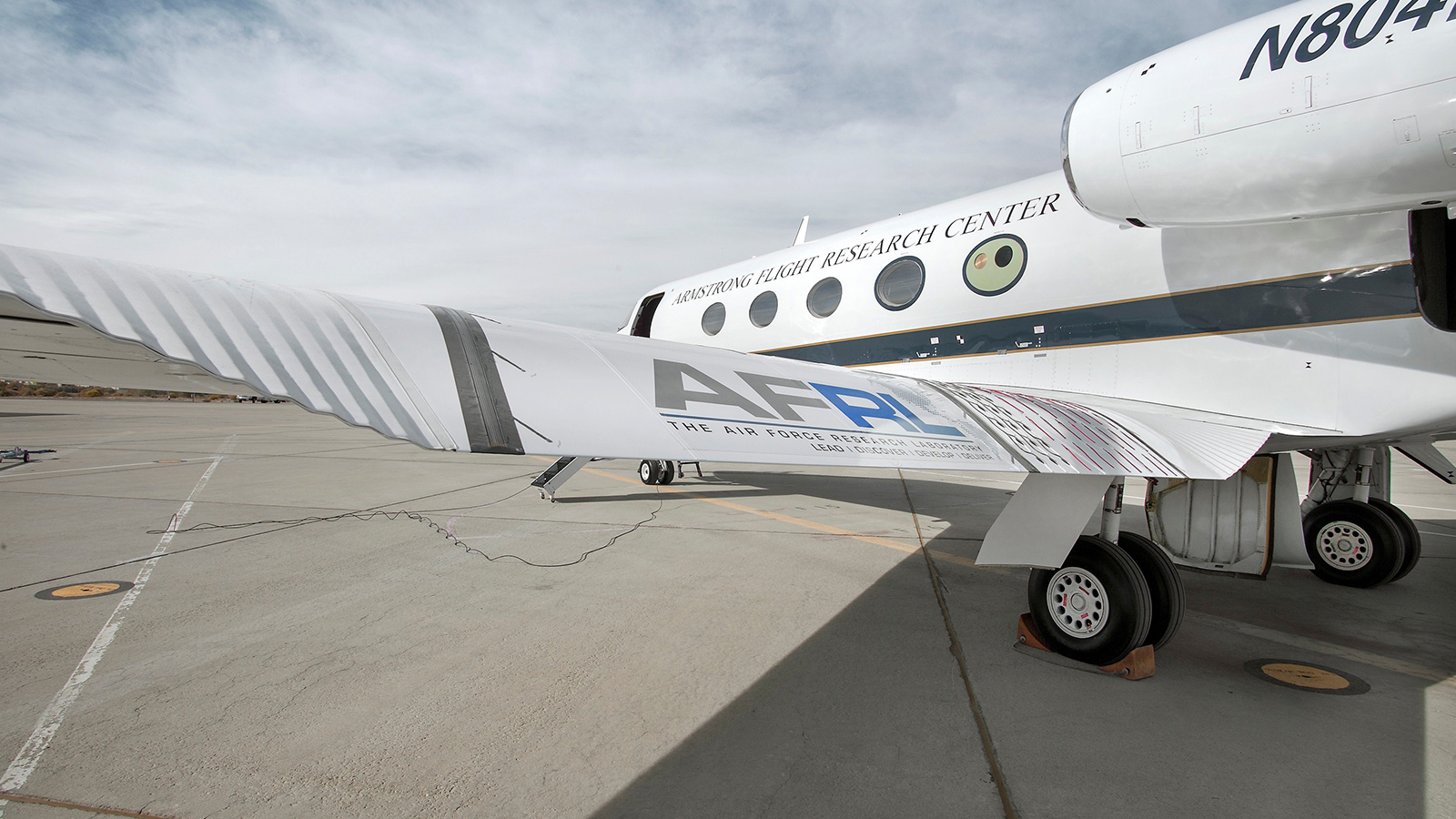
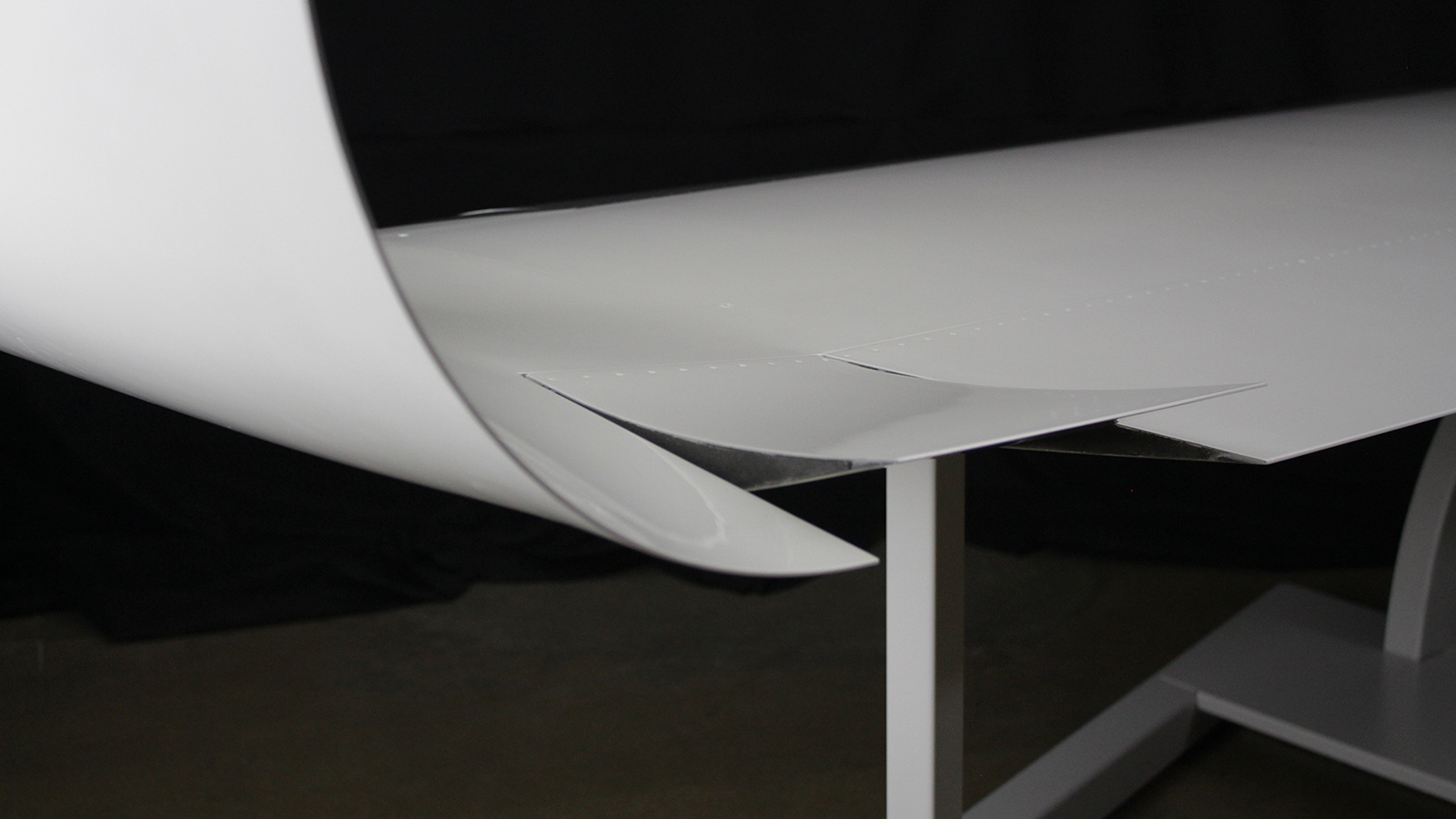
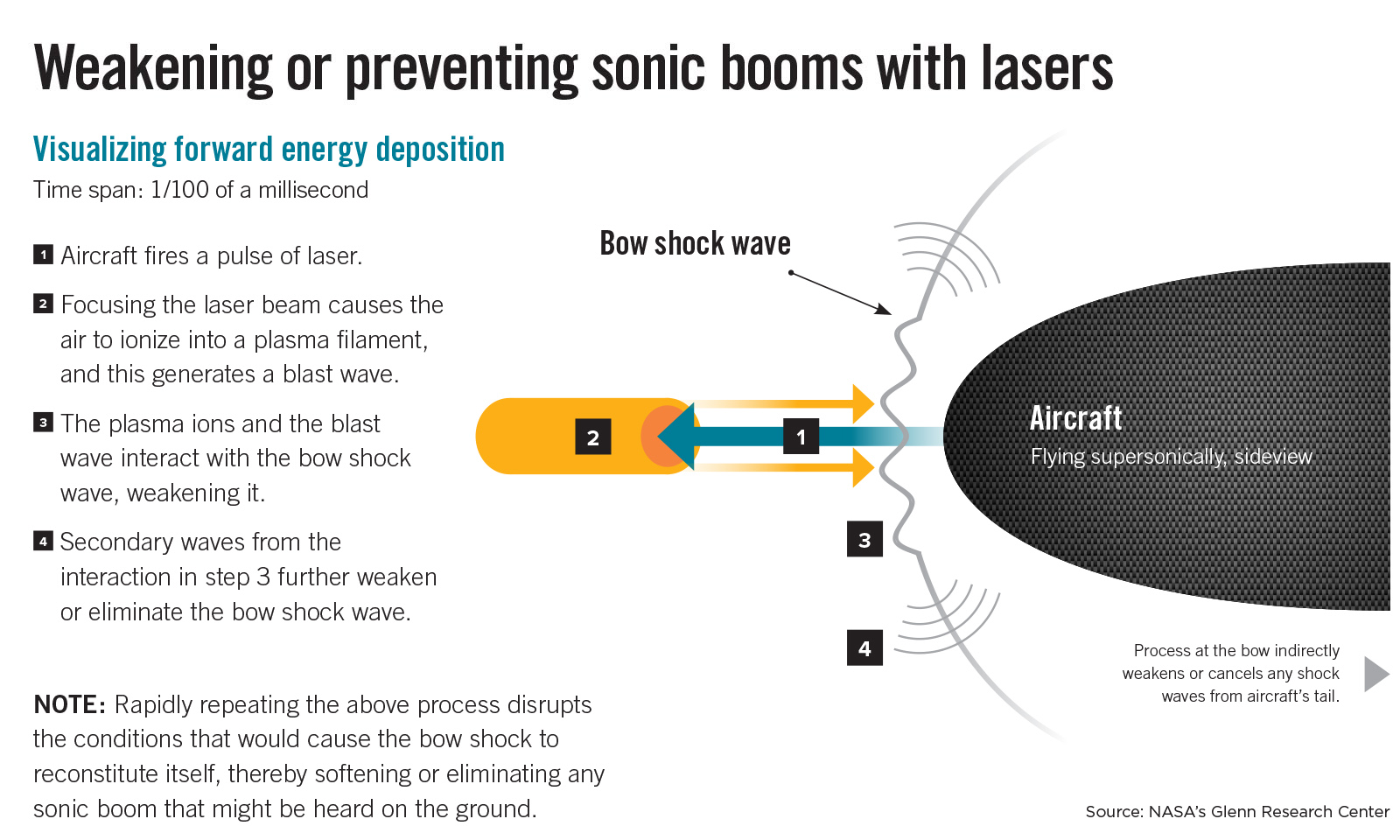
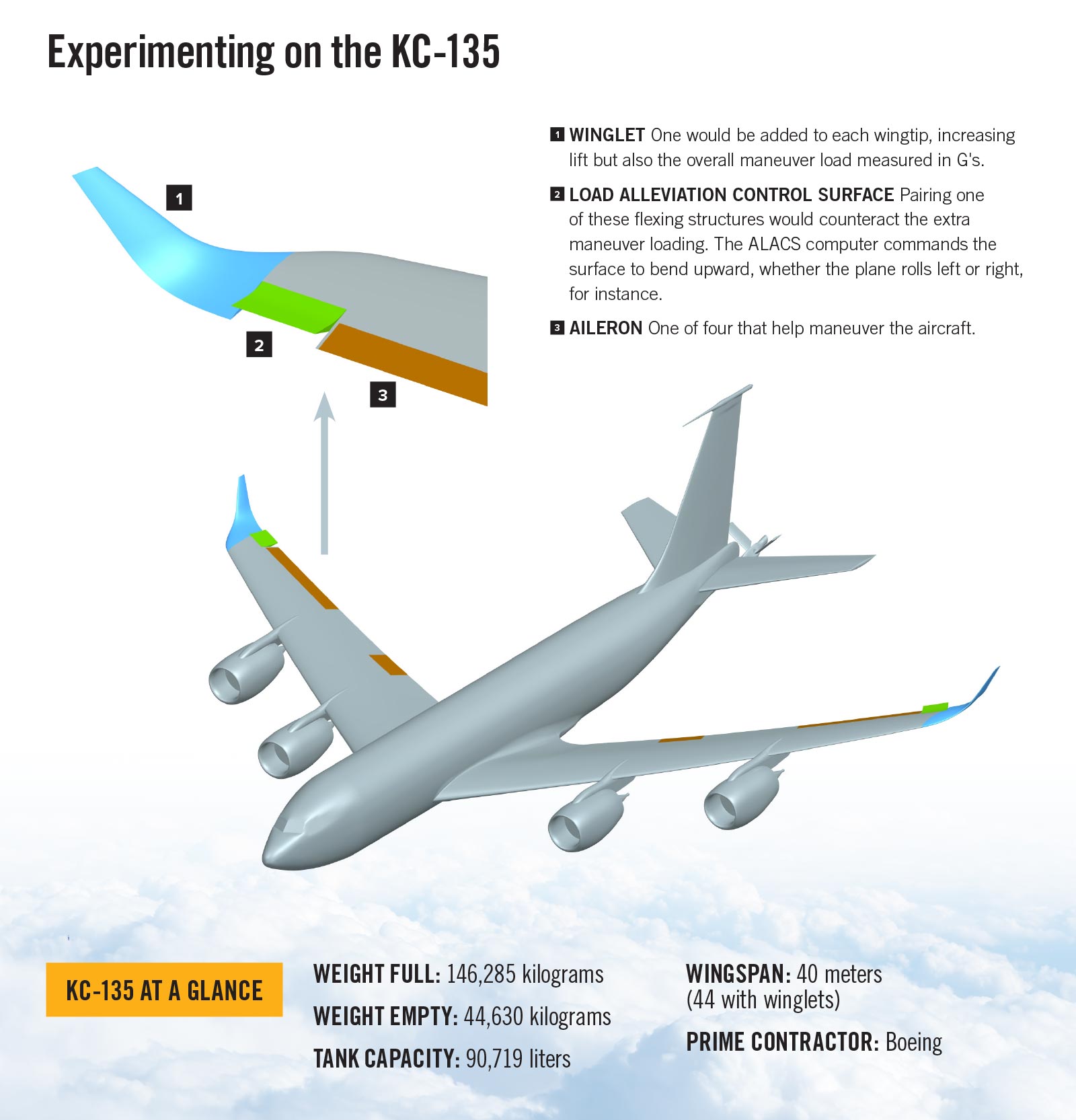
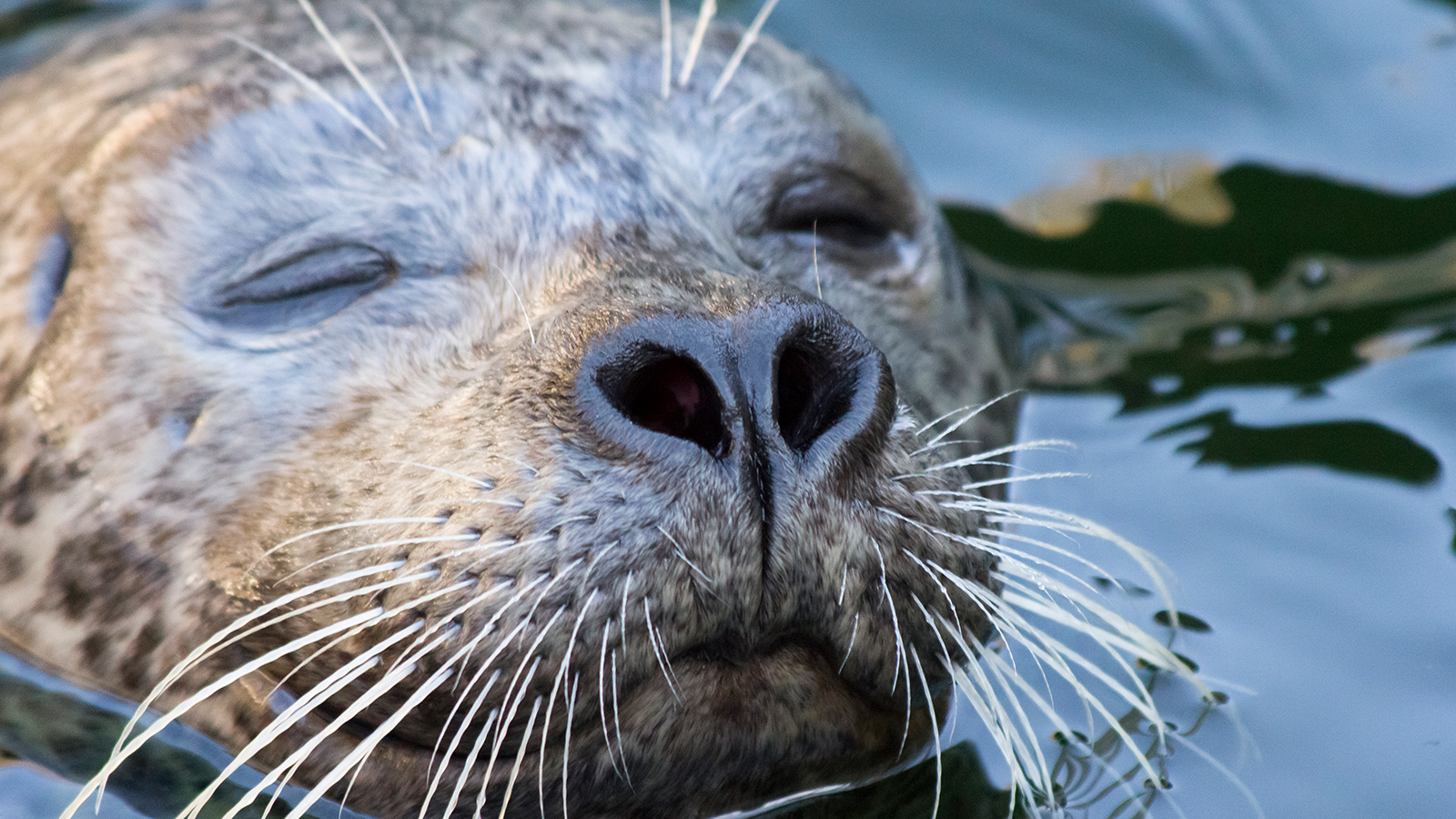
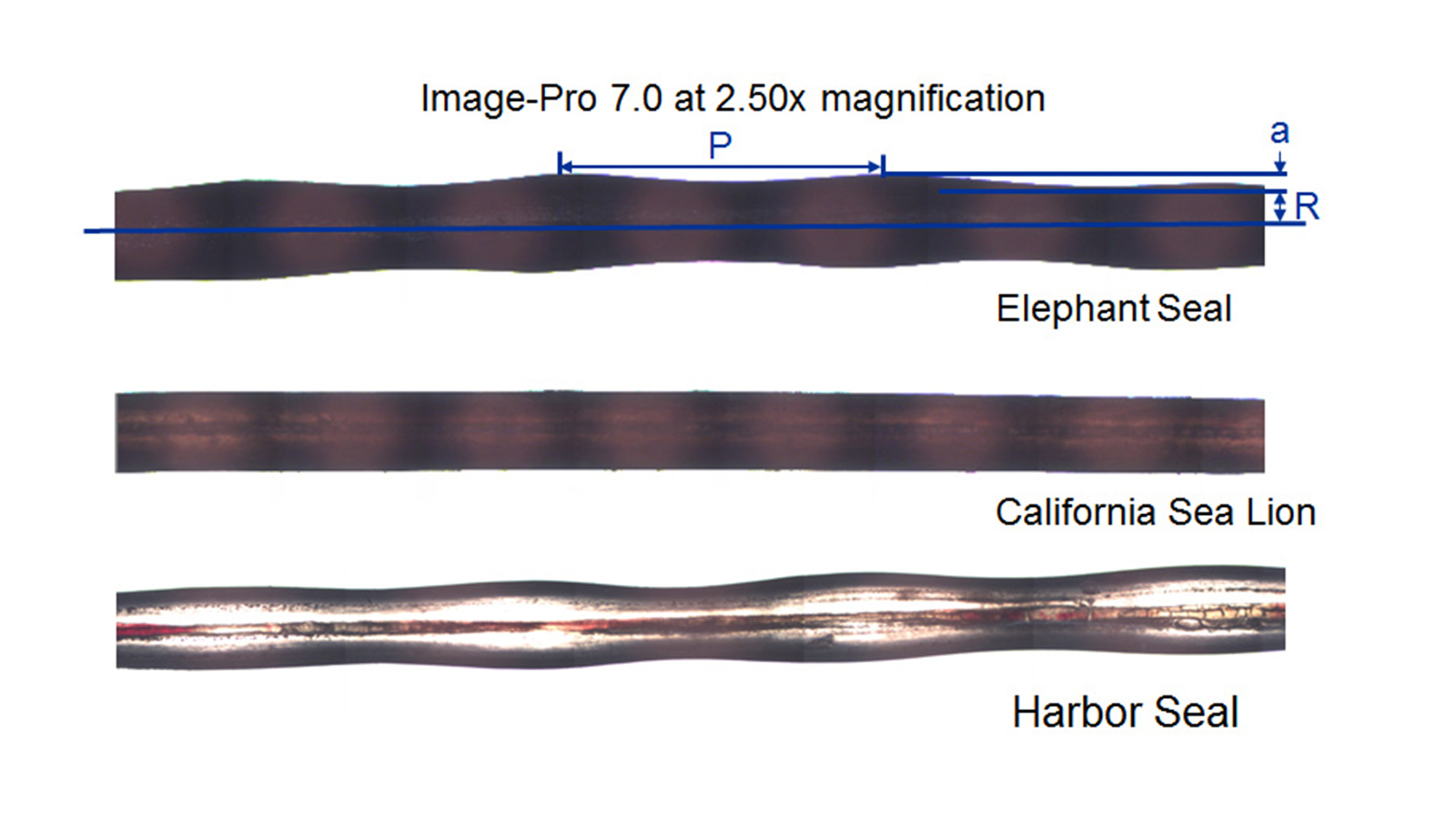
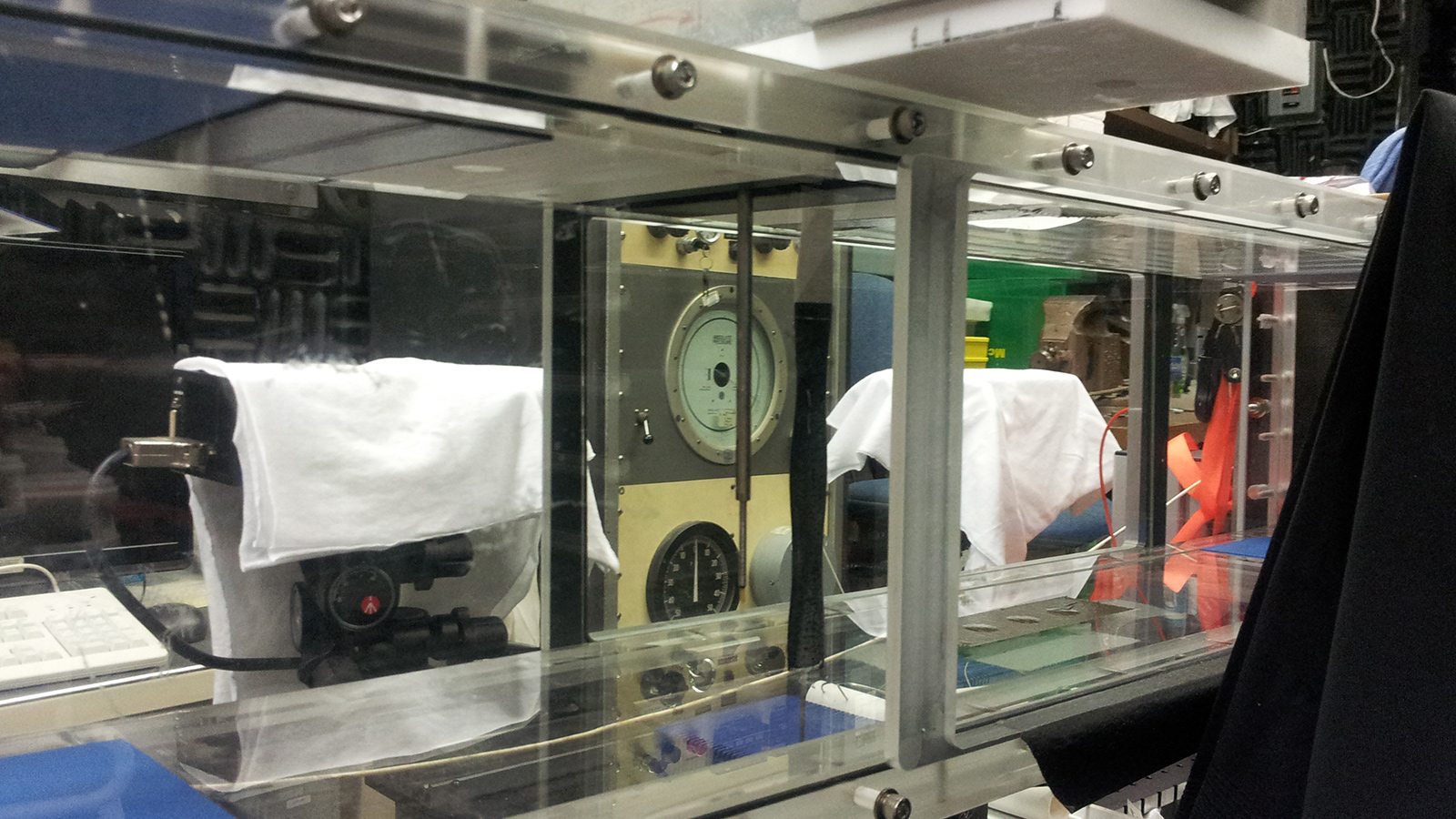
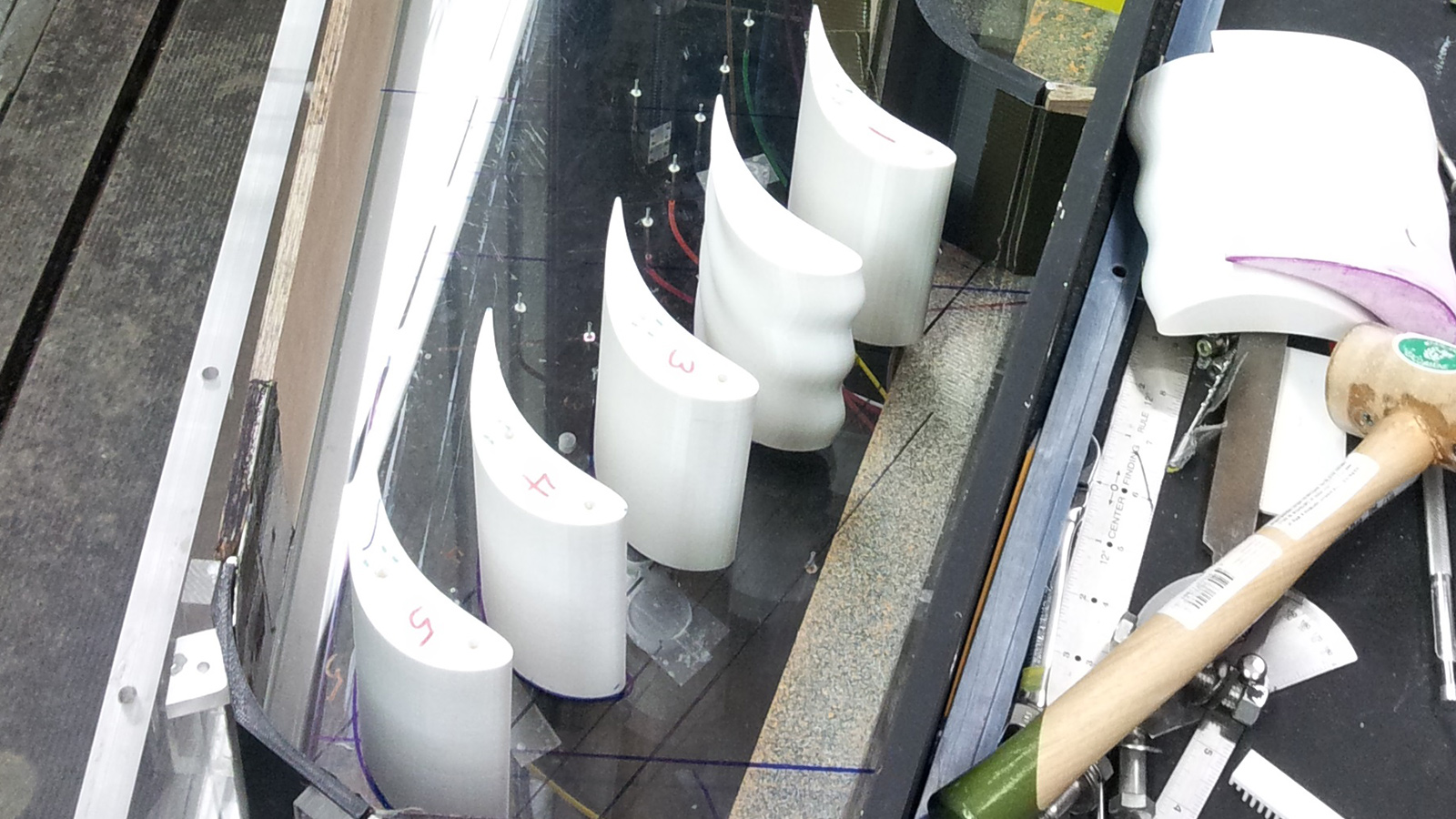