Stay Up to Date
Submit your email address to receive the latest industry and Aerospace America news.
The next version of NASA’s expendable Space Launch System rockets will likely rely on adhesive film rather than metal fixtures to join sections of composite in parts of the structure. Keith Button tells us how engineers earned the trust of designers to incorporate the technique into rockets that will carry astronauts.
Managers of NASA’s Space Launch System program made a bold decision in 2018 after reviewing engineering reports about progress in the Composite Technologies for Exploration project, a multi-field-center effort to reduce the weight of future space vehicles by joining composite panels with epoxy film adhesive rather than metal fixtures.
They would begin the process of incorporating the bonded-joint technique into the SLS design as an alternative to bolts and plates starting with the fourth in the line of multibillion-dollar expendable rockets, the one that would send astronauts to the Lunar Gateway, a planned stopover point for astronauts on their way to the moon’s surface. This rocket will be the first of the larger SLS Block 1B design, which includes a cargo carrier called the Universal Stage Adapter (USA) and a Payload Attach Fitting (PAF) inside it to hold cargo firmly in place during launch. Managers were looking for places to save weight to carry more payload, and the 2018 decision to embrace bonded joints was an outcome of this USA Mass Opportunities study. The new technology will be applied to each of these components, pending a critical design review scheduled for them in June.
This is the story of how a team of NASA composite engineers won the confidence of those in charge of NASA’s most expensive program to start the process of adopting a technology that promises to reduce the mass of rocket joints by 87%.
“We were ecstatic to learn that the work that we had done was relevant and convincing to the flight project,” says Ken Segal, design and analysis co-lead for the CTE project. “As we go to explore the moon and Mars, we need to have lighter-weight structures,” which means spacecraft can either carry more supplies and experiments or burn less fuel.
Trusting bonded joints in rockets with people aboard will be a major step. Bolted joints have a tried and true record in the industry, but the confidence of spacecraft designers in bonded joints has lagged. There was scant testing data proving that bonded joints were no riskier than traditional ones, and the reliability of digital tools that attempted to predict the strength of a bonded joint design was unknown.
That’s the crux of the problem the team of 12 engineers at multiple field centers set out to solve.
The right joints
One of the first challenges was to choose which kind of bonded joints to create representative versions of for modeling and testing in the lab at different scales. Ideally these would be the most worthy candidates to show the world the benefits of bonded joints.
The review started with every type of joint that had been employed or possibly could be employed for a space mission. They considered bonded and bolted joints, thinking that a bonded equivalent might be created for the bolted version. They then narrowed the list based on factors such as whether the joint could be easily reproduced and analyzed, the cost of building the joint, its mass, and its expected strength and resistance to damage.
The field was narrowed to two bonded configurations that could be alternatives to the traditional bolted metal joints on SLS. One was a double-lap bonded joint that could join curved panels of composite to form the Universal Stage Adapter, which will be made by Dynetics in Decatur, Alabama, and the Payload Attach Fitting, which NASA will make in house at Marshall Space Flight Center in nearby Huntsville. The other joint, which has not been adopted by the SLS program, was a circumferential joint that could in theory attach the PAF to a ring and to the rest of the rocket.
In the conventional double-lap joint that the initial blueprints for Block 1B called for, two panels consisting of honeycombed aluminum sandwiched between layers of composite fiber were to be butted together. Strips of metal would protect this seam on both sides, and these strips would be through-bolted to bind them with the two panels. For the representative bonded joints, the configuration was similar, but without bolts or metal plates. Such joints rely on composite strips covering both sides of their seams, and a film of adhesive bonding the strips to the panels.
For the traditional circumferential joint, a metal ring would be bolted to a cut-off-cone composite structure, which is the shape of the Payload Attach Fitting. The ring in a cross-section view looks like a squared-off C with a sideways Pi symbol on the back of the C. The base edge of the cone fits into the slot created by the upward-angled legs of the sideways Pi. In the bonded joint version, the ring and its Pi-shaped fitting would be made of 3D-woven carbon composite — strengthened by both horizontally and vertically woven fibers — and be bonded to the conical structure with film adhesive instead of bolts.
Damage assessment
With the two kinds of joints identified, the engineers needed a method for measuring damage inside the joints when stress is applied. These damage measurements would form a real-world baseline for judging the accuracy of the computer models that designers must rely on when deciding whether a particular kind of joint is resilient enough to incorporate in a blueprint ahead of construction and testing.
The strength, durability and weight of bonded joints depends on the type of composite materials and adhesive, the configuration of the joint and how the joint is built and cured. That variety makes it difficult to digitally predict when a particular design of bonded joint would fail. “You can see how this gets complicated,” Segal says.
To solve this predictability problem, the engineers applied a building-blocks approach: Start by testing the strength of small pieces — 2.5 by 25 centimeters, for example — of the carbon composite material that the representative bonded joints were to be built from. Then test small scaled-down versions of the joints, and then larger and larger scaled-down joints.
They conducted just over 1,000 tests during the five-year program that ended in October, and enough by 2018 for NASA to feel confident enough to begin incorporating the bonded joints in the SLS 1B design. They stretched, compressed and broke scaled-down versions of the representative bonded joints ranging in size from 15 by 20 cm to 91 by 152 cm. Engineers at NASA’s Goddard Space Flight Center in Maryland built the smaller scaled-down joints for the tests and engineers at NASA Marshall built the larger scaled-down joints.
Commercially available computer modeling programs were selected, as well as programs developed at NASA, to analyze strength and predict failure points for the scaled-down joints. Then physical tests were conducted to find out which software created the most accurate predictions of failure strength when forces are applied from different directions. They needed accurate predictions for how much energy it took to break the joints by pulling them apart (tensile strength), pushing them together (compression strength) or tearing them apart (shear strength). They also tested joints for strain — how the joints stretched or deformed before they failed.
To pinpoint where the joints were failing as they broke apart, a variety of measurement methods were employed. Foil strain gauges were bonded to the surface of the joints, typically 0.5-by-1-cm wide. A white paint with a black speckled pattern was sprayed on the surface of the joints and then the specks were tracked with a digital camera, a method called digital image correlation.
The joint strain and damage were also measured with X-ray computed tomography. To measure strain, for example, the engineers clamped a scaled-down joint at both ends and activated a hydraulic piston to push the two clamps apart to apply strain, then they unclamped the joint and placed it in an X-ray chamber to take images. Then they put the joint back in the clamped test frame to apply more strain, X-rayed it again, and repeated the process over and over until the joint broke, to record how and where cracks develop under the surface. They also pinpointed damage under the surface with thumbtack-shaped acoustic sensors that they glued to the surface of the test joints: The sensors could hear when fibers popped or resin cracked, and these sounds could be plotted to locate where the cracks then occurred. And they employed a sound measurement method where ultrasonic pulses were directed into the joint and a computer program located cracks and other defects based on how quickly the pulses reflected back.
The predicted results from the computer models were compared to the actual results of their tests, then they updated and improved the computer models by feeding the actual test results back into the models. Some of the computer models were accurate to within 2% of the actual results, which was considered excellent, Segal says, and most of the computer predictions were within 10% of the actual results. Some were accurate to within only 50% — these were the predictions for 3D-woven composites, which are relatively new to the composites world.
“We haven’t gotten as good using those [digital] tools” for modeling 3D-woven composites, Segal says. “The tools might be good enough; we don’t know. Sometimes it’s not the tool, but the analytical process that you use.”
Weight watching
The engineers calculated that a full-scale configuration of their representative double-lap bonded joints — eight panels joined by eight joints — would weigh 19 kilograms compared to 150 k for the bolted-metal-strips version. And just 40 parts would be required, rather than the 2,116 in the bolted version.
For a representative circumferential joint, at full size — about 8 meters in diameter — they calculated that the bonded version would weigh 168 k less than the bolted version.
But the weight savings could not come at the cost of additional risk compared to the redundancy provided by bolts.
“If you lose one bolt, you still have thousands of other bolts,” Segal says. “But if your bond line breaks, there’s potentially nothing to stop it. You need to demonstrate that it is worthy and trustworthy.” For the CTE project, for example, the engineers tested their representative joints extensively after hitting them with a hammer to damage them, and the joints were still stronger than their design limit.
“We showed that you could make these joints; you could hit them, and impact them, and cause damage to them, and they still could meet the strength requirements,” Segal says. “I’m pretty sure that that’s part of the reason that SLS made the switch.”
Besides showing which computer models worked best for predicting bonded joint failure, the CTE project improved the failure prediction ability of computer models. Those models could be employed by designers of bonded joints for airplanes as well as spacecraft. Test data were also generated that NASA can share with outside researchers, and already some universities are working with the 3D-woven composites data for their own research.
“We generate this data and we want people to work with it,” says Segal.
Debuting bonded joints
NASA set out to trim weight from the design of the Space Launch System’s coming cargo carrier, the Universal Stage Adapter, so it could carry more payload. Pending design reviews, the components below will now be formed by joining panels of composite with adhesive, rather than metal fixtures.
“We showed that you could make these joints; you could hit them, and impact them, and cause damage to them, and they still could meet the strength requirements.”
Ken Segal, Composite Technologies for Exploration project

About Keith Button
Keith has written for C4ISR Journal and Hedge Fund Alert, where he broke news of the 2007 Bear Stearns hedge fund blowup that kicked off the global credit crisis. He is based in New York.
Related Posts
Stay Up to Date
Submit your email address to receive the latest industry and Aerospace America news.
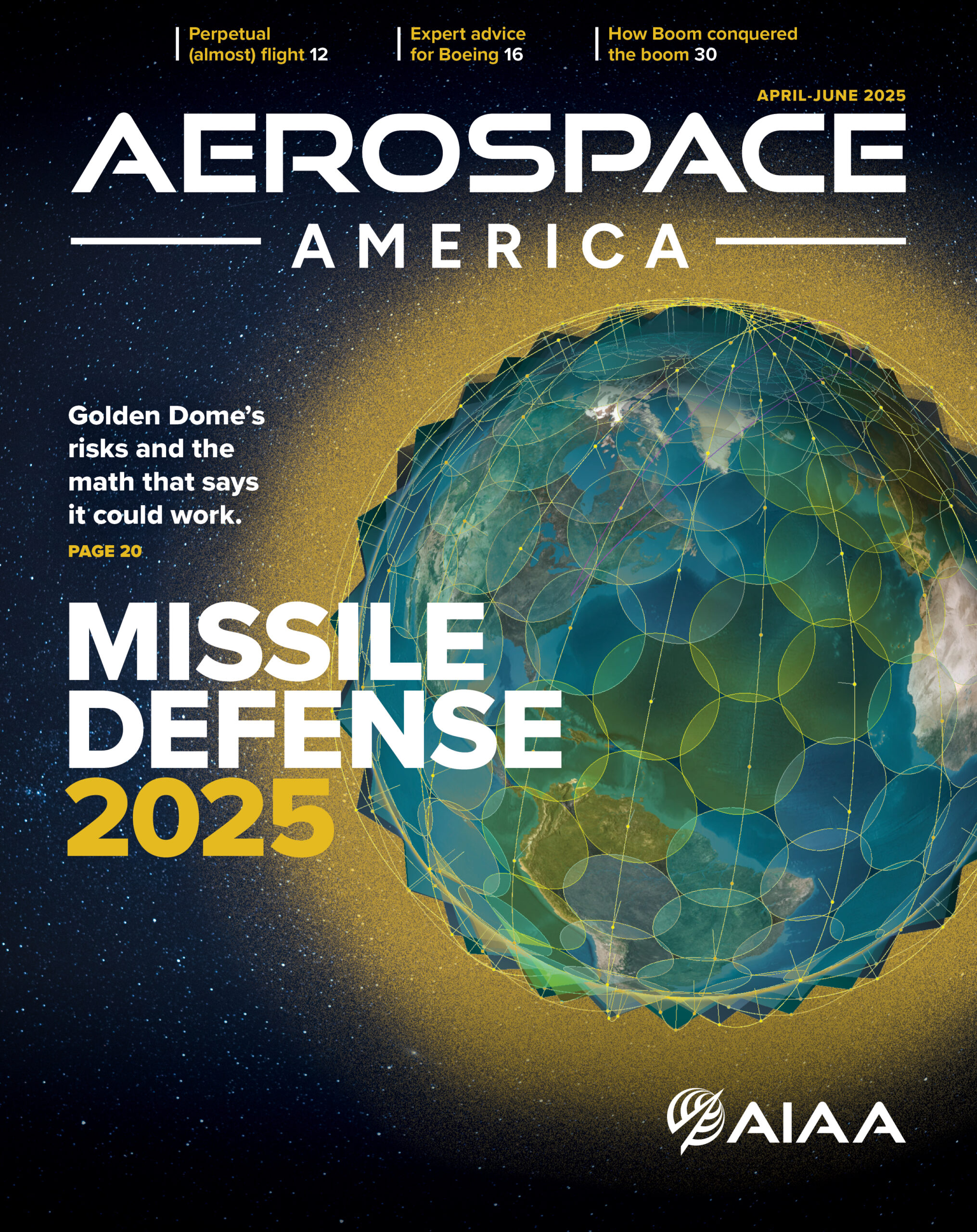