Stay Up to Date
Submit your email address to receive the latest industry and Aerospace America news.
Carbon nanotubes, the long cylindrical molecules that have enthralled engineers with their strength, also happen to conduct electricity that can produce heat. Keith Button spoke to MIT researchers who want to tap this characteristic to change the way aircraft structures are made.
Aerospace engineers at the Massachusetts Institute of Technology have devised a method for curing aircraft composite materials by incorporating carbon nanotube molecules in them and electrifying them to generate heat.
Normally, composite wings, fuselages and other components must be heated for hours in ovens to solidify them into shape. With the out-of-oven process, the MIT team has “demonstrated that we can bake the cake in one hour, as opposed to three hours,” says Brian Wardle, the MIT professor who leads the research team.
So far, only small patches of materials have been cured, but if the method can be scaled up and proven for a wide range of materials and shapes, then airplane manufacturers could adopt the technique to speed up their processes and reduce energy costs.
The new technique came to the engineers through serendipity. In 2010, MIT and Metis Design Corp., a Boston aerospace company headed by Seth Kessler, a colleague of Wardle’s, started a project for the U.S. Navy. MIT and Metis designed and built an embedded wing de-icer for unmanned Triton aircraft, the Navy’s maritime surveillance drones.
For this de-icer, the engineers knew that carbon nanotubes, the long carbon molecules thousands of times thinner than a human hair, conduct electricity well. Feeding electricity to them could warm the aircraft’s wings and melt ice or keep it from building up. They applied thin, black sheets of nanotubes to the leading edge of a composite wing as they fabricated it. Then the whole unit was cured in an oven.
To prove the technique, they fed electrical current to the sheets through electrodes. The sheets conducted the electricity to other electrodes to complete the circuit and produce ice-melting heat. Dozens of ice tunnel tests have been run on the de-icer, but it hasn’t been fielded yet, Kessler says.
The engineers had an epiphany from this experience: “Why can’t we use that heat to actually do the manufacturing?” Wardle recalls the team wondering.
Wings with benefits
Incorporating carbon nanotube heaters into the manufacturing of carbon fiber reinforced plastics could have some immediate benefits for airplane builders, Wardle says. They wouldn’t need giant ovens to contain large wings or fuselages. And because the nanotubes heat up immediately when electric current is applied, the manufacturers wouldn’t have to wait hours for the air or gas inside an oven to heat up.
Once the planes are built, pilots, mechanics and airplane operators could benefit from carbon nanotubes baked into wings and other airplane structures. The nanotubes might measure strain or structural damage, for example. As a strain gauge, bending or twisting the carbon nanotube mesh would cause the resistance of electric current passing through the nanotubes to change: Tension would increase resistance and compression would decrease it. A sensor could discern that change and measure strain on the wing, says Lawrence Drzal, a professor and director of the Composite Materials and Structures Center at Michigan State University in East Lansing, Michigan. He is not involved in the MIT research but is aware of it. For structural damage, a sensor could pick up on permanent changes in the electric current passing through the carbon nanotubes when connections are removed between them because of damage to the wing. Carbon nanotubes might also offer lightning protection to the skin of an aircraft, diffusing the energy of a strike, Drzal says.
Testing the concept
In 2012, the engineers began a series of experiments to see if the heat from electrified sheets of nanotubes would be enough to cure composites. “In a sense, a lot of the really hard stuff was already worked out from the prior technology,” Wardle says, referring to the de-icing work. For the Navy drones, the engineers had figured out issues like how and where to place electrodes to best control the heating. They had also worked out how much the sheets of nanotubes could be bent or folded over and still create heat as required.
Now, they decided to test the nanotube heating on the thermoset carbon-reinforced plastics that some airplane wings and fuselages are made from.
To test their curing technique on this material, the engineers needed to make their own sheets of carbon nanotubes that conducted electricity well. The nanotubes on these sheets had to be dense, aligned in the same direction and touching. They grew their own nanotubes on a 4-by-5-centimeter silicon wafer, producing what was in essence a nanoscale carpet of fibers sticking straight up. They laid a piece of Teflon film over the nanotubes and then rolled a rod over the film to press the nanotubes flat in the same direction. The nanotubes stuck to the Teflon and came off the silicon wafer, creating a nanoscale structure resembling a cloth.
Next, they needed to make electrodes that would be attached to the sheet to create their carbon nanotube heater. They took a rectangular Teflon-nanotube sheet and attached strips of copper mesh running down two ends of the rectangle, perpendicular to aligned nanotubes.
With their heater ready, they needed to see how well it would cure thermoset material compared to the traditional oven method. They stacked together 16 layers of prepreg thermoset sheets, which are sticky like duct tape, each 4-by-5-cm wide. Then they topped the stack with their Teflon-nanotubes sheet and ran electric current through the
Teflon-nanotubes sheet to heat it up. They built a second 16-layer stack of the prepreg sheets and heated it an oven. For both stacks, they raised the temperature to 121 degrees Celsius for three hours, then to 177 degrees Celsius for two hours, following the schedule recommended by the maker of the prepreg. Later tests would show that nanotube heaters could cure the material three times faster than an oven.
Once the curing was finished, the engineers compared how completely the nanotubes-heated and oven-heated samples cured. They found that the degrees of cure — with 100% being fully cured — were about 93% for the oven-made sample and 93% to 99% for the nanotube-made sample.
Recent testing
In 2018 and 2019, MIT engineers decided to find out how nanotube heating compared to traditional curing methods for thermoplastics, another type of carbon-reinforced material. This material is typically formed into airplane parts such as ribs, engine pylons or wing leading edges. Manufacturers traditionally cure prepreg sheets of this material in a hot press or pressurized oven, where it melts and then hardens as it cools.
For this testing, the engineers wanted to try commercially available nanotube sheets for the heaters instead of making their own, because the sheets would be easier to adopt for large-scale production in the future. But first, they needed to make sure the commercial sheets wouldn’t melt or disintegrate at the high temperatures — at least 400 degrees Celsius — needed to cure the thermoplastics.
The engineers ran electric current through patches of the nanotube material, each 2-by-1.5-cm across, to heat them to between 556 and 562 degrees Celsius. The patches were not affected.
They were then confident that the commercial nanotube sheets would not melt or disintegrate, but they still needed to make sure that their process would result in cured thermoplastic patches that were just as strong as those made by the traditional heating methods. So they made three sets of samples that they could compare: samples made by the nanotube heaters, in a pressurized oven and in a hot press.
The team divvied up the work. The MIT engineers made 18- and 24-ply composites with the nanotube heater as the top layer. Meanwhile, Teijin Carbon America — the U.S. subsidiary of a Tokyo-based carbon-fiber manufacturer and maker of the prepreg thermoplastic composite material — cured 18- and 24-ply composites, both in a pressurized oven at the University of Dayton Research Institute and with a hot press at its plant in Kettering, Ohio.
Now, the engineers had to figure out how the samples from the three manufacturing methods compared structurally. They calculated the percentage of crystalline structures in the samples to see how well the samples had hardened. They also scanned the samples with an X-ray microscope to look for voids, which signify structural weakness and can lead to cracks when a component is squeezed, bent or sheared. The engineers found that the samples produced by the nanotube heaters were just as structurally sound, or better in some cases, as those made by the pressurized oven and the hot press.
More work lies ahead, such as to find out exactly how quickly composites can be cured. “The question is: How far can you go? The heaters heat really fast. The polymer can cure really fast as well,” Wardle says. The MIT and Metis engineers didn’t try to optimize the curing period with the nanotube heaters, so adjusting the temperature recipe could probably cut the cure time in a half again, Wardle predicts.
With the out-of-oven process, the MIT team has “demonstrated that we can bake the cake in one hour, as opposed to three hours.”
Brian Wardle, MIT professor

About Keith Button
Keith has written for C4ISR Journal and Hedge Fund Alert, where he broke news of the 2007 Bear Stearns hedge fund blowup that kicked off the global credit crisis. He is based in New York.
Related Posts
Stay Up to Date
Submit your email address to receive the latest industry and Aerospace America news.
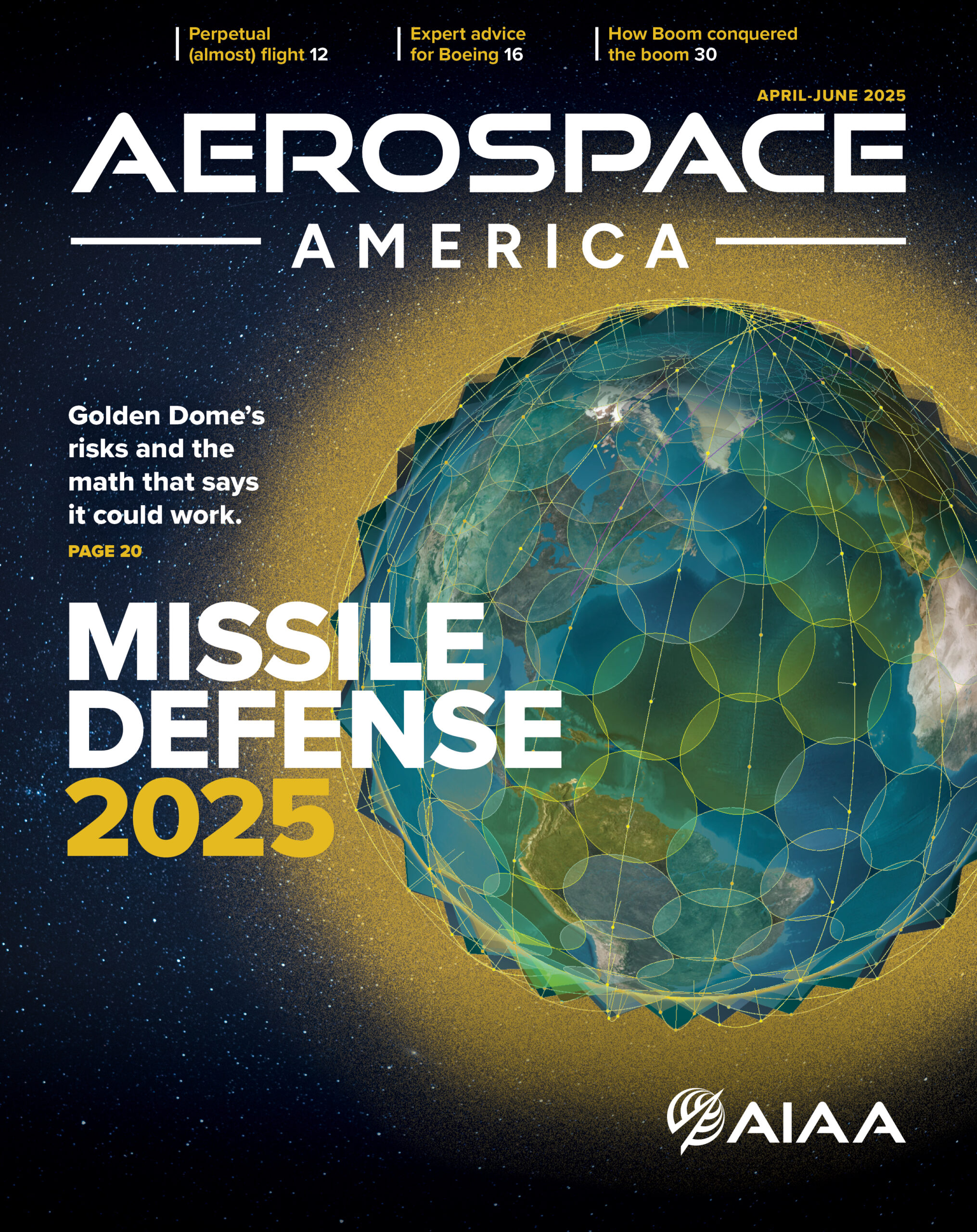
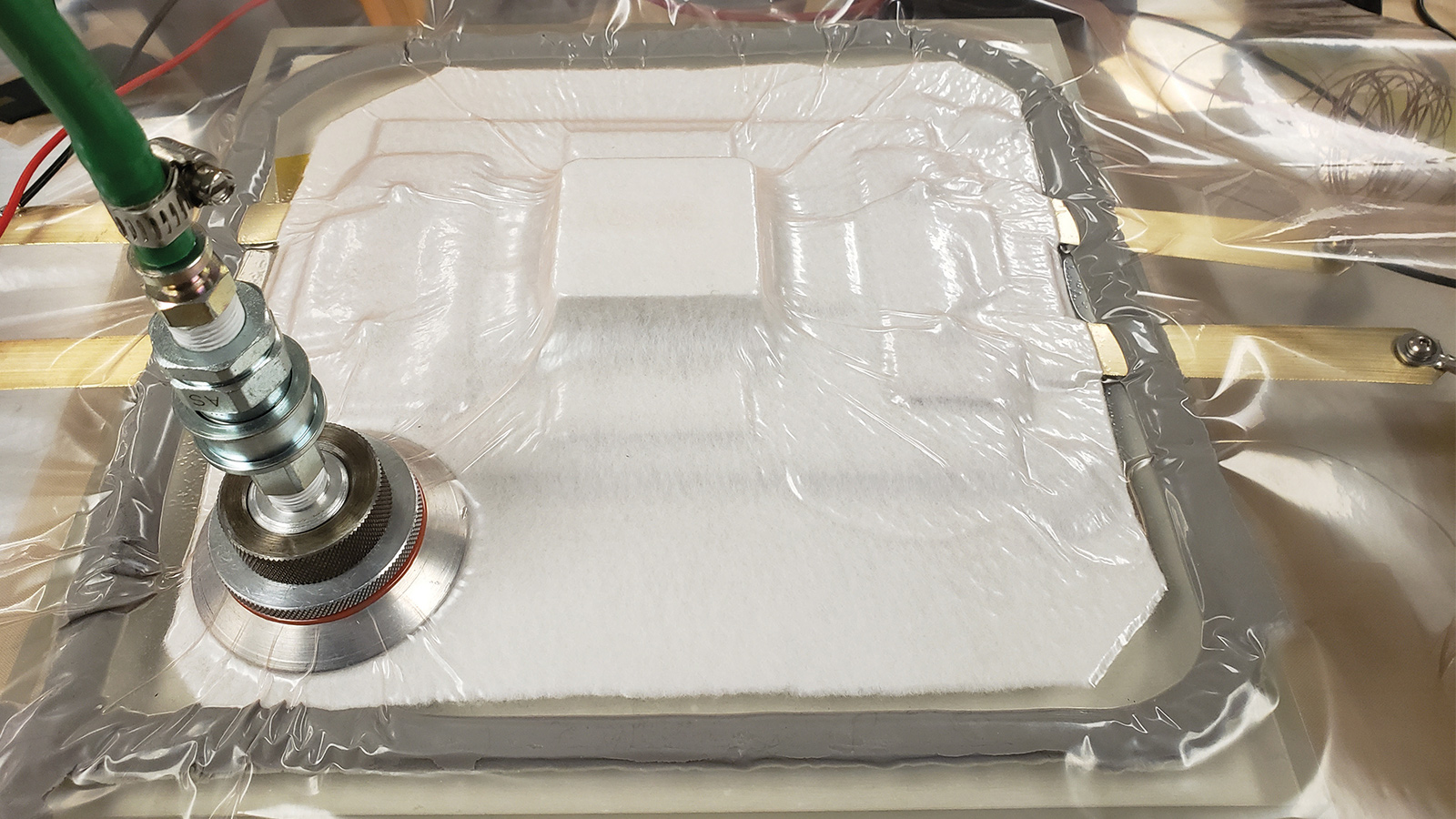
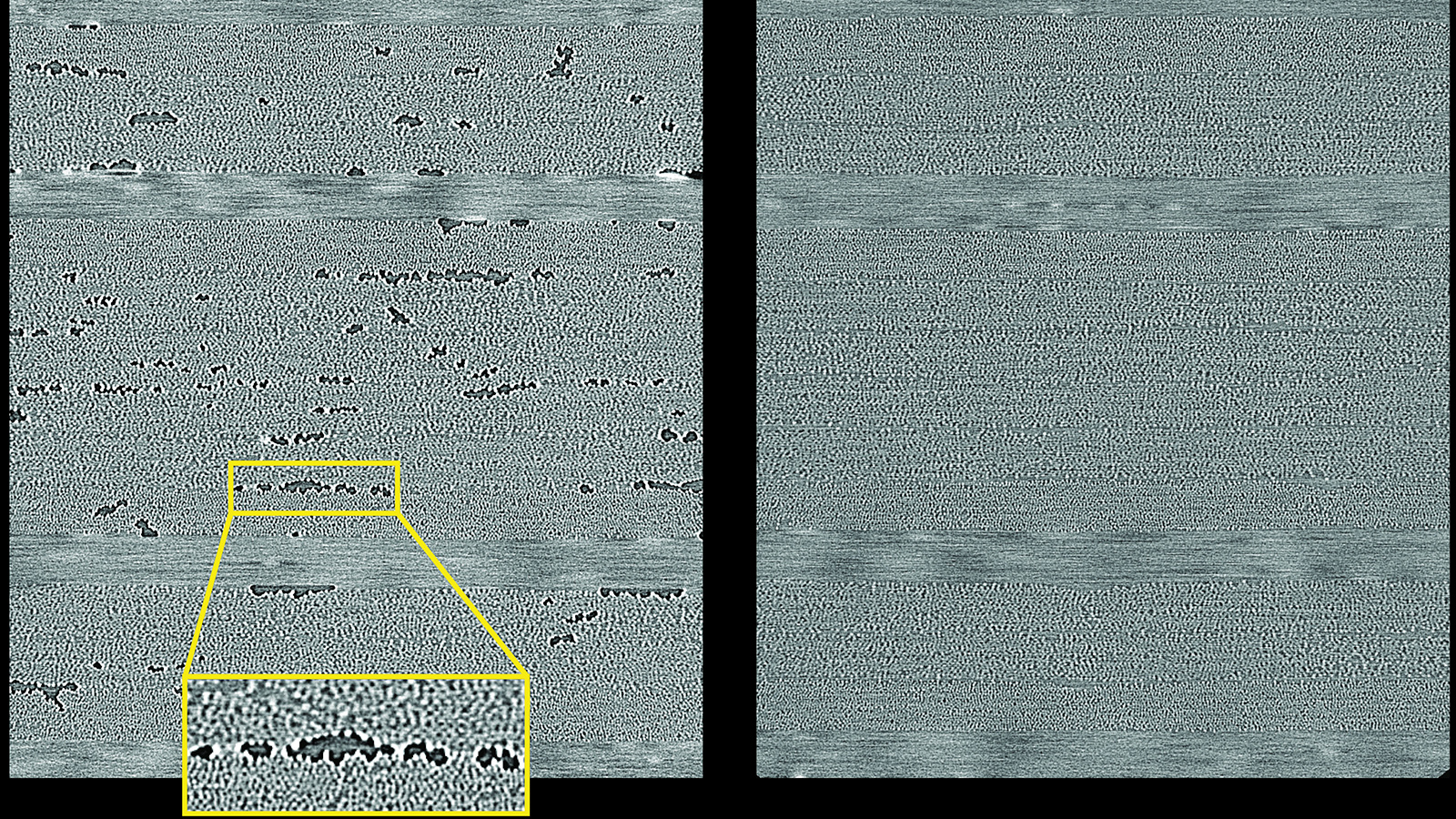